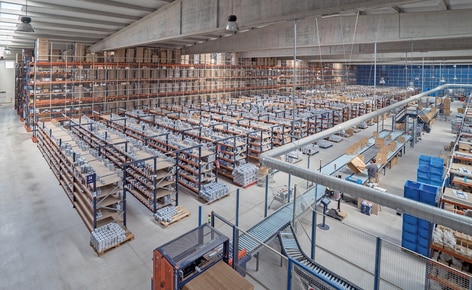
Innovation und Flexibilität bei der Kommissionierung von Industrie-, Hardware- und DIY- Kundenaufträgen
Das neue Cofan Logistikzentrum ist in verschiedene Bereiche unterteilt und ist speziell auf eine optimale Kommissionierung ausgerichtet
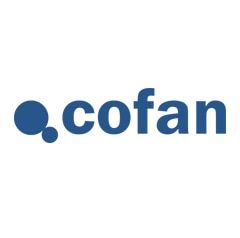
Cofan hat ein modernes Logistikzentrum gebaut, das in verschiedene Bereiche aufgeteilt ist, in denen die Ware je nach Eigenschaften und Nachfrage angeordnet wird. Mecalux hat alle Lagersysteme der Einrichtung (einschließlich eines automatischen Miniload-Lagers) und einen vollständigen Förderkreislauf mit Stationen zur Auftragszusammenstellung, Kartonfaltmaschinen, Verschließmaschinen, Waagen und Klassifizierungsrampen geliefert. Dank dieser Lösung kann die Kommissionierung schnell und effizient erfolgen.
Wer ist Cofan?
Cofan ist eine Firma mit über 15-jähriger Erfahrung in der Entwicklung und dem elektronischen Handel von Eisenwaren, Industrie- und Heimwerkerbedarf. Sie bietet drei verschiedenen Marken an (Cofan, Bricofan und Cofan Home), die in mehr als 12 Ländern verkauft werden.
Das Unternehmen ist bestrebt, sein Wachstumstempo durch Innovation und die Einführung der Technologie in allen seinen Produktionsprozessen zu beschleunigen. Derzeit ist Cofan eine Referenz im Industrie- und Automobilsektor und eine Vertrauensmarke im Onlinehandel.
Die Bedürfnisse von Cofan
Durch das starke Wachstum der letzten Jahre sah sich Cofan gezwungen, ein neues Logistikzentrum zu bauen, das auf eine kurz- und mittelfristige Erweiterung hin ausgelegt ist. Die Firma musste die höchstmögliche Lagerkapazität erreichen und die Produkte nach Artikelarten klassifizieren, um die Zusammenstellung und Konsolidierung der Aufträge zu beschleunigen. Ein weiteres Ziel war es, die Betriebskosten zu minimieren und den E-Commerce-Kunden effiziente Leistungen zu bieten.
Das Unternehmen bat Mecalux um seine Mitarbeit bei der Suche nach einer geeigneten Lösung, die all diese Anforderungen erfüllt, die Zahl der täglich versandten Aufträge erhöht und außerdem die Lieferzeiten der Aufträge verkürzt. Wegen der unterschiedlichen Größen, Gewichte und Klassifizierung der Produkte hinsichtlich ihrer ABC-Rotation stellte das Projekt eine große Herausforderung dar, daher war eine äußerst gründliche Analyse jedes einzelnen Punkts notwendig.
Das Logistikzentrum
Das Ergebnis ist dieses neue Logistikzentrum in Campo de Criptana, ca.150 km von Madrid entfernt, in der Nähe der wichtigsten Logistikplattformen der iberischen Halbinsel. Es befindet sich an einem wichtigen Kommunikations-Knotenpunkt, der die optimale Verteilung der Produkte in ganz Spanien erleichtert.
Das 25.000 m2 große Lager ist gemäß den Anforderungen der Firma in verschiedene Bereiche aufgeteilt, wodurch jede Produktfamilie nach ihrer Nachfrage und ihren Abmessungen klassifiziert werden kann. Die wichtigste Tätigkeit ist die Kommissionierung, mit vielen Aufträgen und wenigen Vorbereitungslinien in jedem Auftrag.
Das Lager besteht aus den folgenden Teilen und Sektoren:
- Lager für manuelle Kommissionierung von Produkten mit hohem Umsatz
- Reservelager
- Reserve- und Kommissionierungslager für sperrige Produkte
- Automatisches Miniload-Lager
- Lager für empfindliche Artikel
- Automatische Kartonfaltmaschinen
- Förderkreislauf und Vorbereitungstische
- Konsolidierungs- und Kontrollbereich
- Bereich für die Klassifizierung der Aufträge
Kommissionierung: die Hauptfunktion des Logistikzentrums
Aufgrund der Eigenschaften und der Art der Aufträge ist der zentrale Bereich des Lagers für die Produkte mit hohem Umsatz bestimmt. Dieser Bereich musste leicht zugänglich und gleichzeitig flexibel sein, wobei sich die Zahl der Kommissionierer je nach Nachfrage und Tageszeit ändert.
Um dieses Ziel zu erreichen, wurden Regalzeilen mit geringer Höhe für eine beschränkte Anzahl von Artikelarten installiert. Die Reservepaletten für diese Produkte befinden sich in den Regalanlagen auf beiden Seiten des Kommissionierbereichs und die Auffüllung wird in den arbeitsschwachen Zeiten vorgenommen, d. h., wenn weniger Arbeit bei der Auftragszusammenstellung anfällt.
In der Mitte dieses Bereichs verläuft der Kreislauf mit den Förderern, die sich mit einer Geschwindigkeit von 45 m/min bewegen. An diesen schließen sich auf beiden Seiten sechs Rollentische mit hohem Fassungsvermögen zur Auftragszusammenstellung an.
Kartonfaltmaschine
Der ganze Vorgang beginnt mit dem Falten der Kartons. Diese Arbeit wird von vier automatischen Kartonfaltmaschinen erledigt (von denen jede für eine andere Größe zuständig ist), die sich am Anfang des Transportkreislaufs befinden.
Die Lagerverwaltungssoftware (LVS) teilt den Kartonfaltmaschinen die Menge und die Größe der Kartons für die Bestellungen mit, wobei die Zusammenstellung jedes Schubs zur Auftragszusammenstellung berücksichtigt wird. Die Kartons, die durch ein ihnen zugewiesenes, aufgeklebtes Etikett gekennzeichnet werden, laufen hintereinander durch den Transportkreislauf bis zum ersten Kommissioniertisch, an dem sich die erforderlichen Produkte für den entsprechenden Auftrag befinden. Der Kommissionierer liest das Etikett der Schachtel mit einem Funkterminal ab, um zu erfahren, welches Material er hineinlegen muss.
Lager für manuelle Kommissionierung
Zu jedem der sechs Vorbereitungstische gehört ein Bereich mit einer bestimmten Anzahl von Regalen. Die Kommissionierer fahren mit Wagen durch die Regalgänge, um die Artikelarten einzusammeln, die ihnen das LVS über das Funkterminal mitgeteilt hat. Nach Abschluss dieser Phase wird die Bestellung wieder auf das Band gesetzt und zur nächsten Station befördert, an der sich die für sie erforderlichen Produkte befinden.Wenn die Bestellung abgeschlossen ist, leitet die Fördervorrichtung sie automatisch in den Konsolidierungs- und Klassifizierungsbereich.
Automatisches Miniload-Lager
Hinter diesem Bereich für Produkte mit hohem Umschlag befinden sich die Vorbereitungstische, neben dem automatischen Miniload-Lager für Behälter. In diesem Bereich werden die kleineren Produkte mit geringerem Umsatz (vor allem Typ B und C) gelagert.
Der Umsatz dieser Produkte entspricht dem Pareto-Prinzip oder der 80/20-Regel, d. h.80 % der Artikelarten machen nur 20 % der Lagerbewegungen aus.
Lager für empfindliche Artikel
Anschließend verläuft der Kreislauf durch die herkömmlichen Palettenregalanlagen, in denen sperrige und wenig nachgefragte Produkte lagern. Direkt daneben bildet das Lager für empfindliche Artikel die letzte Phase des Kreislaufs.
Fertigstellung
Die fertigen Aufträge werden in den Konsolidierungsbereich gebracht, wo die Verpackung, die Etikettierung und die Erstellung der erforderlichen Versanddokumente erfolgen.
Angesichts der Bedürfnisse des Unternehmens und der großen Menge an Aufträgen, die täglich bearbeitet werden, wurden in diesem Bereich zwei Gruppen mit vollkommen automatisch arbeitenden Waagen, Verschließ- und Etikettiermaschinen aufgestellt. Aus dem Konsolidierungsbereich werden die fertigen Bestellungen zu den fünf Klassifizierungsrampen geleitet, die sich vor den Laderampen befinden. Dort werden sie vor dem Versand nach Routen und Transportunternehmen gruppiert.
Miniload-Lager
Im automatischen Lager für Behälter befinden sich kleinere Produkte und solche mit geringem Umschlag. In diesem Bereich des Logistikzentrums, in dem die Auftragszusammenstellung nach dem Prinzip „Ware zur Person“ erfolgt, wurden „Put-to-Light“-Vorrichtungen installiert, die den Ablauf beschleunigen und die Fehler der manuellen Handhabung minimieren.
Es gibt zwei Kommissionierstellen, an denen die Kommissionierer die aus dem Lager kommenden Kartons empfangen. Hinter ihnen befindet sich ein Tisch für die Auftragszusammenstellung, an dem ein Schub von elf Aufträgen gleichzeitig bearbeitet werden kann. Die Regalbediengeräte setzen die Behälter (Eurokisten) mit der Ware auf die Fördervorrichtungen, mit denen sie automatisch zu den Kommissionierstellen gebracht werden. Die Kommissionierer entnehmen die Produkte, die ihnen das System auf einem Bildschirm anzeigt, und legen sie in den entsprechenden Karton auf dem Tisch zur Auftragszusammenstellung.
Die „Put-to-Light“-Anzeigegeräte zeigen den Kommissionierern optisch mithilfe von drei Farben an, wo sie jeden Artikel ablegen müssen. Der Kommissionierer drückt auf die Anzeige, um zu bestätigen, dass er die Tätigkeit durchgeführt hat.
Das automatische Lager besteht aus drei Gängen mit Regalanlagen einfacher Tiefe auf beiden Seiten. Die Regalanlage verfügen über 19 Ebenen mit einer Höhe von 8,6 m.
In jedem Gang bewegt sich ein Einmast-Miniload-Regalbediengerät, das für die Ein- und Auslagerung der Ware verantwortlich ist. Diese Geräte arbeiten mit einer Seitwärtsgeschwindigkeit von 180 m/Min. und einer Hubgeschwindigkeit von 100 m/Min.
Das Regalbediengerät besitzt ein System zum Ausfahren der Gabeln, die in die Unterseite der Behälter geschoben werden und sie herausnehmen oder in die Lagerpositionen auf beiden Seiten des Ganges setzen.
Im hinteren Teil der Gänge wurde ein Wartungsbereich mit gesicherten Zugangstüren eingerichtet, die für die Sicherheit der Arbeiter sorgen. Die Regalbediengeräte fahren dorthin, wenn ein Eingriff oder eine Reparatur erforderlich ist.
Easy WMS von Mecalux
Das automatische Kommissionierungslager wird durch die Lagerverwaltungssoftware Easy WMS von Mecalux gesteuert, die dessen korrekte Funktion kontrolliert und koordiniert.
Dieses leistungsstarke System führt verschiedene Vorgänge aus, unter anderem die Zuweisung der Lagerplätze und die Einlagerung der Behälter abhängig vom Umschlag, die Entnahme der Ware und die Auftragszusammenstellung.
Easy WMS von Mecalux kommuniziert ständig in beiden Richtungen mit dem allgemeinen LVS des Lagers und dem ERP von Cofan, wobei Daten und Informationen ausgetauscht werden, um die höchste Produktivität und Rentabilität der Kommissionierung zu erreichen.
Verschiedene Lagersysteme
Die Anordnung der verschiedenen Lagersysteme im Logistikzentrum passt sich an die große Vielfalt der verfügbaren Produkte an und berücksichtigt ihre Nachfrage und Rotation, wodurch die Auftragszusammenstellung beschleunigt wird.
Im mittleren Bereich, in dem kleinere Produkte mit hohem Umschlag gelagert werden, wurden 59 Kommissionierregale installiert, die 2,5 m hoch und 2,7 m lang sind.Sie bestehen aus drei bzw. fünf Ebenen mit Regalbrettern.
Die Gänge sind ausreichend breit, sodass sich die Arbeiter dort schnell und ohne gegenseitige Behinderung bewegen können. Ein mit dem LVS des Lagers verbundenes Funkterminal ermöglicht die Identifizierung und Klassifizierung der Produkte. Die Aufträge werden schubweise zusammengestellt, d. h., mehrere Aufträge gleichzeitig, um die zurückgelegte Strecke zwischen den verschiedenen Lagerorten innerhalb der Installation zu optimieren.
In der Nähe des Bereichs, der für die manuelle Kommissionierung von Produkten mit großem Umschlag vorgesehen ist, wurden 7,5 m hohe herkömmliche Palettenregalanlagen installiert. Dort werden sperrige Güter und die Reserve für die Produkte mit hohem Umschlag auf Paletten gelagert. Daneben wird auf den unteren Ebenen direkt kommissioniert.
Die Kommissionierer setzen niedrige Kommissionierstapler ein, da diese so angepasst sind, dass die Kommissionierung in einer ergonomischen Position durchgeführt wird, und bis zu zwei Paletten gleichzeitig transportiert werden können.
Es wurde ein unterer Durchgang geschaffen, der quer unter den Regalzeilen durch verläuft. Er dient einerseits als Notausgang und erleichtert andererseits den Warenfluss. Die Module, die sich über dem Sicherheitsgang befinden, sind mit Gittern versehen, um das Herabfallen von Material zu verhindern.
Vorteile für Cofan
- Hohe Lagerkapazität: Im neuen Logistikzentrum von Cofan mit einer Fläche von 25.000 m2 sind verschiedene Lagersysteme zu finden, die sich an die breite Vielfalt von Produkten mit ganz verschiedenen Abmessungen anpassen.
- Effizientes System für die Zusammenstellung von Aufträgen: Durch die Anordnung der Ware unter Berücksichtigung ihrer Eigenschaften und ihres Umschlags können die Bewegungen der Kommissionierer optimiert und die maximale Rentabilität bei der Auftragszusammenstellung erzielt werden.
- Effiziente Verwaltung: Die Kombination der verschiedenen in der Einrichtung vorhandenen Softwaresysteme, sowohl für die Verwaltung als auch zur Steuerung, sowie das ERP von Cofan sorgen für die maximale Ausnutzung aller Ressourcen.
Automatisches Miniload-Lager con Cofan, Spanien | |
---|---|
Lagerkapazität: | 14.334 Behälter |
Maximalgewicht pro Behälter: | 30 kg |
Anzahl der Regalbediengeräte: | 3 |
Höhe des Lagers: | 8,6 m |
Lagerebenen: | 19 |
Kommissionierstellen: | 2 |
Galerie
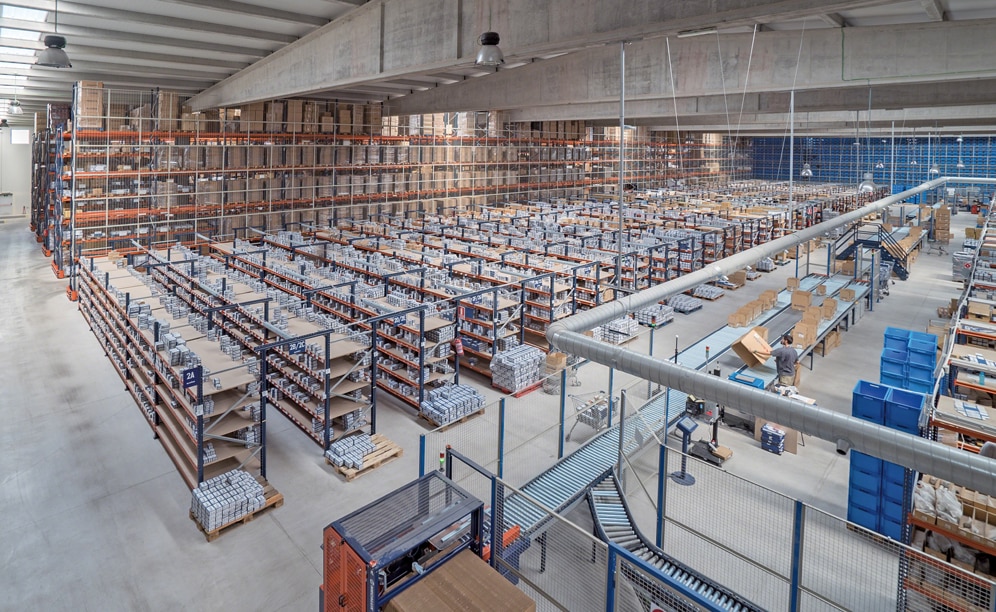
Mecalux hat alle Lagersysteme: eines automatischen Miniload-Lagers, einen vollständigen Förderkreislauf mit Stationen zur Auftragszusammenstellung, Kartonfaltmaschinen, Verschließmaschinen, Waagen und Klassifizierungsrampen geliefert
Fragen Sie einen Experten