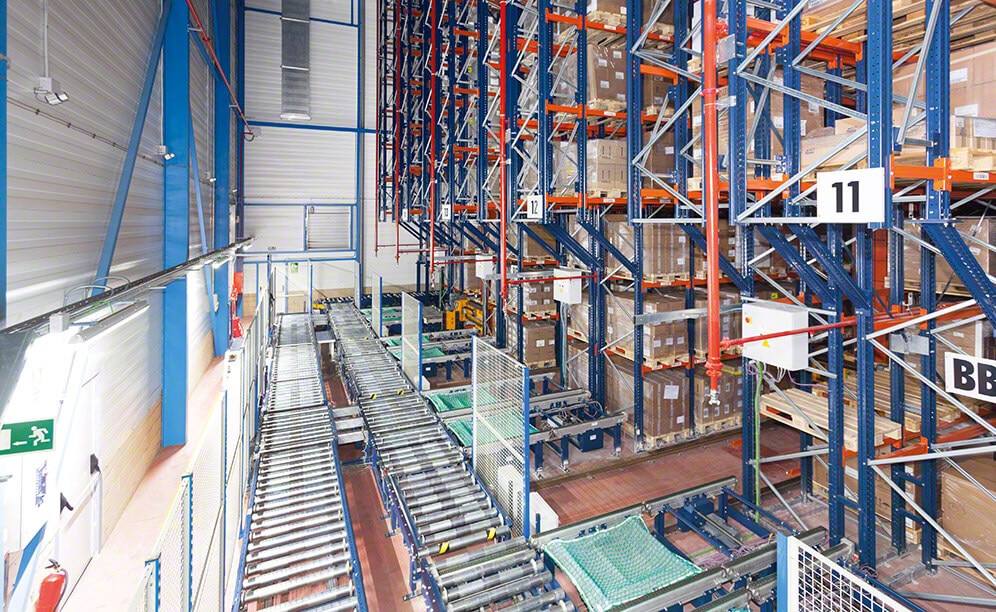
Disalfarm erhöht seine Kapazität und Produktivität mit der Automatisierung in verschiedenen Lagerbereichen
Einfache, budgetbewusste Automatisierung bei Disalfarm mit dreiseitigen Regalbediengeräten
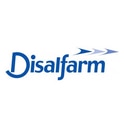
Dieses Logistikzentrum, das sich am Standort von Disalfarm in Rubí (Barcelona) befindet, wurde auf einer Fläche von 39.027 m² errichtet. Das heute vollautomatisch betriebene Lager, mit einer Lagerkapazität von mehr als 19.000 Paletten, konnte die Produktivität des Unternehmens merklich verbessern. Während der Erweiterung und Modernisierung des Lagers musste der Betrieb zu keinem Zeitpunkt unterbrochen werden.
Informationen zu Disalfarm
Disalfarm S.A. ist eine Logistikfirma, die in Spanien von den Pharmaunternehmen Bayer, Boehringer Ingelheim und Novartis gegründet wurde, um ihre nationalen Lagerungs- und Vertriebstätigkeiten zu konzentrieren.
Das Unternehmen begann seine Geschäftstätigkeit im Jahre 2000 mit dem Vorsatz, Marktführer im Pharmavertrieb zu werden. Um dies zu erreichen, ist es unerlässlich, mit einem Qualitätssystem zu arbeiten, das den gesetzlich vorgeschriebenen Normen für ordnungsgemäße Herstellung und Vertrieb entspricht.
Heute verfügt Disalfarm über ein breites Sortiment an Produkten, das von verschreibungspflichtigen Arzneimitteln bis zu Arzneimitteln zur Verwendung in Krankenhäusern, tierärztlichen Arzneimitteln, Nahrungsergänzungsmitteln und sonstigen Medizinprodukten reicht.
Standort
Der Standort von Disalfarm, S.A. befindet sich in Rubí, einem Industriegebiet in der Nähe von Barcelona, an dem ein wichtiger Verkehrsknotenpunkt liegt.
Die Einrichtung liegt in der Nähe der wichtigsten Logistik- und Vertriebszentren, wodurch die Firma ihren Kunden eine flexible und schnelle Belieferung bieten kann.
Bedürfnisse von Disalfarm: Verbesserung ohne Einschränkung der Leistung
Das Wachstum, das Disalfarm in den letzten Jahren erlebt hat, führte zu einer wesentlichen Veränderung seiner Bedürfnisse in Bezug auf die Lagerung.
Im Jahre 2000 wurde ein Logistikzentrum errichtet, in dem die Lagerung mit der Kommissionierung kombiniert wurde —weniger als 20 % der Bestellungen enthielten komplette Paletten mit einer einzigen Artikelart.
In dieser ersten Phase wurden ebenfalls zwei Lagerhallen, ein Bereich zur Ladevorbereitung und Konsolidierung, die Laderampen sowie Büros und Toiletten errichtet.
Diese Einrichtungen nahmen eine Gesamtfläche von 9706 m2 ein. Alle Regalanlagen des Lagers und des Kommissionierbereichs wurden von Mecalux installiert.
2007 war das Lager an sich zu klein geworden. Die große Zahl an Bewegungen, die die Gabelstapler durchführen mussten, verursachten übermäßig hohe Kosten und erhöhten gleichzeitig die Gefahr von Arbeitsunfällen, was den Prinzipien von Disalfarm zuwiderläuft.
Angesichts dieser Situation bestand die große Herausforderung, vor die das Unternehmen Mecalux stellte, darin, dieses Logistikzentrum zu erneuern, ohne die Belieferung der Kunden zu beeinträchtigen.
Ausgangspunkt: Phasen 1 und 2
In der ersten Phase im Jahre 2000 wurde Folgendes gebaut:
- Ein Lager mit einer Lagerkapazität für 12.900 Paletten der Maße 800 x 1200 mm, das aus zehn Gängen mit 15 m hohen Regalen bestand.
- Kommissionierbereich, der aus schwerkraftgesteuerten Durchlaufregalen mit Pick-to-Light-Vorrichtungen und Behälterfördersystemen bestand, die diesen Bereich mit dem Verpackungs- und Konsolidierungsbereich verband.
- Bereich für die Kommissionierung von kompletten Kisten, die direkt von den Paletten erfolgt.
- Lager für gekühlte Produkte mit Kapazität für 290 Paletten
- Geschlossenes Lager für psychotrope Produkte.
- Neun Laderampen mit einem großen Manövrierbereich.
In der zweiten Phase kamen fünf weitere Gänge mit herkömmlichen Palettenregalanlagen mit einer Lagerkapazität für 6450 Paletten hinzu, sodass nun insgesamt 19.350 Paletten gelagert werden konnten.
Außerdem wurden drei neue Laderampen gebaut.
Der Bewegungsfluss erhöhte sich ebenfalls erheblich, sodass nun täglich 1100 Paletten bewegt wurden (500 ankommende und 600 hinausgehende).
Um eine derart große Zahl von Paletten bewegen zu können, wurden folgende Ressourcen eingesetzt:
- Sieben Frontstapler, die an den Laderampen arbeiteten, die Kommissionierbereiche versorgten und die Paletten am Eingang der Gänge abholten.
- Fünf Dreiseitenstapler, die nur innerhalb der Gänge arbeiteten.
- 24 Lagerarbeiter, die die Gabelstapler bewegten (12 pro Schicht).
In den beiden Schaubildern dieses Abschnitts ist zu sehen, wie sich die Bewegungsflüsse (Ein- und Ausgänge) im Hauptgang überkreuzen.
Warenfluss in den Phasen 1 und 2
Die Ware kam vollständig palettiert im Lager an. Der Lagerarbeiter las den Barcode jeder Palette mit einem EDV-Terminal ab und die Lagerverwaltungssoftware (LVS) zeigte ihm den zugewiesenen Gang an. Nach der Bestimmung der Lagerposition wurden die Paletten mit Frontstaplern zu den Konsolen gebracht, die sich am Anfang des Lagergangs befanden, wo sie von den Dreiseitenstaplern übernommen und in die vom Lagerverwaltungssystem festgelegte Lagerposition gebracht wurden.
Bei Auslagerungen wurde der gleiche Vorgang in umgekehrter Reihenfolge durchgeführt, mit dem Unterschied, dass die meisten Paletten für den Kommissionierbereich bestimmt waren.
Phase 3: Abschaffung des internen Transports kompletter Paletten
Durch das Wachstum der Firma war es nicht erforderlich, mehr Lagerpositionen zu schaffen, es war jedoch nötig, mehr Paletten zu bewegen. Um dies zu erreichen, wurde die Möglichkeit erwogen, die Anzahl der Gabelstapler und der Arbeiter zu erhöhen, dies war jedoch mit einem erhöhten Risiko verbunden.
Die Einrichtung besaß fünfzehn Lagergänge und es gab schon fünf Dreiseitenstapler. Obwohl man noch fünf weitere angeschafft haben könnte, wurde diese Möglichkeit verworfen, da es sich um halbautomatische, langsame Geräte handelt und die Zahl der möglichen Zyklen nicht ausreichte, die Anforderungen von Disalfarm zu erfüllen.
Zu diesem Zeitpunkt erwog Mecalux zwei mögliche Optionen in Bezug auf den Einsatz automatischer Rollen- und Kettenförderer, um jegliche Bewegungen der Gegengewichtsstapler innerhalb des Lagers selbst überflüssig zu machen.
Erste Option für Phase 3: verworfen
Der Vorschlag bestand aus einem Regaleingang, der aus folgenden Elementen bestand:
- Zwei Hauptstränge, die quer zu den Regalzeilen verlaufen.
- Zwei Kämme (einer für Eingänge und einer für Ausgänge) in jedem Lagergang.
- Eingangsprüfstelle für Paletten im Bereich der Laderampen, an der ungeeignete Paletten zurückgewiesen werden.
- Direkter Ausgang zum Versandbereich.
- Zwei Ausgänge zum Kommissionierbereich.
Dies war die konsequenteste Option, wenn man die Nähe zu den Laderampen betrachtet, und sie war ebenfalls geeignet, um die Kommissionierstellen zu versorgen. Für die Lagerarbeiten würden die Dreiseitenstapler genutzt und in Zukunft würde man entweder die Zahl der Stapler erhöhen oder nach einer automatischen Lösung suchen. Bei dieser Option würde der hintere Bereich für den Gangwechsel der Dreiseitenstapler genutzt, genauso wie es schon in der ersten Phase vorgesehen war.
Obwohl dieser Vorschlag der einfachste und logischste war, wenn von Anfang an alles nach diesem Prinzip durchgeführt worden wäre, wurde er verworfen, weil es zu seiner Realisierung notwendig gewesen wäre, den Lagerbetrieb zu unterbrechen.
Zweite Option für Phase 3: die Lösung
Man entschied sich dafür, den Hauptbereich des Regaleingangs an die Rückseite des Lagers zu verlegen. Auf diese Weise würde der Hauptgang wie bisher für die Richtungswechsel der Dreiseitenstapler und die Bewegungen der Frontstapler genutzt.
Diese Lösung war komplizierter und teuerer, da ein Förderkreislauf im unteren Teil einer der Regalanlagen installiert werden musste, der die gesamte von den Laderampen kommende Ware transportiert. Das Gleiche galt für die Ausgänge, dies war jedoch die einzige Lösung, deren Realisierung den täglichen Betriebsablauf nicht unterbrechen würde.
Die Bewegungen zwischen den Eingangskämmen und den Lagerpositionen wurden mit den Dreiseitenstaplern durchgeführt. Als der Umbau beendet war, diente der Hauptgang nur noch für den Gangwechsel der Dreiseitenstapler und die wenigen direkten Ausgänge zum Versand, die durchgeführt wurden.
Von diesem Zeitpunkt an wurde das Steuerungsprogramm Galileo von Mecalux eingesetzt, das für die Steuerung aller automatischen Bewegungen der Fördervorrichtungen zuständig ist, von der Eingangsstelle über den Kommissionierbereich bis zu den Ausgängen. Die Funkterminals wurden weiterhin benutzt, um den Fahrern der Dreiseitenstapler Anweisungen zu geben.
Phase 4:Vollautomatisierung des Lagers
Aufgrund des Erfolges, der durch die Automatisierung der Eingangs- und Ausgangsbewegungen erreicht wurde, erwog man angesichts der weiteren Wachstumsaussichten die Möglichkeit, das Lager vollständig zu automatisieren.
Die vollständige Automatisierung brachte einen neuen Nachteil mit sich:Mit den auf dem Markt angebotenen automatischen Geräten (Regalbediengeräte) war es nicht möglich, die Paletten auf dem Boden abzusetzen. Um dieses Problem zu lösen, bestand die einzige Möglichkeit darin, die erste Ebene ca.60 bis 70 cm über dem Boden zu installieren und eine Führungsschiene im oberen Teil der Gänge anzubringen. Diese Lösung hätte den Verlust einer kompletten Lagerebene bedeutet, wodurch man 1290 Paletten weniger hätte lagern könnten.
Da es die Bedürfnisse von Disalfarm nicht zuließen, Lagerkapazität einzubüßen, musste ein anderer Weg zur Automatisierung gefunden oder ein ganz neues Logistikzentrum gebaut werden. Zu diesem Zeitpunkt brachte Mecalux das dreiseitige Regalbediengerät auf den Markt, ein natürlicher Ersatz für die Dreiseitenstapler, der sich perfekt an die Bedürfnisse des Logistikzentrums von Disalfarm anpasste.
Es besitzt folgende Eigenschaften:
- Paletten können in einer Höhe von nur 10 cm über dem Boden abgesetzt werden.
- Es verfügt über dreiseitige Gabeln anstelle der üblichen seitlichen Teleskopgabeln.
- Es sind keine Führungsschienen im oberen Teil der Gänge notwendig, sondern nur zwei Führungsschienen am Boden.
- Es erreicht eine maximale Höhe von 15 m.
- Es kann eine Umsetzbrücke (für den Gangwechsel) installiert werden.
- Es funktioniert ebenfalls mit dem Steuerungsprogramm Galileo.
- Es wird mindestens die gleiche Kapazität wie mit Dreiseitenstaplern erreicht.
Die in Phase 4 durchgeführten Änderungen
Die durchgeführten Änderungen waren minimal und einfach zu realisieren. Sie bestanden vor allem darin:
- Die beiden Führungsschienen am Boden zu installieren.
- Die Abstände zwischen den Ebenen leicht zu verändern.
- Die auf den Fördervorrichtungen des Regaleingangs installierte Prüfstelle zu verlängern.
- Sicherheitsabsperrungen anzubringen, um die gesamte Einrichtung an die Vorschriften zur Automatisierung von Lagern anzupassen, insbesondere in Bezug auf die Sicherheit in den Gängen, in denen sich Regalbediengeräte bewegen.
Der Zugang zu den Gängen im Zusammenhang mit Instandhaltungsarbeiten im Lager erfolgt von der dem Regaleingang gegenüberliegenden Seite aus, d. h., von dort, wo sich der Hauptgang der Installation befand, als noch mit Dreiseitenstaplern gearbeitet wurde.
Für die wenigen Vorgänge, bei denen komplette Paletten das Lager verlassen, wurde ein dynamischer Kanal pro Gang auf den Konsolen eingerichtet, die sich am ursprünglichen Regaleingang befanden. Dieser kann mit Gegengewichtsstaplern angefahren werden, ohne dass diese in den automatisierten Bereich gelangen müssen.
Kommunikation mit der Software
Von Anfang an verfügte Disalfarm über ein leistungsstarkes Lagerverwaltungssystem (LVS), das an seine betrieblichen Anforderungen angepasst war. Die weitere Nutzung dieses Systems als Grundlage zur Verwaltung des gesamten Systems war eine verpflichtende Bedingung. Aus diesem Grund brauchte nur das standardmäßige Steuerungsprogramm von Mecalux eingesetzt zu werden, Galileo Control System, um alle Bewegungen innerhalb des Lagers durchzuführen.
Außerdem wurde eine Kommunikationsschnittstelle für die korrekte Kommunikation der beiden Systeme entwickelt, sowie eine mittlere Schicht für die Verwaltung, die unstimmige Befehle bei der Reservierung und Belegung der Lagerpositionen verhindern soll.
Vorteile für Disalfarm
- Hohe Lagerkapazität auf reduziertem Raum: Das Lager von Disalfarm kann 19.350 Paletten der Maße 800 x 1200 mm aufnehmen.
- Verbesserung ohne Einschränkung der Leistung: Mecalux hat das Logistikzentrum von Disalfarm optimiert, ohne dass die Belieferung jemals unterbrochen werden musste, und die Firma konnte in der gleichen Einrichtung verbleiben.
- Hohe Produktivität: Die Automatisierung der verschiedenen Lagerprozesse hat den Bewegungsfluss erhöht, was den Bedürfnissen des Unternehmens entgegenkommt.
- Vollständige Kontrolle: Die Kommunikationsschnittstelle zwischen dem Lagerverwaltungssystem von Disalfarm und dem standardmäßigen Steuerungsprogramm von Mecalux ermöglicht die Lenkung aller Prozesse und Vorgänge innerhalb des Lagers.
Lager von Disalfarm | |
---|---|
Lagerkapazität: | 19.350 Paletten |
Abmessungen der Palette: | 800 x 1200 mm |
Höchstgewicht der Palette: | 800 kg |
Regalhöhe: | 13 m |
Regallänge: | 60 m |
Anzahl Regalbediengeräte: | 15 |
Art der Regalbediengeräte: | automatisch, dreiseitig |
Galerie
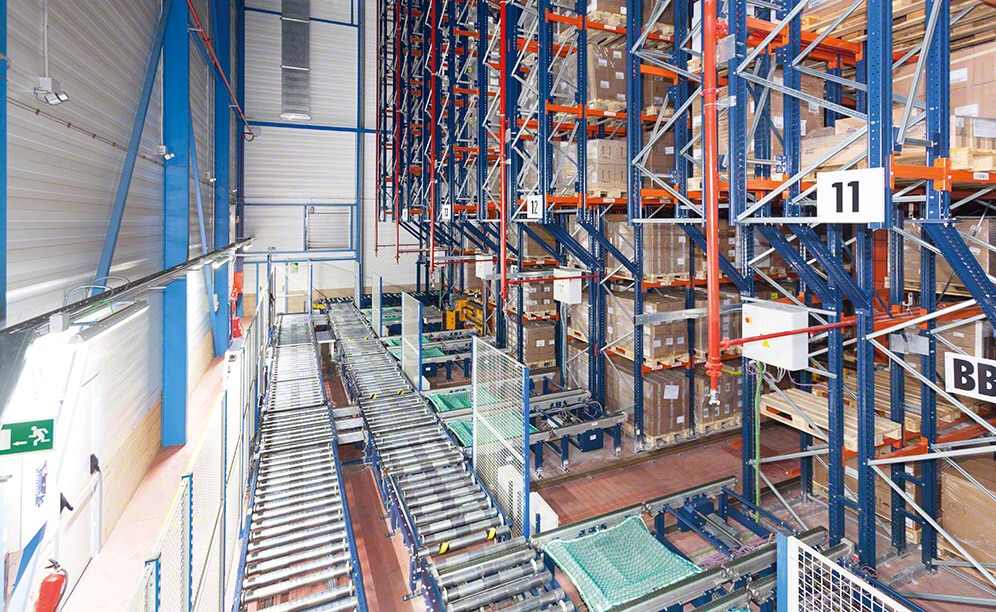
The warehouse, now fully automated and with a storage capacity for more than 19,000 pallets, has significantly improved the productivity of the company
Fragen Sie einen Experten