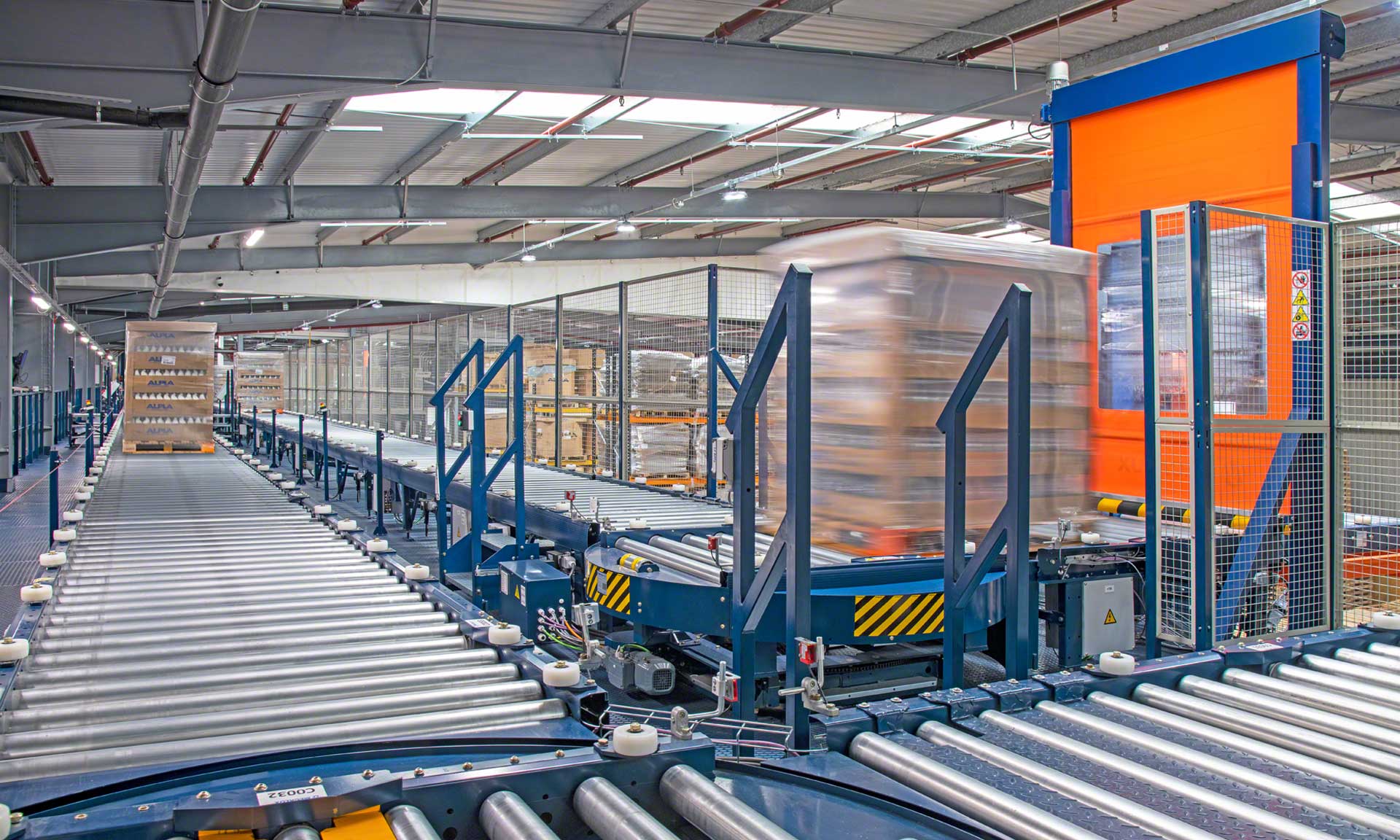
ALPLA installiert ein automatisches Fördersystem in seinem Werk in Golborne (UK)
Der weltweit führende Entwickler und Hersteller von Kunststoffverpackungssystemen ALPLA bewegt dank eines automatisierten Fördersystems 2.500 Paletten pro Tag.
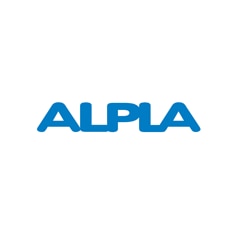
ALPLA hat zur Verbindung des Lagers mit den Produktionslinien am Standort Golborne einen Kreislauf aus automatischen Fördersystemen installiert. Der weltweit führende Entwickler und Hersteller von Kunststoffverpackungssystemen befördert dank eines automatischen Fördersystems 2.500 Paletten pro Tag.
ALPLA: innovative Verpackungslösungen
ALPLA wurde in Österreich gegründet und ist eines der weltweit führenden Unternehmen im Bereich von Verpackungslösungen. Das Unternehmen ist weltweit für die Herstellung von Kunststoffverpackungen von höchster Qualität bekannt. Seine Behälter und Verpackungen werden in zahlreichen Branchen eingesetzt, z. B. in der Lebensmittel-, Pharma- und Kosmetikindustrie. Der Schwerpunkt des Unternehmens liegt auf der Entwicklung einer nachhaltigen und umweltfreundlichen Produktion dank der eigenen Recyclinganlagen.
- Gründungsjahr: 1955
- Internationale Präsenz: 45 Länder
- Produktionszentren: 177
- Anzahl Mitarbeiter: Über 22.100 Personen
- Umsatz: 4 Milliarden Euro im Jahr 2021
HERAUSFORDERUNGEN
|
LÖSUNGEN
|
VORTEILE
|
---|
Wie lässt sich ein Lager automatisch mit der Produktionsanlage verbinden, wenn zwischen beiden Gebäuden ein Abstand von 70 m und eine Straße liegen? Die ALPLA-Gruppe, eines der führenden Unternehmen für industrielle Verpackungsprodukte (Vorformlinge, Kunststoffflaschen...), konnte diese Aufgabe dank einer technischen Lösung von Mecalux bewältigen. „Dank der installierten logistischen Lösung mit Fördersystemen und automatischen Palettenliften konnten wir unsere Umschlagkosten und Kohlendioxidemissionen drastisch senken, wodurch unser Unternehmen nachhaltiger und umweltfreundlicher geworden ist,“erklärt Liam Grimwood, technischer Leiter im britischen Werk von ALPLA.
ALPLA ist in 45 Ländern vertreten und erzielte 2021 einen Umsatz von vier Milliarden Euro, 8,4 % mehr als im vergangenen Jahr. Das Unternehmen verfolgt in Großbritannien einen noch nie dagewesenen Wachstumsplan und verfügt seit einigen Jahren über eine moderne Produktionsstätte in Golborne, in der Nähe von Manchester und Liverpool.
Der Logistikkomplex besteht aus zwei durch eine öffentliche Straße getrennten Gebäuden - eines für die Produktionslinien und eines für den Lagerbereich. „Früher waren wir stark auf den Einsatz schwerer Fahrzeuge angewiesen, um die Waren manuell von der Produktionsstätte zum Lager zu transportieren“, sagt Grimwood.
Mit dem steigenden Produktionsvolumen stiegen auch die Bewegungen und der Transport von Lastwagen zwischen den Produktions- und Lagergebäuden von ALPLA. Irgendwann kam der Punkt, an dem die manuelle Beförderung von Waren unhaltbar wurde. „Wir brauchten ein System, mit dem wir die beiden Gebäude miteinander verbinden und die Waren automatisch von der Produktionsstätte zum Lager befördern konnten. Wir wollten uns von der manuellen Handhabung und dem Einsatz schwerer Fahrzeuge verabschieden“, räumt der technische Leiter des britischen ALPLA-Werks ein.
Die Lösung für den Bedarf von ALPLA war die Errichtung eines acht Meter hohen Hochtunnels, der die öffentliche Straße überquert, um die Produktionsanlage und den Lagerbereich zu verbinden.
„Wir haben uns für Mecalux entschieden, weil das Unternehmen Erfahrung mit der Umsetzung von Projekten wie unseres hat. Die Erfahrung und das Fachwissen des technischen Teams und des Projektmanagers, die uns während der gesamten Zeit begleitet und beraten haben, waren ebenfalls ausschlaggebend für unsere Wahl“, sagt Grimwood.
Kommunikation durch automatische Systeme
„Wir befördern jeden Tag etwa 2.500 Paletten, dank eines automatisierten Transportsystems, das rund um die Uhr und sieben Tage die Woche in Betrieb ist“, sagt Grimwood stolz.
Das von Mecalux installierte System umfasst einen doppelten Kreislauf von Fördersystemen, die die Waren von der Produktion zum Lager befördern. „Es werden hauptsächlich Paletten mit Kartonschalen, die leere Flaschen, Kisten und Metallbehälter mit Polyethylenterephthalat-Vorformlingen enthalten, transportiert“, erklärt der technische Leiter des britischen ALPLA-Werks.
Fördersysteme sind ein automatisches Warentransportsystem mit einem Satz Rollen, die die Last tragen und sie entlang des Kreislaufs bewegen.
Das System verfügt über Elektromotoren, die die Ladeeinheiten auf kontrollierte und sichere Weise bewegen. Rollenförderer sparen Zeit und steigern die Effizienz bei sich wiederholenden Beförderungen von Lasten und mit vordefinierten Kreisläufen.
Zusätzlich zu den Fördersystemen wurden sieben automatische Aufzüge installiert, um die Paletten vertikal zu bewegen. Mit den Aufzügen wird die Lücke zwischen dem Kreislauf der Fördersysteme in Bodennähe und dem Hochtunnel überbrückt. Die Paletten können auf diese Weise den gesamten Weg von der Produktionsanlage bis zum Lager vollständig robotisiert zurücklegen.
Am Anfang des Kreislaufs der Fördersysteme und genau dort, wo die Paletten die Produktionslinien verlassen, wurde eine Kontrollstation (PIE) eingerichtet. Dieses automatische Mess- und Qualitätskontrollsystem für Paletten ist unerlässlich, damit sowohl die Waren als auch die Paletten, die in den Kreislauf des Fördersystems gelangen, einwandfrei transportiert werden können und keine Unfälle verursachen. Die Kontrollstation prüft, ob die Abmessungen, das Gewicht und der Zustand der Paletten den Spezifikationen der Anlage entsprechen.
Hauptbestandteile der Fördervorrichtungen mit Rollen
- Rollen. Metallzylinder mit einer Welle und zwei Lagern. Nacheinander angebracht, tragen sie das Gewicht der Palette und transportieren diese bis zum Ende des Förderkreislaufs.
- Rahmen und Füße aus Metall. Sie dienen als Stütze für die Rollen und werden je nach dem Gewicht, das sie tragen müssen, aus verschiedenen Stahlsorten hergestellt. Ihre Funktion: Sie geben die Richtung des Förderkreislaufs vor.
- Elektronische Bauteile. Die Lastenbewegung im Kreislauf wird durch elektrische Komponenten, Motoren und Schaltkästen ausgelöst. Die erforderliche Leistung hängt von der benötigten Geschwindigkeit und dem Gewicht der zu bewegenden Lasten ab.
- Sicherheitselemente. Mechanische Vorrichtungen oder Sensoren, wie z. B. Erkennungsstopps oder Lichtschranken, sorgen für die Sicherheit der Anlage. Außerdem kennen sie jederzeit die Position der Lasten und übermitteln diese Information an die Steuerungssoftware.
Effiziente Fertigungslogistik
„ALPLA in Golborne befindet sich in einer starken Position und hat die Chance auf weiteres Wachstum“, enthüllt Grimwood. Zur weiteren Konsolidierung seiner Präsenz auf dem britischen Markt fördert das Unternehmen die Lean-Methode in seiner Logistik. Damit sollen die Aktivitäten gefördert werden, die einen Mehrwert für das Unternehmen darstellen, um den Materialfluss zu erhöhen und die Kosten zu minimieren.
Dank der Lösung von Mecalux verfügt ALPLA über eine effiziente Logistik, die durch automatische Transportsysteme mit der Produktion verbunden ist. In der heutigen Industrie ist ein flexibles und diversifiziertes Produktionssystem erforderlich. Eine effiziente Produktionslogistik ist dabei ausschlaggebend für einen erfolgreichen Kundenservice. Dank der installierten Lösung ist die Lieferkette von ALPLA effizienter, optimiert und für die aktuellen und zukünftigen Herausforderungen gerüstet.
Mit der von Mecalux installierten automatischen Transportlösung haben wir die Kosten und den CO2-Ausstoß gesenkt und können außerdem rund 2.500 Paletten pro Tag rund um die Uhr an sieben Tagen in der Woche transportieren.
Galerie
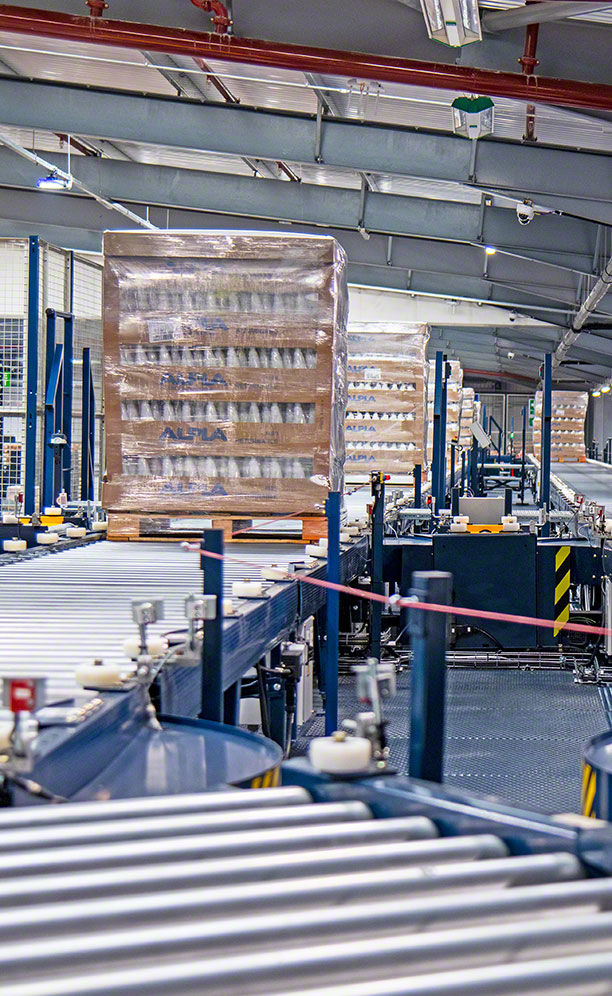
Automatische Palettenfördersysteme im Logistikzentrum von ALPLA
Fragen Sie einen Experten