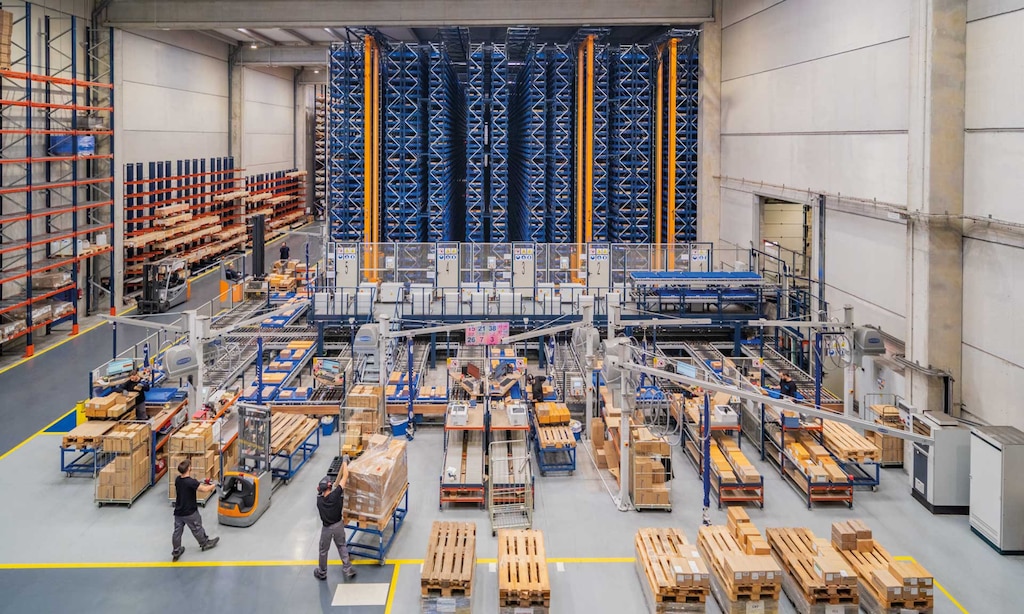
LOGISTIKFORSCHUNG
Von Diego Pacheco, Daniel Møller Clausen und Jendrik Bumann
Lager bilden eine zentrale Säule der Lieferkette und der Erfahrungen des Endkunden. Die Verantwortlichen dieser Anlagen sind jedoch mit stetig auftretenden Schwierigkeiten konfrontiert, die sie täglich zu bewältigen haben. Einige der kritischsten Punkte sind unzureichende Qualitätskontrollen, redundante Prozesse, schlecht umgesetzte Konzepte und ungenaue Informationen über den Bestand. Wenn nichts unternommen wird, können alle diese Faktoren zu zusätzlichen Kosten, Leistungseinbußen und Unzufriedenheit bei den Benutzern führen.
Im Produktionssystem von Toyota werden Aktivitäten, die keinen Mehrwert schaffen, als „Muda“ bezeichnet. Zu den sieben Arten von Verschwendung gehören Wartezeiten, Überproduktion, übermäßiger Warenumschlag, unnötige Umlagerungen, unzureichende Verarbeitung, Mängel und Überbestände.
Die Kenntnis des aktuellen Zustands des Lagers ist ein wesentlicher Schritt zur Ermittlung von Verschwendungen innerhalb des Lagers. Dies geschieht u. a. durch Datenanalyse, Lagerbeobachtung, Interviews oder Fragebögen, Pareto-Analyse der Lean-Produkte und -Ressourcen, wie z. B. Value Stream Mapping (VSM) oder Genba Shikumi, d. h. ein quantitatives Instrument, das auf Vektoren und aufeinander folgenden Korrelationsmatrizen beruht. Und wenn eine hohe Leistung und Wettbewerbsfähigkeit im Betrieb erreicht werden soll, müssen kontinuierliche Verbesserungsprogramme umgesetzt werden.
Engpässe in einem Vertriebslager
In der Studie wurde der Betrieb eines dänischen Vertriebslagers untersucht, das zu einem KMU gehört. Das Unternehmen beschäftigt einen Lagerleiter in Vollzeit und einen Assistenten in Teilzeit und vertreibt seine Produkte in ganz Europa auf B2B- und B2C-Basis. Zunächst wurden Strategien zur Ermittlung und Verringerung der betrieblichen Verschwendung ausgearbeitet, und dann wurden die Ergebnisse auf dieses Unternehmen angewandt.
Bei ersten Kontakten stellte unser Forschungsteam fest, dass sich die Geschäftsleitung der Tatsache bewusst war, dass eine Reihe von betrieblichen Problemen die Unternehmensleistung beeinträchtigte. Wenn das Unternehmen nicht proaktiv auf die Situation reagiert, könnte dies die Skalierbarkeit des Unternehmens auf dem Markt beeinträchtigen.
Die Datenerhebung für die Analyse wurde in mehreren Phasen durchgeführt. Zunächst wurde ein Gespräch mit dem Inhaber des Unternehmens geführt, um das Unternehmen, seine Mitarbeiter und die Probleme der Anlage näher kennen zu lernen. In der Folge wurden drei Besuche durchgeführt und weitere Beobachtungen gesammelt. Außerdem wurde ein Fragebogen verteilt, um Informationen von Lieferanten und Lieferungen zu sammeln, und es wurden Verkaufs- und Bestandsberichte zur Ermittlung des Nutzens der einzelnen Produktgruppen herangezogen.
Aufdeckung unzureichender Prozesse
Wir haben erkannt, dass das Entladen und Sortieren der Waren bei ausbleibendem Regen unter freiem Himmel und mit mehr Platz erfolgen kann. In Bezug auf die Verpackung und den Versand war der wichtigste Faktor die Verfügbarkeit geeigneter Behälter und Füllstoffe. Bei der Ankunft eines Lastwagens gab es kein System, um die Artikel zu erfassen, und bei der Kommissionierung war die Ware manchmal nicht auffindbar. In solchen Fällen musste der Kommissionierer entweder nach dem Artikel suchen, einen Kollegen um Hilfe bitten oder den Auftrag ohne eines der Produkte abschließen. Wenn es keine geeignete Verpackung gab, musste der Lagermitarbeiter ein Behältnis aus dem Lager holen.
Das Unternehmen versendet im Durchschnitt 128 Produkte pro Tag in einer einzigen Sendung. Sein Hauptlieferant schickt ihm alle zwei Monate 367 Pakete mit 9.715 Artikeln. Obwohl die Kommunikation zwischen den beiden Unternehmen per E-Mail stattfindet, erfolgt der Informationsfluss innerhalb des Unternehmens immer noch manuell.
Ohne ein System zum Auffinden von Artikeln bleibt das gesamte Wissen über die Bestände in den Händen des Leiters. Sollte dieser längere Zeit abwesend sein, ist das Unternehmen anfällig für mögliche Fehler
Da es nur eine Vollzeitkraft gibt, müssen die Büroangestellten beim Entladen der Lastwagen helfen. Dauert es länger als eine Stunde, muss das Lieferunternehmen zusätzlich dafür bezahlt werden, und ohne Hilfsmittel ist die körperliche Arbeit anstrengend. Da die Beladung nach dem Zufallsprinzip erfolgte, werden die Produkte erst beim Verlassen des Lastwagens nach Kategorien sortiert, was sehr zeitaufwendig ist.
Ohne ein System zum Auffinden von Artikeln bleibt das gesamte Wissen über die Bestände in den Händen des Lagerleiters. Sollte dieser für längere Zeit abwesend sein, ist das Unternehmen anfällig für mögliche Fehler. Aufgrund mangelnder Informationen über das Inventar und einer begrenzten Ausbildung werden von den Lagermitarbeitern viele Fragen gestellt, was die Arbeit des Managers und des Büropersonals erschwert.
Bei der Auswahl der Artikel begann die Kommissionierung mit der Entgegennahme eines Bestellscheins durch einen Lagermitarbeiter. Anschließend benutzte er diesen als Kommissionierliste und legte ihn auf ein Tablar. Wir haben festgestellt, dass es zu Verzögerungen bei früheren Aufträgen kam, wenn ein neu eingegangener Auftrag oben statt unten im Tablar abgelegt wurde. Die Etiketten auf den Behältern sind klein und undeutlich, so dass sie schwer zu lesen sind. Die Behälter sind übereinander gestapelt, was die Handhabung erschwert. Ohne ein Lagerverwaltungssystem müssen sich die Mitarbeiter auf ihr Gedächtnis verlassen, um den schnellsten Weg zu finden – eine zusätzliche Herausforderung für Zeitarbeiter.
Ergebnisse und Übersicht über Wertschöpfung
Die Ergebnisse ergaben, dass die meisten Vorgänge im Lager verbessert werden können. Obwohl das Unternehmen gewachsen ist, hat es seine Arbeitsweise nicht geändert, was zu zahlreichen Problemen geführt hat, wie z. B. die doppelte Handhabung von Waren. Gleichzeitig erhalten die Lagermitarbeiter keine Rückmeldung von den Kunden über ihre Arbeit, und sie können auch nicht sehen, welche Fehler sie begangen haben.
Die Untersuchung ergab, dass die drei größten Verschwendungsquellen des dänischen Unternehmens Wartezeiten, übermäßige Handhabung von Waren und unnötige Umlagerungen waren. Neben den allgemeinen Abläufen erfordern auch das Entladen und die Sortierung der Waren dringende Aufmerksamkeit. Daher wurde eine Reihe von Änderungen für eine bessere Funktionsweise des Lagers vorgeschlagen, die in die zukünftige Wertstromkarte aufgenommen wurden (Abbildung).
Die wichtigste in der neuen Wertschöpfungsübersicht vorgeschlagene Änderung war die Einführung eines Lagerverwaltungssystems (LVS oder WMS auf Englisch). Dieses System erweitert den gesamten Wertstrom und verfügt über Daten aller Artikel. Es liefert Informationen über Lieferantenlieferungen im Voraus, so dass sich die Lagermitarbeiter schon vor dem Eingang der Ware darauf einstellen können. Es sorgt dafür, dass genügend Platz im Lager vorhanden ist, indem es jedem Produkt vor seiner Ankunft einen Stellplatz zuweist. In diesem Fall wäre es auch mit Voice-Picking-Programmen verbunden. Da es Advanced Shipping Notices (ASNs) lesen kann, gibt es auch Warnungen in Bezug auf Entlade- und Sortiervorgänge aus.
Eine weitere Schlussfolgerung war die Einführung von Standardarbeitsanweisungen (SOPs) für den Lieferanten, den Entlade- und Sortierprozess und die Verpackung. Zu diesen Verfahren gehören Anforderungen an die Größe und Sichtbarkeit der Etiketten sowie an die Strukturierung der Artikel vor dem Versand.
Einsatz eines Lagerverwaltungssystems
Ein LVS würde sich positiv auf alle Lagerabläufe auswirken – unabhängig davon, ob es allein oder integriert mit einem ERP-System (Enterprise Resource Planning) eingesetzt wird. Durch die Einführung eines LVS können Wartezeiten, eine übermäßige Handhabung von Waren und unnötige Umlagerungen reduziert werden. Die Anwendung und Erarbeitung von Absatzprognosen trägt wiederum zu genaueren Lagerbeständen und zur Vermeidung von Fehlbeständen bei.
Eines dieser Programme kann Slotting-Probleme (optimierte Lagerplatzfindungsprobleme) lösen und den Stellplatz neuer Artikel nach der ABC-Methode vorhersagen. Es sorgt dafür, dass schwerere Produkte in der Nähe der Kommissionierstationen gelagert werden, und platziert Produkte, die normalerweise zur gleichen Zeit verkauft werden, in der Nähe. Es kann auch als Planungsinstrument dienen und ermitteln, ob genügend Behälter unterschiedlicher Größe zum Verpacken der Waren vorhanden sind.
Die Leistung des Lagers wirkt sich auf mehrere Bereiche aus, und die Verbesserung der Lagerprozesse bringt Vorteile für das gesamte Unternehmen mit sich
Durch die Untersuchung und das Verständnis der Ursachen für die betriebliche Verschwendung wird den Mitarbeitern die Bedeutung ihrer Arbeit bewusst, was wiederum die Arbeitszufriedenheit erhöht. Die Ergebnisse zeigen, dass die Bewältigung dieser Situationen zu einer besseren Zuweisung von Ressourcen führt, was das Unternehmenswachstum und neue Geschäftsmöglichkeiten fördert.
Die Leistung des Lagers wirkt sich auf mehrere Bereiche aus, und die Verbesserung der Lagerprozesse bringt Vorteile für das gesamte Unternehmen mit sich. So zeigt die Wertschöpfungsübersicht des dänischen Einzelhändlers eine Gesamtproduktionszeit von 1.721,29 Stunden. Nach der Einführung eines LVS und der Umsetzung von Verbesserungen in allen Arbeitsabläufen würde sich diese Zeit um 41,4 % verringern.
AUTOREN DER STUDIE:
Diego Pacheco, Daniel Møller Clausen und Jendrik Bumann. Abteilung für Technologie und Unternehmensentwicklung, Fakultät für Wirtschafts- und Sozialwissenschaften, Universität Aarhus (Dänemark).
Originalveröffentlichung:
De Jesús Pacheco, Diego Augusto, Møller Clausen, Daniel, Bumann, Jendrik. 2023. „A multi-method approach for reducing operational wastes in distribution warehouses“, in International Journal of Production Economics 256 (Elsevier).
© The Authors. Licensed under CC BY 4.0