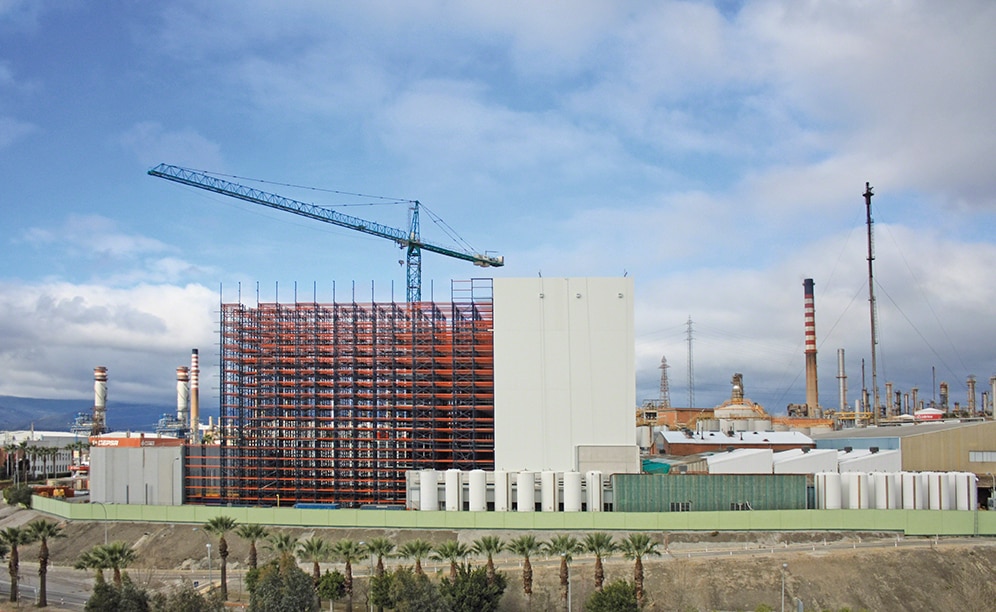
Mecalux baut für Cepsa ein 37 m hohes automatisiertes Lager, das mit den Produktionslinien verbunden ist
Cepsa: ein Erfolgsbeispiel für die Integration von Logistikprozessen
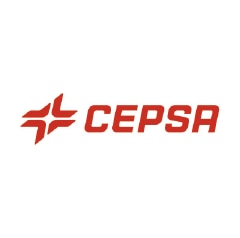
Das Energieunternehmen Cepsa beauftragte Mecalux mit dem Bau eines schlüsselfertigen, 37 m hohen automatischen Lagers in San Roque (Provinz Cádiz, Spanien). Im Lieferumfang war auch die Lagerverwaltungssoftware Easy WMS von Mecalux enthalten, die alle im Zentrum ablaufenden Vorgänge steuert.
Informationen zu Cepsa
Cepsa ist ein Energiekonzern, der sich zu 100 % im Besitz von IPIC befindet und über 10.000 Mitarbeiter beschäftigt und dessen Aktivität sich auf alle Phasen der Wertschöpfungskette von Mineralölen erstreckt: Exploration und Produktion von Öl und Gas, Raffinierung, Transport und Vermarktung von Erdölprodukten und Erdgas, Biokraftstoffen, Kraft-Wärme-Kopplung und Stromhandel.
Das Unternehmen hat einen wichtigen petrochemischen Bereich geschaffen, der eng mit der Erdölraffinerie verknüpft ist, in der es Rohstoffe für die Herstellung von Produkten mit hoher Wertschöpfung produziert und vermarktet, die hauptsächlich für die Herstellung von Kunststoffen der neuen Generation und biologisch abbaubaren Waschmitteln verwendet werden. Es ist in Spanien sehr präsent und ist durch eine zunehmende Internationalisierung auf mehreren Kontinenten tätig, um seine Produkte auf der ganzen Welt zu vertreiben.
Anforderungen von Cepsa
Das Unternehmen hatte hohe Logistikkosten, da sich sein Lager für Fertigprodukte, im Gegensatz zum Rohstofflager, in einiger Entfernung von den Produktionsanlagen befand.
Angesichts dieser Situation wendete sich Cepsa an Mecalux mit der Absicht, ein neues automatisches Lager mit der größtmöglichen Lagerkapazität auf dem Gelände zu errichten, auf dem sich das herkömmliche Lager und die Wartungswerkstätten befanden. Außerdem sollten unbedingt Kommissionierstationen zur Beschleunigung der Auftragszusammenstellung eingerichtet werden.
Die Automatisierung sollte direkt am Ausgang der Produktionslinien beginnen, um den Einsatz von Personal auf die Vorgänge zu beschränken, die unbedingt einen manuellen Eingriff erfordern.
Es war notwendig, die verschiedenen Modelle und Abmessungen der Paletten zu berücksichtigen, und in den Regalen sollten Europaletten der folgenden Maße direkt gelagert werden können: 800 x 1200 mm, 1000 x 1200 mm, 1150 x 1200 mm und 1200 x 1200 mm.
Gleichzeitig waren der Eingang und die anschließende Einlagerung von Paletten mit anderen Abmessungen, hauptsächlich von außerhalb, zu berücksichtigen. Ein Teil dieser Paletten enthält Produkte, die für die Produktion benötigt werden, weshalb ebenfalls die Lieferung aus dem Lager in diesen Bereich vorzusehen war.
Eine weitere Forderung von Cepsa bestand darin, dass alle Phasen des Entwurfs und Baus des Lagers, einschließlich der Lieferung der notwendigen Software zur korrekten Abwicklung aller internen Abläufe, aus einer Hand durchgeführt werden sollten. Kurzum, es sollte ein schlüsselfertiges Projekt von Anfang bis Ende durchgeführt werden, ohne dass die Produktion während dieser Zeit unterbrochen wird.
Merkmale eines schlüsselfertigen Lagers
Das Konzept des schlüsselfertigen Lagers für Cepsa umfasste folgende Faktoren:
- Planung, Ausarbeitung und Legalisierung des Projekts unter Einbeziehung aller Bereiche, aus denen das Lager besteht, und unter Berücksichtigung der verschiedenen geltenden Vorschriften.
- Abriss der vorhandenen Gebäude auf dem Gelände, auf dem das Lager errichtet werden sollte, sowie dessen anschließende Vorbereitung.
- Vorbereitung des Untergrunds und Konstruktion der Betonplatte und der Außenwände mit der notwendigen Festigkeit und Ebenheit für diese Art von Lagern.
- Lieferung und Montage der Regale und der notwendigen Strukturen für den Bau des selbsttragenden Lagers.
- Lieferung, Montage und Inbetriebnahme von Fördermitteln: Regalbediengeräte (Lagerroboter), Fördervorrichtungen, Kontrollstationen, Vorrichtungen zur Erleichterung der Kommissionierung und alle erforderlichen Hilfselemente.
- Lieferung und Montage der Verkleidungspaneele für das Lager sowohl für die Seitenwände als auch für das Dach.
- Bau eines angrenzenden Gebäudes, in dem der Eingangsbereich für von außerhalb kommende Ware, Lagerausgänge, Versand und Kommissionierung untergebracht werden soll.
- Lieferung und Montage der Brandschutzvorrichtungen innerhalb des Lagers und in den angrenzenden Bereichen unter Berücksichtigung der geltenden Vorschriften. In diesem Fall verfügte Cepsa in der Fabrik bereits über einen Wassertank und die erforderlichen Pumpanlagen.
- Installation von Abschlusstoren zwischen dem Lager und den angrenzenden Gebäuden, die sich im Brandfall automatisch schließen.
- Elektroinstallation.
- Lagerverwaltungssystem (LVS). Dieses System muss mit dem ERP-System SAP bzw. dem Haupt-Computersystem von Cepsa verbunden sein, um Anweisungen und Informationen auszutauschen.
Ein Hochregallager in Silobauweise als Lösung
Von Beginn an arbeitete Mecalux eng mit den Verantwortlichen der verschiedenen bautechnischen Bereiche und der Logistikleitung von Cepsa zusammen, um herauszufinden, welche Lösung am besten den Anforderungen des Unternehmens entspricht.
Nach der ausführlichen Analyse der vorgegebenen Spezifikationen schlug Mecalux vor, ein automatisches Hochregallager in Silobauweise mit 37 m Höhe und einer Lagerkapazität von über 28.000 Paletten auf einer Fläche von nur 4150² zu errichten.
Da die verfügbare Fläche beschränkt war, wurde geplant, den Eingang der aus den Produktionslinien kommenden Ware auf der einen Seite des Lagers und den Ausgang auf der gegenüberliegenden Seite anzulegen. Die Trennung von Eingangs- und Ausgangsbereich ist nicht üblich, aber im Falle von Cepsa erwies sich dieses Vorgehen als die beste Lösung.
Bei einem Hochregallager in Silobauweise sind die Regalanlagen, an denen die Seitenwände befestigt werden, ein fundamentaler Teil der Struktur des Gebäudes. Neben ihrem Eigengewicht müssen die Regale das Gewicht der gelagerten Paletten tragen und den Windkräften, den Fördermitteln (Lagerroboter), möglichen Erdbeben, abhängig von dem am Aufstellungsort geltenden Koeffizienten, und der gemäß den Vorschriften zu berücksichtigenden Schneelast standhalten.
Die Rohre des Brandschutzsystems werden an den Regalzeilen selbst installiert und befestigt, wodurch sie vor möglichen Stößen geschützt sind und eine ausreichende Löschwassermenge für die Paletten zur Verfügung stellen können. Um die korrekte Funktion aller Abläufe zu gewährleisten, wurde das Lagerverwaltungssystem Easy WMS von Mecalux installiert, das für die Steuerung und Kontrolle aller Prozesse des Logistikzentrums zuständig ist.
Das Lagerinnere
Es besteht aus sieben Gängen mit Regalanlagen doppelter Tiefe auf beiden Seiten, in denen jeweils ein fast 34 m hohes Zweimast-Regalbediengerät mit Teleskopgabeln doppelter Tiefe verkehrt.
In der Länge verfügt das Lager über 19 Regalmodule mit 18 Ladeebenen in der Höhe, die je nach Modell und Abmessungen zwei oder drei Paletten aufnehmen können.
Von der dritten bis zur 18. Ebene wurde jeweils eine zusätzliche Lagerposition eingerichtet, die an die Stellen zur Platzierung und Entnahme der Fördervorrichtungen grenzt, welche sich an den Enden jeder Ladegasse befinden.
Regaleingang auf Produktionsseite
Auf dieser Seite findet die Einlagerung der Fertigprodukte statt, obwohl ebenfalls Ausgänge für Zusatzprodukte, die für die Produktion benötigt werden, vorhanden sind.
Direkt nachdem die von den Produktionslinien kommende Ware palettiert wurde, sorgt das von Mecalux installierte System für die Einlagerung der Paletten und den späteren Transport in den Versand- und Kommissionierbereich.
Bei genauer Betrachtung des Grundrisses ist zu erkennen, dass es außer dem Produktionsbereich, der direkt an den hinteren Teil des Lagers grenzt, einen Bereich gibt, der für die Abfüllung von IBC-Containern (speziell für die Lagerung und den Transport von Flüssigkeiten bestimmt) reserviert ist.
Dieser Bereich ist durch ein zweites Shuttle-Car und den Regaleingang auf Produktionsseite ebenfalls mit dem Lager verbunden.
Regaleingang auf Versandseite
Es wurden direkte Ausgangsförderer, die zu den Laderampen führen, eingerichtet (fünf mit Ketten und drei mit Rollen), die die Paletten auf der am besten geeigneten Seite platzieren. In diesem Bereich findet der Wareneingang von außerhalb statt.
Zu diesem Zweck wurden die erforderlichen Fördervorrichtungen und Elemente installiert, einschließlich der Möglichkeit, Paletten, die ungeeignete Maße haben oder sich in schlechtem Zustand befinden, auf geeignete Paletten zu setzen.
Hier befinden sich auch die Kommissionierstationen mit entsprechenden Fördermitteln und eine freie Fläche, auf der bei Bedarf zwei weitere Stationen installiert werden können. Es ist auch ein Verfahrwagen vorhanden, der als Verbindungsglied zwischen den einzelnen Positionen dient.
Kommissionierbereich
Er befindet sich zwischen den Fördervorrichtungen am Regaleingang und der Reihe von Elementen, aus denen die Eingangsstation von den Laderampen aus besteht. Es gibt zwei Kommissionierstationen, und jede von ihnen verfügt über die folgenden Elemente:
- U-förmiger Kreislauf, der an die Fördervorrichtungen am Regaleingang angrenzt und Platz für drei Ursprungspaletten bietet (zwei davon in Wartestellung).
- Arbeitsplattform mit Zugang zu den vier Seiten der Palette, die sich in der mittleren Position befindet. Hier erfolgt die eigentliche Kommissionierung.
- Drei Positionen für die Zielpaletten, um drei Aufträge gleichzeitig zusammenstellen zu können. Sie befinden sich an der gegenüberliegenden Seite der Arbeitsplattform.
- Ein Saugheber für Behälter und ein Hebegerät mit Klammern für Fässer, die an der darüberliegenden Struktur aufgehängt sind, sich auf drei Achsen bewegen können und die manuelle Handhabung überflüssig machen, vor allem bei schweren Behältern und Fässern.
- Ein Computerterminal und zwei Drucker.
Außerdem befindet sich hier eine freie Fläche, die für eine zukünftige Verdoppelung der Anzahl der Kommissionierstationen vorgesehen ist.
Die Paletten mit abgeschlossenen Bestellungen werden von außerhalb mithilfe des Shuttle-Cars in die Eingangsstation für Paletten gesetzt. Diese Paletten werden automatisch umreift, bevor sie in die Wartepositionen innerhalb des Lagers oder direkt zum zugewiesenen Ausgangskanal befördert werden. In beiden Fällen werden sie von den Fördersystemen am Regaleingang transportiert.
Verlauf der Bauarbeiten
Hier wird der Verlauf der gesamten Bauarbeiten, vom Abriss des alten Gebäudes bis zur Inbetriebnahme der Anlage, gezeigt.
Auf den Bildern sind die verschiedenen Phasen beim Bau dieses Lagers zu erkennen. Die perfekte Koordination aller am Bau beteiligten Teams und die Tatsache, dass Mecalux als alleiniger Lieferant dieses schlüsselfertigen Projekts fungierte, hat zu diesem großen automatischen Lager geführt, das mit den Produktionsprozessen vernetzt ist.
Der Bau wurde durchgeführt, ohne das Cepsa die Belieferung jemals einstellen musste.
Verwaltungssystem Easy WMS: das Herz der Installation
Easy WMS steuert sämtliche Eingänge, die Platzierung im Lager, den Bestand, die Platzierungsregeln, die Ein- und Auslagerung, die Paletten, die an die Kommissionierstationen transportiert werden müssen, die Kommissionierung selbst, den Rücktransport ins Lager usw.
Galileo, die Steuerungssoftware von Mecalux, führt die Bewegungen der verschiedenen Vorrichtungen und Geräte aus. Außerdem kontrolliert sie den Zustand der Elemente, aus denen die Förderkreisläufe, die Regalbediengeräte und die internen und externen Sicherheitsvorrichtungen bestehen, sowie der anderen Elemente, die mit ihnen interagieren. Die Synchronisierung beider Systeme und die angewandte Technologie ermöglichen dem Anwender eine grafische Ansicht der Installation und geben ihm die Möglichkeit, sichere Tätigkeiten vom Steuerpult aus durchzuführen.
Vorteile für Cepsa
- Hohe Lagerkapazität auf begrenztem Raum: In dem Hochregallager in Silobauweise lassen sich 28.630 Paletten auf einer Fläche von 4150 m² lagern.
- Kosteneinsparung: Durch die Automatisierung des Hochregallagers in Silobauweise und die direkte Vernetzung mit den Produktionslinien konnte Cepsa die Effizienz verbessern und Personal- und Logistikkosten einsparen.
- Vollständige Kontrolle: Dank der LVS Easy WMS von Mecalux steuert Cepsa alle Prozesse und Vorgänge innerhalb des Lagers.
Automatisches Hochregallager von Cepsa (Spanien) | |
---|---|
Lagerkapazität: | 28.630 Paletten |
Höchstgewicht der Paletten: | 1.000 kg |
Höhe des Lagers: | 37 m |
Anzahl der Regalbediengeräte: | 7 |
Art der Regalbediengeräten: | Zweimast-Geräte |
Gabeltyp: | Doppelte Tiefe |
Anzahl der Verfahrwagen: | 3 |
Bauweise: | Selbsttragend |
Galerie
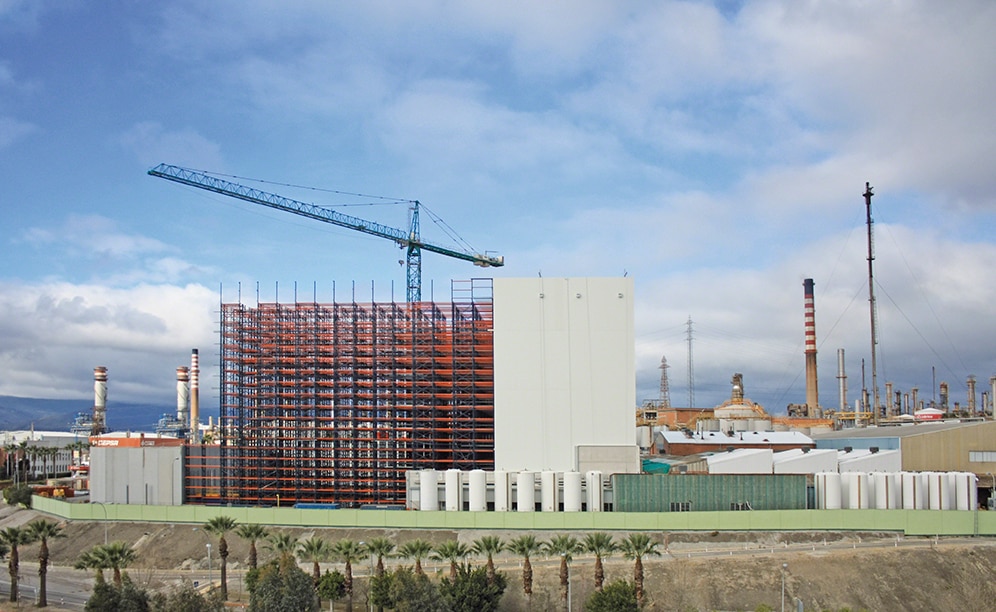
Mecalux baut für Cepsa ein 37 m hohes automatisches Lager mit einer Kapazität für mehr als 28.000 Paletten
Fragen Sie einen Experten