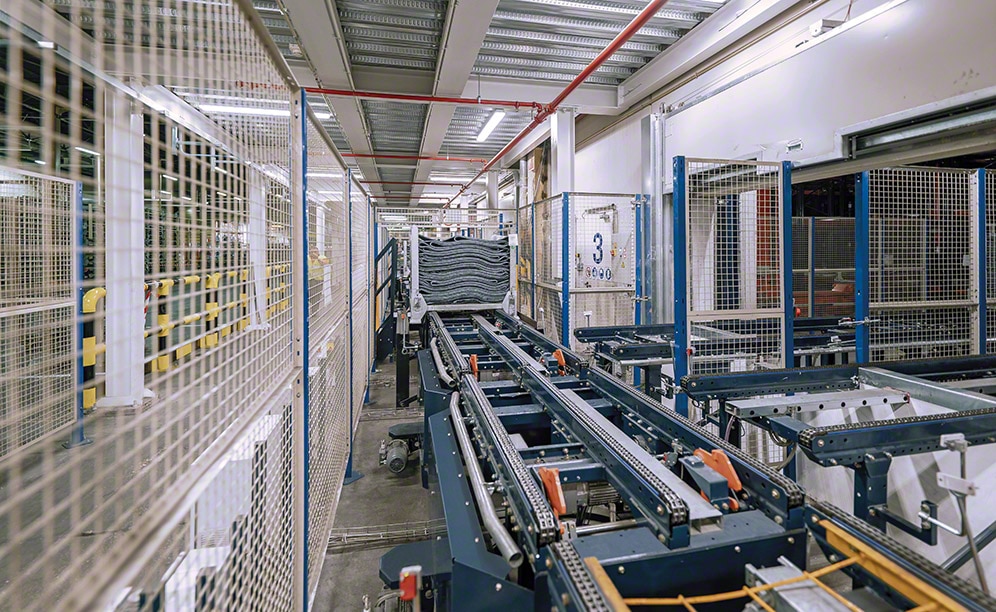
In die Produktion integriertes automatisiertes Hochregallager von Michelin
Michelin besitzt in Vitoria im Baskenland eine der größten Reifenfabriken Spaniens
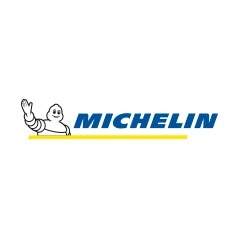
Der Reifenhersteller Michelin hat sein Produktionszentrum in Vitoria (Spanien) erweitert, um die in den letzten Jahren erzielte Produktionssteigerung bewältigen zu können. In nur acht Monaten hat Mecalux ein schlüsselfertiges, automatisiertes Hochregallager in Silobauweise errichtet, das an die Abmessungen der Metallbehälter von Michelin angepasst ist. Alle Abläufe im Lager sind vollständig automatisiert. Fördervorrichtungen, Regalbediengeräte, Palettenstapler und Shuttles transportieren die Behälter innerhalb der gesamten Anlage, gemäß den Anforderungen und Erwartungen des Unternehmens.
Ein sich im Wachstum befindliches Produktionszentrum
Im Jahre 1889 begannen die Brüder André und Edouard Michelin mit dem Projekt zur Entwicklung fortschrittlicher Transportlösungen. Auch heute noch besteht das Ziel des Unternehmens darin, zur Verbesserung der Mobilität von Gütern und Personen oder, mit anderen Worten, zur Entwicklung der Gesellschaft, beizutragen.
Michelin verfügt über mehr als 70 Produktionsstätten in 20 Ländern. Das Unternehmen investiert ständig in seine Produktionszentren und passt sie an neue Anforderungen des Marktes an. Das Unternehmen beschloss, an seinen Standort in Vitoria (Spanien) ein Lager für die bei der Reifenherstellung verwendeten Gummirohlinge zu errichten.
Dabei wurde der maximalen Nutzung der verfügbaren Fläche Priorität eingeräumt, um eine größere Lagerkapazität zu erreichen. Antonio J. García-Montalvo, Leiter dieses Projekts bei Michelin, erläutert: „Früher hatten wir ein kleineres Lager, in dem wir die Behälter stapelten, was aber nicht besonders praktisch war.“
„Das technische Team von Mecalux war quasi während des gesamten Jahres 2017 mit diesem Projekt beschäftigt, anfangs mit der Analyse unserer Anforderungen und später mit dem Bau des Lagers.“ Außerdem wurden die in der Nähe des neue Lagers vorhandenen Gebäude zur gleichen Zeit erweitert, was die Koordination von mehr als 170 Fachleuten und den gleichzeitigen Einsatz von 70-TM-Kranen erforderte.“
Das Ergebnis ist ein in die übrige Fabrik integriertes Lager, das laut dem Projektleiter „in der Lage ist, alle von den Produktionslinien erzeugten Produkte zu lagern.“ Durch diesen Neubau kann die Fläche des freigewordenen früheren Lagers für eine weitere Produktionslinie genutzt werden.
Das Lager arbeitet das ganze Jahr lang rund um die Uhr mit voller Leistung. García-Montalvo erläutert: „Wir können nun die aus den Produktionslinien kommende Ware lagern und gleichzeitig die Laderampen schneller versorgen.“
Das maßgeschneiderte Lager
Das 27 m hohe Lager ist selbsttragend, das heißt, die Regale selbst tragen ihr Eigengewicht sowie das Gewicht der Ware, der Seitenwände und des Daches. Diese Lösung hat den Vorteil, dass das Lager nur den unbedingt notwendigen Platz im Industriekomplex von Michelin einnimmt, gleichzeitig aber eine Lagerkapazität von 4590 Behältern bietet.
Es besteht aus fünf Gängen mit Regalen einfacher Tiefe auf beiden Seiten und arbeitet vollautomatisch, sodass nur minimale menschliche Eingriffe erforderlich sind. Die Fördervorrichtungen, Regalbediengeräte, Shuttles und Aufzüge transportieren die Ware zu ihren entsprechenden Lagerpositionen. Die Anlage erfüllt die Anforderungen von Michelin in Bezug auf den Warenfluss: Die Regalbediengeräte können pro Stunde bis zu 240 Behälter im kombinierten Zyklus bewegen (120 Eingänge und 120 Ausgänge).
Eine der Besonderheiten dieses Lagers besteht darin, dass keine Holz- oder Kunststoffpaletten verwendet werden, sondern Metallbehälter der Maße 1100 x 1250 x 1220 mm, um die Gummirohlinge zu lagern, aus denen die Reifen hergestellt werden. Diese Ladeeinheiten sind an ihrer Unterseite mit Füßen statt mit Kufen versehen. „Sowohl die Regale als auch die automatischen Fördermittel wurden im Hinblick auf die Abmessungen und Eigenschaften unserer Behälter konstruiert“, erklärt García-Montalvo.
Bei den Fördervorrichtungen handelt es sich um Kettenförderer, die die Ware mit einer kontrollierten Geschwindigkeit von 20 m/min transportieren. Die Regale verfügen über Halterungen, in denen die Behälter sicher platziert werden können.
Im Zentrum herrschen strenge Sicherheitsmaßnahmen, die für den bestmöglichen Zustand der Produkte sorgen. Die Temperatur des Lagers ist geregelt und wird zwischen 10 und 27 °C gehalten. Es verfügt darüber hinaus über eine Brandschutzanlage mit in den Regalen verteilten Sprinklern sowie vertikale Brandschutztüren, die im Falle ihrer Aktivierung das Lager hermetisch abschließen, um die Ausbreitung der Flammen zu verhindern.
In die Fabrik integriertes Lager
Das Lager ist in zwei Ebenen unterteilt: Auf der unteren Ebene befinden sich die Eingänge und auf der oberen die Ausgänge. „Durch diese Aufteilung werden gegenseitige Störungen zwischen den beiden Vorgängen vollständig vermieden“, betont der Projektleiter.
Wareneingang
Die Behälter kommen übereinander gestapelt aus der Produktion an. Die Lagerarbeiter setzen sie mithilfe von Gabelstaplern auf eine der beiden Eingangsstationen. Anschließend werden die Behälter von einer Stapelvorrichtung einzeln angehoben und ohne Palette auf die Kettenförderer gesetzt, die sie in das Lagerinnere transportieren.
Die Förderer sind für den Transport der Ware in den entsprechenden Gang zuständigund folgen den Anweisungen des Lagerverwaltungssystems (LVS) Easy WMS von Mecalux.
Warenausgang
Ein Shuttle mit zwei Lastaufnahmemitteln holt die für den Ausgang aus dem Lager vorgesehenen Behälter ab und transportiert sie zu einem der vier Ausgänge. Dort wurden ebenfalls Stapelvorrichtungen installiert, die die Behälter hier paarweise übereinandersetzen, damit die Lagerarbeiter sie in den LKW stellen können. García-Montalvo hebt hervor: „Auf diese Weise erreichen wir mehr Flexibilität beim Warenausgang und erhöhen die Produktivität des Versands.“
Kontrolle der Ware
Easy WMS von Mecalux wurde an die Eigenschaften des neuen Lagers von Michelin angepasst und ist zur individuellen Verwaltung seiner Produkte bereit. Um dies zu erreichen, „kommuniziert das LVS von Mecalux über eine Schnittstelle mit BSM, dem Computersystem von Michelin. Diese Schnittstelle wurde mithilfe von Tests in den Büros von Mecalux, an unserem Hauptsitz in Clermont-Ferrand und im Werk Vitoria entwickelt. All dies geschah mit dem Ziel, die korrekte Synchronisierung beider Systeme zu gewährleisten“, erläutert Garcia-Montalvo.
Michelin muss jederzeit in der Lage sein, genau zu wissen, wo sich seine Produkte befinden. Dies wird durch Easy WMS ermöglicht, da es die Rückverfolgbarkeit der Produkte jederzeit mithilfe von virtuellen Adressen steuern kann und zudem weiß, wo sich jeder Behälter befindet und ob er das Lager verlassen hat oder nicht.
Antonio J. García-Montalvo – Projektleiter des automatisierten Lagers von Michelin in Vitoria
„Wir haben uns für Mecalux als Lieferanten unseres Gummilagers in Vitoria entschieden, nachdem wir die Vorschläge von fünf weiteren Firmen geprüft hatten. Unsere Entscheidung wurde aufgrund der Erfahrung des Unternehmens im Bau von selbsttragenden Einrichtungen und der Qualität ihrer Produkte getroffen, die sich an unsere Metallbehälter anpassen können.“
Vorteile für Michelin
- Maximale Leistung: Das in die Fabrik von Michelin integrierte Lager ist rund um die Uhr in Betrieb.
- Maßgeschneiderte Lösung: Die gesamte Anlage wurde so konzipiert, dass sie die Lagerung und Handhabung der Metallbehälter der Maße 1100 x 1250 x 1220 mm von Michelin erleichtert.
- Schlüsselfertiges Lager: Mecalux hat neben den Regalen auch alle Sicherheitsvorrichtungen, das Kühlsystem und die Brandschutzvorrichtungen geliefert.
Automatische lager von Michelin | |
---|---|
Lagerkapazität: | 4590 Behälter |
Abmessungen der Behälter: | 1100 x 1250 x 1220 mm |
Höchstgewicht der Behälter: | 850 kg |
Höhe des Lagers: | 27 m |
Regallänge: | 38 m |
Galerie
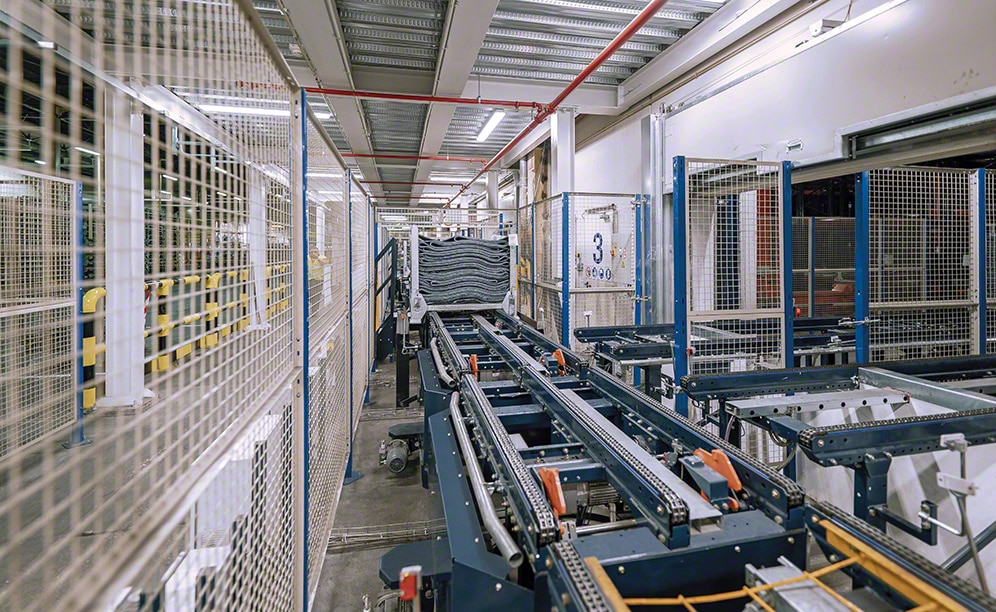
An die Abmessungen der Metallbehälter angepasste Kettenförderer
Fragen Sie einen Experten