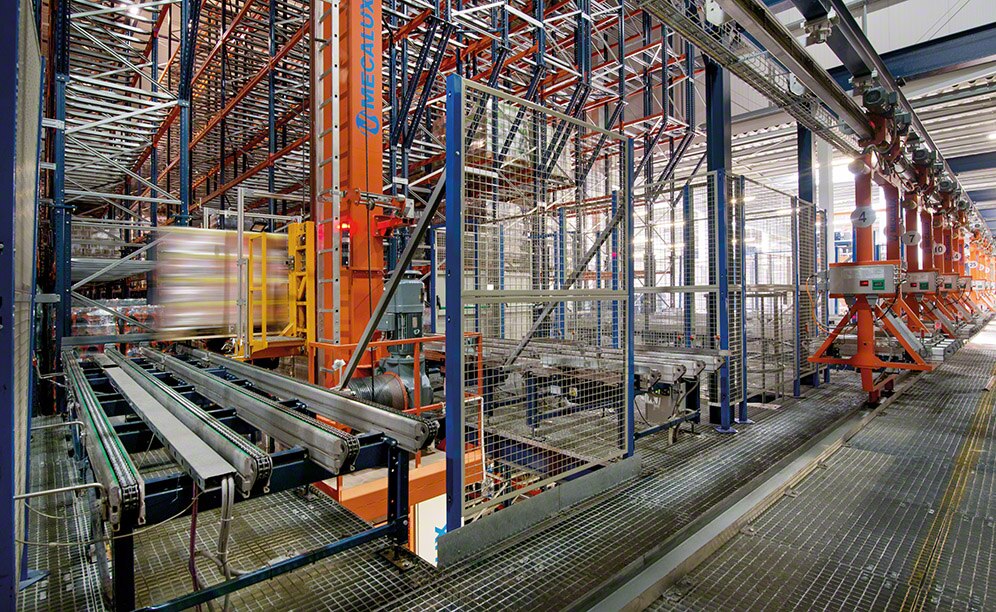
Ein großes Lager für die Säfte von Sokpol in Polen
Das Lager für Säfte von Sokpol ist über schienengeführte Fördersysteme mit dem Produktionszentrum verbunden
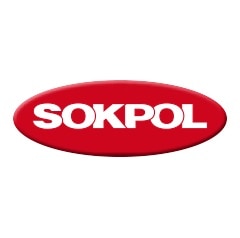
Sokpol ist einer der bekanntesten Saft-, Fruchtnektar- und Mineralwasser-hersteller Polens. Sein Produktionszentrum in Myszków ist zur Steigerung der Leistungsfähigkeit mit der neuesten Technologie ausgestattet. Dieses sich in ständiger Weiterentwicklung befindliche Projekt wurde immer wieder erweitert und an die Anforderungen von Sokpol und an neue Marktbedingungen angepasst. Derzeit besteht das Zentrum aus zwei Lagern, von denen eines mit dem halbautomatischen Pallet-Shuttle-System ausgestattet ist und für die Fertigprodukte mit der höchsten Nachfrage vorgesehen ist und das andere über eine Kapazität von mehr als 28.400 Europaletten verfügt und vollautomatisch betrieben wird.
Informationen zu Sokpol
Die Säfte, Erfrischungsgetränke und Fruchtpürees von Sokpol gehören zu den beliebtesten in Polen. Seit seiner Gründung im Jahre 1992 entwickelt und vertreibt das Unternehmen ständig neue Produkte.
In den letzten Jahren hat die Firma ihre internationale Präsenz verstärkt und vertreibt ihre Produkte in vielen Ländern Europas und in den Vereinigten Staaten.
Anforderungen von Sokpol
Sokpol besitzt ein Produktionszentrum in Myszków im Süden Polens, in dem der größte Teil seiner Produkte hergestellt wird. Die ideale Lage sorgt für einen raschen Vertrieb der Produkte in ganz Europa.
Ursprünglich verfügte das Zentrum über ein Lager neben dem Herstellungswerk, in dem die Fertigprodukte gelagert wurden. Der Platz reichte jedoch nicht aus, um den Produktionszuwachs bewältigen zu können.
In den letzten Jahren hat das Unternehmen sein Produktsortiment erweitert und seine Verkaufszahlen aufgrund der internationalen Expansion erhöht. Entschlossen, diese Herausforderungen zu überwinden und seine Zukunftsaussichten zu stärken, bat Sokpol Mecalux um Unterstützung.
Die Lösung
Unter Berücksichtigung der Bedürfnisse von Sokpol hat Mecalux ein automatisches Lager mit einer Lagerkapazität von 28.400 Europaletten (800 x 1200 mm) bzw. 56.800 Halbpaletten (400 x 600 mm) entworfen und errichtet. Es handelt sich um eine hochmoderne, funktionelle Lösung, die hohe Leistungen garantiert und alle Erwartungen übertrifft.
Der Standort von Sokpol erstreckt sich über ein weitläufiges Gelände, und das neue Lager ist ein Stück von der Produktionsstätte entfernt. Die Überbrückung dieser Entfernung hätte mit hohen Kosten für den Warentransport verbunden sein können, was unbedingt vermieden werden musste.
Aus diesem Grund hat Mecalux eine überdachte Hochbrücke errichtet, die sich 5 m über dem Boden befindet. Sie verbindet den Ausgang aus der Produktion mit dem neuen Lager und durchquert das alte Lager an einer Seitenwand. In seinem Inneren sorgt eine Elektrohängebahn für hohe Geschwindigkeit beim Transport der Ware.
Lager 1
Sokpol errichtete neben der Fabrik ein erstes Lager, das mit dem halbautomatischen Pallet-Shuttle-System ausgestattet ist.
Es dient als Puffer (Kurzzeitlager) und dort werden hauptsächlich die am häufigsten nachgefragten Fertigprodukte gelagert, bevor sie in den Versandbereich gebracht werden.
Das System eignet sich hervorragend für die dort vorhandenen Produkte mit hoher Nachfrage und mit vielen Paletten pro Artikelart. Es nutzt den gesamten verfügbaren Raum vollständig aus, um eine größere Lagerkapazität zu erreichen. Seine Funktionsweise ist sowohl einfach als auch schnell und erfordert nur minimale Bewegungen der Lagerarbeiter, was die fortlaufende Ein- und Auslagerung der Artikel ermöglicht.
Die Ware wird nach dem FIFO-Prinzip (First In First Out) verwaltet, d. h. die zuerst eingelagerte Palette wird zuerst entnommen. Es gibt zwei Arbeitsgänge: einen Gang zur Einlagerung und einen zur Entnahme, wodurch gegenseitige Störungen zwischen den beiden Abläufen vermieden werden.
Direkt vor den Laderampen verfügt das Lager über einen Bereich zur Ladevorbereitung. Die Paletten werden gruppenweise auf dem Boden gelagert, was die anschließende Beladung der Transportlastwagen beschleunigt.
Das Lager besitzt zwei Ebenen. Auf jeder Ebene werden unterschiedliche Vorgänge durchgeführt.
Untere Ebene
Hier befinden sich die Produktionsanlage und das Lager. Die Lagerarbeiter profitieren von einer direkten, hindernisfreien Verbindung, um die Ware von einem Ort zum anderen zu bringen.
Sie nehmen die Paletten mithilfe von Schubmaststaplern auf und setzen sie in dem Kanal der Regalanlage ab, der ihnen von der Lagerverwaltungssoftware (LVS) zugewiesen wurde. Anschließend transportiert der motorisierte Wagen die Ladung selbstständig bis zur ersten freien Lagerposition.
Direkt neben dem Ausgang aus der Produktion wurde außerdem ein Förderkreislauf installiert, auf den die Paletten gesetzt werden, die direkt für das Lager 2 bestimmt sind. Die Fördervorrichtungen transportieren die Paletten zu zwei Lastenaufzügen, die die Lasten auf die obere Ebene heben, auf der sich der Kreislauf mit den Elektrohängebahnen befindet.
Neben den Laderampen befindet sich ein dritter Lastenaufzug, der die Produkte auf die obere Ebene befördert. Dieser Eingang ist für die Produkte bestimmt, die aus anderen Produktionsstätten kommen und im Lager 2 gelagert werden sollen.
Vor der Ankunft am Lastenaufzug durchlaufen die Paletten eine Prüfstelle. Dort wird überprüft, ob sie sich in gutem Zustand befinden und ihr Gewicht und ihre Abmessungen den im automatischen Lager vorgeschriebenen Qualitätsansprüchen entsprechen.
Sowohl die Fördervorrichtungen als auch die Lastenaufzüge sind durch Gitterwände, Lichtschranken und gesicherte Zugangstüren geschützt, die den Zutritt von nicht autorisierten Personen in ihrem Aktionsradius verhindern.
Obere Ebene
Die Elektrohängebahnen verlaufen an einer der Seitenwände des Lagers bis zur Hochbrücke. Auf der anderen Seite der Brücke befindet sich das Lager 2.
Durch die Installation des Elektrohängebahnkreislaufs auf der oberen Ebene wird die Fläche des Lagers maximal genutzt, und gegenseitige Störungen der übrigen Vorgänge werden vermieden.
Hochbrücke und Elektrohängebahn
Die Hochbrücke ist die beste Lösung, um die drei Gebäude miteinander zu verbinden. Sie verbindet ebenfalls die Lager 1 und 2, die durch eine Straße getrennt sind.
In ihrem Inneren verläuft der Kreislauf der Elektrohängebahn. Hierbei handelt es sich um ein flexibles und schnelles Transportsystem, dass eine Geschwindigkeit von bis zu 100 m/min erreicht und einen ständigen Warenfluss gewährleistet.
Der Kreislauf besteht aus Schienen, die an der Decke aufgehängt sind und an denen sich autonome Wagen bewegen, die die Paletten transportieren. Abhängig von den Bedürfnissen und dem Wachstum der Firma kann die Anzahl der Wagen erhöht werden.
In diesem Lager wird hauptsächlich mit Europaletten und Halbpaletten gearbeitet. Um sie transportieren zu können, verfügen sowohl die Wagen der Elektrohängebahnen als auch die Fördervorrichtungen über vier Kettenstränge.
Die Hauptvorteile der Elektroführungen bestehen in ihrer hohen Effizienz, großen Vielseitigkeit und der Fehlerminimierung.
Der Kreislauf durchläuft den gesamten Eingangsbereich des Lagers 2. Dort werden die Paletten auf die Ein- und Ausgangsförderer der einzelnen Gänge gesetzt bzw. von diesen entnommen. Am Ende des Kreislaufs wurde ein Wartungsbereich eingerichtet, in den die Wagen gebracht werden, bei denen bestimmte Maßnahmen erforderlich sind, und wo die Wagen in Wartestellung verbleiben.
Bei der sorgfältigen Konzeption dieses Kreislaufs wurden die Warenflüsse und die Anzahl der Paletten, die zwischen den beiden Lagern transportiert werden müssen, genau betrachtet. Aus diesem Grund wurden zwei Abkürzungen eingerichtet, die vermeiden, dass die Wagen den gesamten Kreislauf durchlaufen müssen.
Lager 2
Das 15,5 m hohe automatische Lager besteht aus neun Gängen mit Regalanlagen doppelter Tiefe auf beiden Seiten.
Die Artikelarten werden unter Berücksichtigung ihrer Rotation (A, B oder C) in den entsprechenden Lagerpositionen gelagert. Die stärker nachgefragten Produkte befinden sich im vorderen Teil des Lagers und die geringer nachgefragten im hinteren Teil. Diese Anordnung optimiert die Bewegungen der Fördermittel und erhöht die Zykluszahl.
In jedem Gang ist ein Einmast-Regalbediengerät vorhanden, das sich mit einer Seitwärtsgeschwindigkeit von 160 m/Min. und einer Hubgeschwindigkeit von 38 m/Min. bewegt.
Die Regalbediengeräte holen die Paletten von den Eingangsförderern ab und setzen sie an der Lagerposition ab, die ihnen die Lagerverwaltungssoftware Easy WMS von Mecalux zugewiesen hat. Später wird die gleiche Bewegung in umgekehrter Richtung zur Entnahme der Ware durchgeführt.
Der Eingangsbereich des Lagers besteht aus zwei Ebenen. Auf der oberen Ebene, auf der sich die Elektrohängebahnen bewegen, finden die Ein- und Ausgänge des Lagers statt. Auf der unteren Ebene wurden die Schalt- und Steuerschränke sowie die Zugangstüren zu den Wartungsbereichen installiert.
Die Schalttafeln senden und empfangen Signale und versorgen die Geräte im Lager, z. B. Fördervorrichtungen, Regalbediengeräte, Elektrohängebahnen oder Lastenaufzüge, mit Strom.
An einer Seite des Lagers wurde ein niedrigerer Anbau mit zwei Ebenen errichtet, auf denen jeweils verschiedene Vorgänge stattfinden.
Obere Ebene
Hier befindet sich eine freie Fläche, auf der sich die Kommissionierstationen befinden.
Die Elektrohängebahnen beliefern diesen Lagerbereich mit den notwendigen Paletten für die Auftragszusammenstellung. Die Eingangsförderer verfügen über einen Hubtisch, der die Arbeit mit Palettenhubwagen ermöglicht.
Untere Ebene
Sie ist für den Ausgang zum Versand und zur Ladevorbereitung bestimmt. Zwei Lastenaufzüge bringen die Ware auf die untere Ebene. Zwei Verfahrwagen bedienen diesen Bereich, indem sie die Ware im entsprechenden dynamischen Kanal absetzen.
Die Verfahrwagen verbinden zwei Punkte in gerader Linie und können sich in beiden Richtungen bewegen. Sie bewegen sich auf Schienen und verfügen über vier Kettenförderstränge für den Transport der Paletten. Es wurden 40 dynamische Kanäle zur Ladevorbereitung eingerichtet.
Es wurden 40 dynamische Kanäle zur Ladevorbereitung eingerichtet. Diese haben eine leichte Neigung, sodass sich die Paletten mithilfe der Schwerkraft vom oberen bis zum unteren Teil (der den Laderampen gegenüberliegt) bewegen. Im unteren Teil sind die Rollen geteilt, damit die Gabelzinken der Stapler ausreichend zur Entnahme der Paletten haben.
Easy WMS von Mecalux
Angesichts der Größe dieses Produktionszentrums ist ein äußerst effizientes Informatiksystem unerlässlich. Die von Mecalux entwickelte Lagerverwaltungssoftware Easy WMS steuert und verwaltet alle stattfindenden Prozesse wie beispielsweise den Eingang der Ware aus der Produktion und von außerhalb, die Zuweisung der Lagerpositionen, die Bestandskontrolle, die Entnahme, den Versand usw.
Easy WMS von Mecalux verfügt über konfigurierte Regeln und Algorithmen zur Lagerung der Ware in den entsprechenden Lagerpositionen, die die Eigenschaften der Produkte, die Verbrauchskriterien und ihren Umschlag berücksichtigen.
Die LVS gibt an, welche Artikel aus dem Lager entnommen werden sollen. Diese werden automatisch in den Bereich der Ladevorbereitung gebracht, wo sie verbleiben, bis der Lastwagen an der Laderampe andockt und sie verladen werden.
Um den korrekten Betrieb dieses Zentrums zu gewährleisten, steht Easy WMS von Mecalux in ständiger Verbindung mit dem Unternehmensverwaltungssystem ERP von Sokpol sowie mit dem Steuerungsmodul Galileo.
Galileo ist die Steuerungssoftware von Mecalux, die in beiden Lagern Befehle an die Vorrichtungen (Fördervorrichtungen, Regalbediengeräte, Elektrohängebahnen und Lastenaufzüge) erteilt und mögliche Zwischenfälle registriert. Sie stellt sämtliche Informationen über alle Vorrichtungen in Echtzeit bereit und ist in der Lage, die elektromechanischen Funktionen der gesamten automatischen Anlage über ein Steuerungssystem mit dem Namen SCADA zu simulieren.
Vorteile für Sokpol
- Effizientes Fördersystem: Der Kreislauf der Elektrohängebahn, der die beiden Lager mit der Produktion verbindet, gewährleistet die erforderliche Anzahl an Palettenbewegungen bei Sokpol.
- Sichere Installation: Die elektromechanischen Elemente sind geschützt und der Zutritt von unbefugten Personen wird verhindert, um Zwischenfälle zu vermeiden.
- Optimale Abläufe: Die Anordnung der Ware im Lager abhängig von ihren Eigenschaften und ihrem Umschlag erhöht die Produktivität in beiden Lagern.
Automatischen Lager von Sokpol in Polen | |
---|---|
Installierte Vorrichtungen: | Kreislauf mit Elektrohängebahnen |
Installierte Vorrichtungen: | Lastenaufzüge |
Installierte Vorrichtungen: | Regalbediengeräte |
Installierte Vorrichtungen: | Verfahrwagen |
Installierte Vorrichtungen: | Fördervorrichtungen |
Installierte Vorrichtungen: | Dynamische Kanäle zur Ladevorbereitung |
Galerie
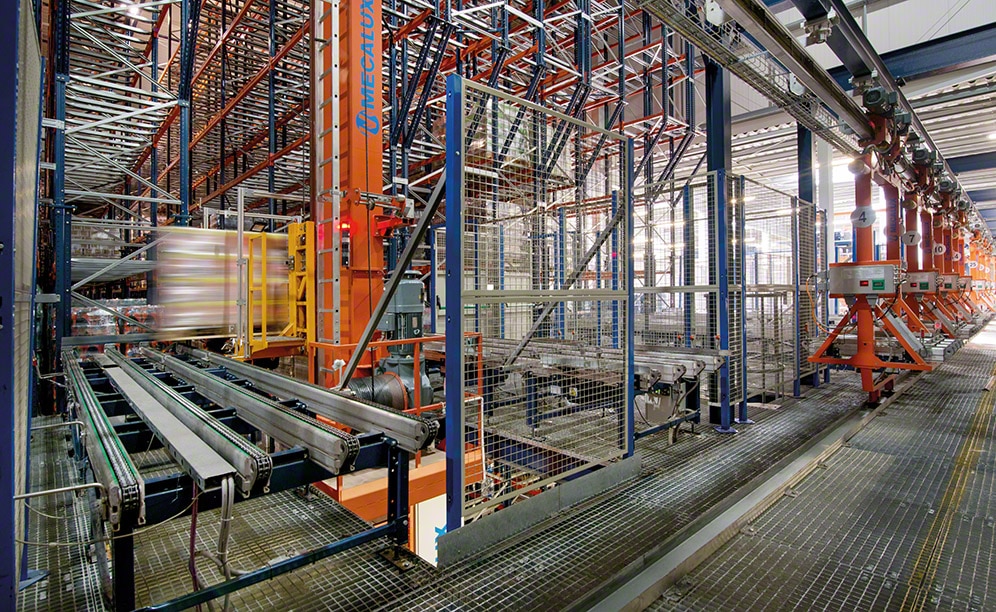
Das automatisierte Lager von Sokpol mit einer Lagerkapazität von 28.400 Paletten
Fragen Sie einen Experten