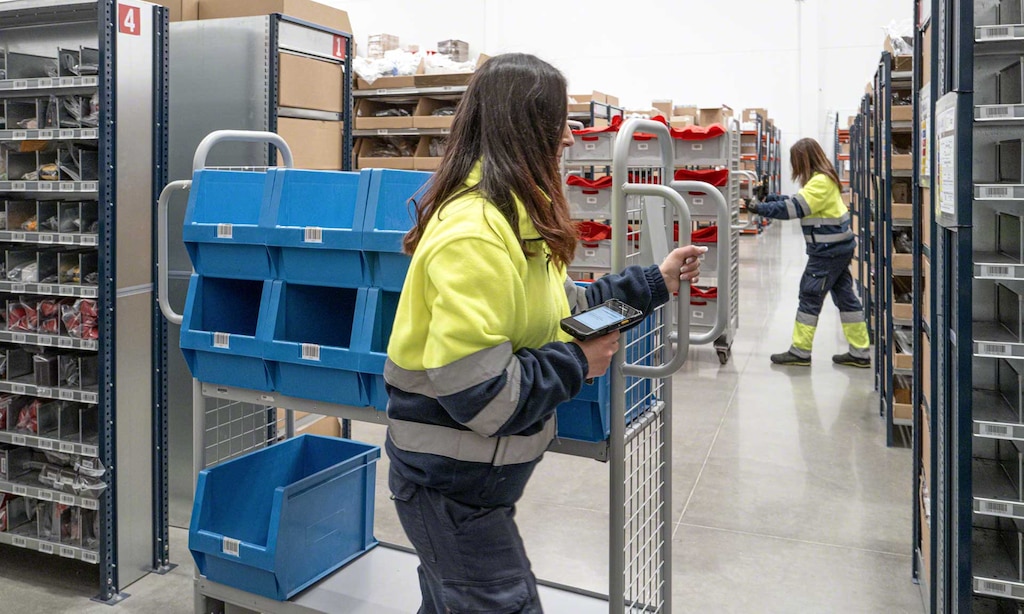
LOGISTIKFORSCHUNG
Von Shuya Zhong, Vaggelis Giannikas, Jorge Merino, Duncan McFarlane, Cheng Jun und Shao Wei
Die Kommissionierung und das Verpacken sind zwei Schlüsselprozesse in der Auftragsabwicklung. Bei der Kommissionierung werden die verschiedenen Artikel an verschiedenen Stellen des Lagers gesammelt, während beim Verpacken die Artikel in Behältern, Tüten oder Paketen verpackt werden. Beide Vorgänge sind ausschlaggebend dafür, wie lange ein Auftrag im Werk verweilt, vom Zeitpunkt des Kaufs einer Reihe von Produkten durch den Kunden bis zur Versandbereitschaft der Sendung.
In dieser Studie analysieren wir die Ergebnisse der gemeinsamen Planung von Kommissionierung und Verpackung in E-Commerce-Lagern. Um ihren Nutzen festzustellen, müssen beide Aufgaben berücksichtigt werden: Die Verbesserung nur einer dieser Tätigkeiten hat keine großen Auswirkungen, da sie untrennbar miteinander verbunden sind.
Obwohl die beiden Vorgänge eng miteinander verknüpft sind, handelt es sich bei der Kommissionierung und der Verpackung häufig um aufeinanderfolgende, aber voneinander unabhängige Prozesse, die von zwei getrennten Mitarbeiterteams durchgeführt werden. Wir sind der Meinung, dass die gemeinsame Verwaltung von Kommissionierung und Verpackung die Lagerleistung im Vergleich zur getrennten Organisation beider Vorgänge verbessert.
Drei Schlüsselfragen
Ziel ist es, nicht nur die Kommissionierung und Verpackung zu verbessern, sondern auch die dazwischen liegenden Wartezeiten zu verkürzen. Zu diesem Zweck wurden zwei Hauptparameter verwendet: die Auftragsbearbeitungszeit (die Zeit, die ein einzelner Auftrag benötigt, um versandfertig zu sein) und die Produktionszykluszeit (die Zeit, die das Lager benötigt, um eine bestimmte Anzahl von Aufträgen zu bearbeiten, bis sie versandfertig sind).
In einem E-Commerce-Lager wird eine Bestellung im Allgemeinen in eine der folgenden vier Kategorien eingeteilt, je nach Anzahl der Artikel und der bestellten Menge jedes Artikels: 1-Artikelart-1-Artikel, 1-Artikelart-mehrere-Artikel, mehrere-Artikelarten-1-Artikel und mehrere-Artikelarten-mehrere-Artikel. Diese Klassifizierung wirkt sich auf die aufzusuchenden Stellplätze sowie auf die Kommissionier- und Verpackungszeit aus.
Die Untersuchung berücksichtigt auch die verschiedenen Ebenen der für die Kommissionierung und Verpackung zuständigen Mitarbeiter. Um die potenziellen Vorteile eines ganzheitlichen Arbeitsansatzes zu bewerten, haben wir eine experimentelle Studie in einem Lagerunternehmen auf der Grundlage empirischer Daten durchgeführt und die gemeinsame Planung von Kommissionierung und Verpackung mit einer individuellen Planung anhand eines mathematischen Modells verglichen.
Die gemeinsame Verwaltung von Kommissionierung und Verpackung steigert den Lagerdurchsatz
Mit dem mathematischen Modell sollten drei Fragen beantwortet werden: Wie sollen Aufträge zu einer Kommissionierliste zusammengefasst werden? Wie sollen sich die Kommissionierer organisieren? Wie und in welcher Reihenfolge sollen die Kommissionierlisten nach Abschluss der Kommissionierung den Packern zugewiesen werden?
Zu diesem Zweck haben wir auf der Grundlage von Studien zu diesem Thema und der Tätigkeit eines bestimmten Unternehmens die folgenden Merkmale eines Lagers festgelegt. Die Anlagen arbeiten mit einem Kommissioniersystem auf niedriger Ebene, bei dem die Produkte während der Kommissionierung sortiert werden. Der Kommissionierbereich umfasst mehrere breite Gänge und einen Pufferbereich, in dem jeder Artikel an einem Stellplatz gelagert wird. Die Kommissionierer verwenden Gabelstapler - die immer verfügbar sind - und legen S-förmige Wegstrecken zurück, während die Packer an ihrem Arbeitsplatz bleiben.
Vier verschiedene Szenarien
Das untersuchte manuelle Lager ist eine Logistikplattform, die für ein Online-Einzelhandelsunternehmen betrieben wird. Es wurden verschiedene Szenarien mit unterschiedlichen Auftragsvolumina analysiert. Sie erforderten jeweils unterschiedliche Mengen und Artikel, die zudem auf eine variable Anzahl von Kommissionierlisten verteilt waren.
Wartezeiten und Ausführung der Kommissionierung und Verpackung mit integrierten und nicht integrierten Methoden
Gibt es mehr Packer als Kommissionierer, tritt die Zeitersparnis ein, bevor die Kommissionierung beginnt
- Bei 300 Aufträgen und maximal 24 Kommissionierlisten konnten durch die gemeinsame Organisation von Kommissionierung und Verpackung die Bearbeitungszeit und die Produktionszykluszeit reduziert werden. Um dies zu erreichen, erfolgt die Kommissionierung bei der integrierten Methode mit etwas geringerer Effizienz, sodass eine erhebliche Zeitersparnis in der Verpackungsphase erzielt wird.
- In Szenarien mit 100-600 Aufträgen, die auf 8 bis 48 Kommissionierlisten verteilt sind, zeigt sich, dass mit zunehmender Auftragsanzahl die Vorteile einer gemeinsamen Verwaltung von Kommissionierung und Verpackung tendenziell abnehmen.
- Bei der Überprüfung von 300 Aufträgen mit unterschiedlicher Zusammensetzung - wobei das Verhältnis von 1-Artikelart-1-Artikel, 1-Artikelart-mehrere Artikel, mehrere-Artikelarten-1-Artikel und mehrere-Artikelarten-mehrere-Artikel variiert - konnte festgestellt werden, dass die integrierte Methode die Leistung erhöht. Der Vorteil dieser Methode zeigt sich besonders dann, wenn die Komplexität der zu bearbeitenden Sendungen eher gering ist.
- Zwölf Mitarbeiter werden auf verschiedene Weise verteilt, um die Anzahl der Kommissionierer und Packer zu variieren und 300 Aufträge mit 24 Kommissionierlisten zu bewältigen. Wenn es mehr Kommissionierer als Packer gibt, besteht der Vorteil der integrierten Methode darin, die Zeit vor der Verpackungsphase zu verkürzen. Gibt es mehr Packer als Kommissionierer, tritt die Zeitersparnis ein, bevor die Kommissionierung beginnt. Das bedeutet, dass in einigen Szenarien, in denen es nicht möglich ist, das Verpacken zu beschleunigen, die gemeinsame Organisation von Kommissionierung und Verpackung nicht von Vorteil ist.
Ergebnisse: kleinere Kommissionierwellen
Unsere Ergebnisse belegen, dass die gemeinsame Planung von Kommissionierung und Verpackung die Leistung unter verschiedenen Bedingungen optimieren kann. Es hat sich gezeigt, dass der Fokus auf Veränderungen bei der Kommissionierung allein keine systemweiten Verbesserungen garantiert, wenn die Verpackung weiterhin einen Engpass darstellt. Darüber hinaus können kleine Kompromisse bei der Kommissionierung eine große Zeitersparnis bei der Verpackung bewirken und die Gesamteffizienz steigern.
In ähnlicher Weise ist die Auftragsanzahl, die für die Arbeitsverteilung in Frage kommt, und der Nutzen, den die gemeinsame Planung bringen kann, umgekehrt proportional. Dies verdeutlicht, wie wichtig es ist, vor Beginn eines Prozesses, z. B. einer Wellenkommissionierung, festzulegen, wie viele Aufträge gruppiert werden sollen. In der Praxis kann es daher besser sein, sich für mehrere kleinere Wellen zu entscheiden, um den größten Nutzen aus der gemeinsamen Planung zu ziehen.
AUTOREN DER STUDIE:
- SHUYA ZHONG. Außerordentliche Professorin für Logistik und Lieferketten an der Universität Bath (UK).
- VAGGELIS GIANNIKAS. Professor für Technologie und Betriebsmanagement und Direktor des Zentrums für intelligente Lager- und Logistiksysteme an der Universität Bath (UK).
- JORGE MERINO. Forschungsbeauftragter am Institute of Manufacturing, Universität Cambridge (UK).
- DUNCAN McFARLANE. Professor für Wirtschaftsinformatik an der Fakultät für Ingenieurwesen der Universität Cambridge und Direktor des Labors für verteilte Informationen und Automatisierung am dortigen Institute of Manufacturing (UK).
- JUN CHENG. Shenzhen YH Global Supply Chain Co., Ltd (China).
- WEI SHAO. Shenzhen YH Global Supply Chain Co., Ltd (China).
Originalveröffentlichung:
Zhong, Shuya, Giannikas, Vaggelis, Merino, Jorge, McFarlane, Duncan, Cheng Jun, Shao Wei. 2022. „Evaluating the benefits of picking and packing planning integration in e-commerce warehouses“. European Journal of Operational Research, 301 (Elsevier).
Frei zugängliche Version hier verfügbar.