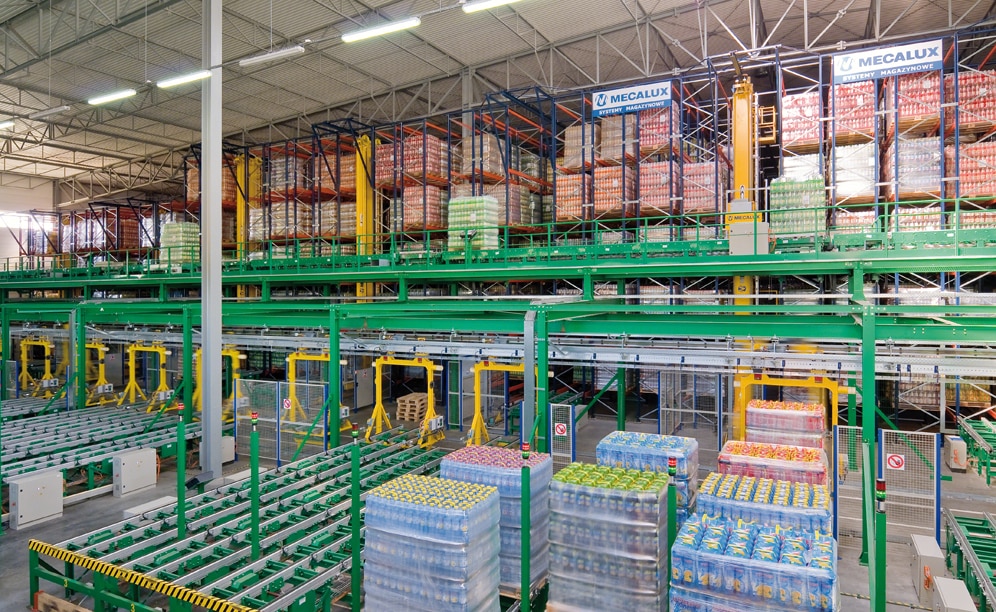
Ein automatisiertes Hochleistungslager: 200 Paletten/Stunde und 18.000 gelagerte Paletten
Mecalux hat ein automatisiertes Lager geliefert

Um ihr Wachstumstempo beibehalten zu können, wollte die Firma Zbyszko Company die Kapazität und Geschwindigkeit ihres Lagers erhöhen und ihre Produktions- und Lagerprozesse miteinander verbinden. Um diese Bedürfnisse zu erfüllen, hat Mecalux ein automatisches Lager errichtet, das durch einen 100 m langen Tunnel mit Fördervorrichtungen mit der Produktionsstätte verbunden ist. Die gesamte Anlage wird vom Lagerverwaltungssystem Easy WMS von Mecalux koordiniert und gesteuert.
Informationen zu Zbyszko Company: Anforderungen
Zbyszko Company, ein auf die Herstellung von Limonaden, Erfrischungsgetränken und aromatisiertem Wasser spezialisiertes Unternehmen, wurde 1993 von Zbigniew Bojanowicz in der polnischen Stadt Białobrzegi gegründet. In nur 10 Jahren ist Zbyszko Company auf spektakuläre Weise gewachsen, sodass das Unternehmen nun zu den erfolgreichsten polnischen Herstellern auf dem Markt der natürlichen Getränke gehört.
Angesichts des unaufhörlichen Fortschritts hat Zbyszko Company Mecalux mit dem Bau eines neuen Lagerzentrums beauftragt, das alle logistischen Aktivitäten der Firma zentralisieren und mit den derzeit innovativsten Technologien ausgerüstet sein soll, um die hohe Produktionsleistung bewältigen zu können und Logistikkosten zu sparen.
Um den internen Transport zu beschleunigen, bestand eine der wesentlichen Anforderungen des Projekts darin, eine direkte Verbindung zwischen dem Produktionsbereich und dem Lager zu schaffen und die Lagerprozesse so weit wie möglich zu automatisieren, um die Wettbewerbsfähigkeit von Zbyszko Company auf dem Markt zu erhöhen.
Vorgeschlagene Lösung: Verbindung von Produktionsbereich und Lager
Mecalux hat ein automatisiertes Lager geliefert, das durch einen 100 m langen Hochtunnel, durch den die bereits palettierte Ware auf einem Förderkreislauf mit Rollen transportiert wird, mit dem Produktionsbereich verbunden ist.
Die am Anfang des Kreislaufs innerhalb des Produktionsbereichs vorhandene Kontrollstation überprüft, ob die Abmessungen und die Qualität der Paletten den Anforderungen entsprechen. Die Fördervorrichtungen bestehen aus zwei Strecken, eine in jeder Richtung, die unabhängig voneinander arbeiten, auch wenn sie parallel zueinander verlaufen.
Innerhalb des Lagers gibt es zwei Ebenen mit Fördervorrichtungen. Die obere Ebene ist für den Wareneingang bestimmt, während die untere Ebene für den Warenausgang vorgesehen ist. Es besteht jedoch auch die Möglichkeit, dass auf dieser Ebene von außerhalb kommende Ware, die für das Silo oder den Produktionsbereich bestimmt ist, ankommt. Um die Vorgänge zu trennen, wurde direkt über den Laderampen an einem Ende ein Förderer für den Eingang in das Lager mit einem Lastenaufzug, der die Paletten auf die obere Ebene hebt, eingerichtet.
Um den Bewegungsfluss soweit wie möglich zu maximieren, wurde auf der unteren Ebene ein Kreislauf mit Elektrohängebahnen angelegt, der in der Lage ist, Waren mit einer Geschwindigkeit von über 100 m/min zu transportieren, und das Lager mit dem Bereich zur Ladevorbereitung verbindet. Dieses System ist ideal, um verschiedene, voneinander entfernte Punkte der Anlage in konstantem Rhythmus miteinander zu verbinden.
Das Lagerinnere
Das Lager nimmt eine Fläche von 7000 m2 ein und wurde in einem nur 11 m hohen Gebäude errichtet. Durch die Installation von Regalbediengeräten ist die Lagerung von bis zu 18.000 Paletten trotz dieser beschränkten Höhe möglich.
Da nur wenige Artikelarten gelagert werden, entschied man sich für den Einbau von Regalen doppelter Tiefe, eine Methode, die häufig in automatischen Logistikzentren, die eine hohe Lagerkapazität benötigen, angewandt wird.
Die Regale werden von elf vollautomatischen Regalbediengeräten bedient, die sich rasch in ihren Gängen bewegen und Paletten mit einem Gewicht von bis zu 1000 kg handhaben können.
Expediciones
Die Regalbediengeräte sorgen für die automatische Entnahme der Ware, die aus dem Produktionsbereich kommt, und bringen sie zum entsprechenden Ausgangsförderer. Sobald sich die Paletten auf den Fördervorrichtungen befinden, werden sie von den Elektrohängebahnen in den ihnen zugewiesenen Bereich zur Ladevorbereitung gebracht.
Es gibt eine Vielzahl von Optionen für den Entwurf eines Kreislaufs mit Elektrohängebahnen. Im Fall von Zbyszko Company kam man zu dem Schluss, dass ein einfacher Kreislauf in Form einer Schleife, in dem sich 21 einzeln gesteuerte Wagen bewegen, die rentabelste und effiziente Lösung ist.
Die Software zur Steuerung der Wagen ist mit dem LVS für das gesamte Lager verbunden, welches wiederum mit dem ERP-System des Kunden verbunden ist.
Auf dem Bild rechts lassen sich die folgenden Bereiche unterscheiden:
- Lager
- Eingänge im oberen Teil
- Elektrohängebahnen
- Ladevorbereitung
- Eingangsförderer von den Laderampen
Lagerverwaltungssystem: Easy WMS von Mecalux
Zbyszko Company nutzt das Lagerverwaltungssystem Easy WMS von Mecalux, um alle innerhalb des Logistikzentrums anfallenden Bewegungen zu steuern und den verfügbaren Lagerraum auf effiziente Weise zu verwalten.
Easy WMS kommuniziert mit dem ERP-System SAP des Kunden, um Versand, Wareneingang, Vertrieb, Transfer und alle weiteren Aufgaben des Logistikzentrums bewältigen zu können.
Dieses leistungsstarke System gewährleistet die ordnungsgemäße Funktion der zur Automatisierung von Lagern verwendeten Geräte, wodurch die Transportbewegungen vereinfacht, menschliche Fehler beseitigt und Personalkosten verringert werden.
Vorteile für Zbyszko Company
- Raumnutzung: Das nur 11 m hohe Lager verfügt über eine Lagerkapazität von 18.000 Paletten auf einer Fläche von 7000 m2.
- Kosteneinsparungen: Durch den Hochtunnel, der das Lager mit dem Produktionsbereich verbindet, spart Zbyszko Company Logistikkosten.
- Steigerung der Produktivität: Die Auftragszusammenstellung ist schnell und effektiv dank der Geschwindigkeit der Regalbediengeräte und des installierten Kreislaufs von Fördervorrichtungen und Elektrohängebahnen, sodass bis zu 200 Paletten/Stunde versandt werden können.
Automatische Lager in Polen | |
---|---|
Lagerkapazität: | 18.000 Paletten |
Höchstgewicht pro Palette: | 1000 kg |
Höhe des Lagers: | 11 m |
Fläche des Lagers: | 7000 m2 |
Anzahl der Regalbediengeräte: | 11 |
Gabeltyp: | Doppelte Tiefe |
Anzahl der Wagen der Elektrohängebahn: | 21 |
Länge der Verbindungsbrücke: | 100 m |
Galerie
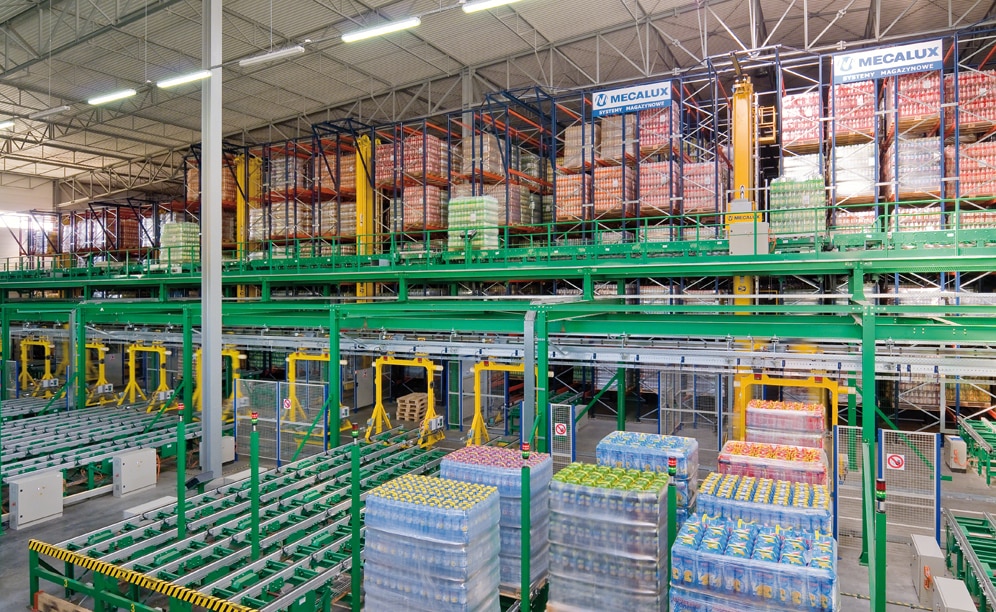
Das Lager nimmt eine Fläche von 7000 m² ein und wurde in einem nur 11 m hohen Gebäude errichtet
Fragen Sie einen Experten