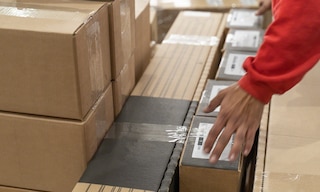
„Double Handling“: Beispiel für „Lean Waste“ in der Logistik
Beim Double Handling handelt es sich um die übermäßig häufige Handhabung von Waren, wodurch die Produktivität in Logistikanlagen sinkt. Durch Ineffizienz bei der Bewegung von Waren oder der Auftragszusammenstellung kommt es zu Kostenüberschreitungen, Materialverlusten, unpünktlichen Lieferungen und infolgedessen zu einem schlechteren Service für den Endkunden.
Die Einführung neuer Technologien im Lager schränkt die Auswirkungen des Double Handling ein: Eine Lagerverwaltungssoftware (LVS) führt die Lagermitarbeiter durch die auszuführenden Aufgaben, automatisiert die Entscheidungsfindung und gewährleistet, dass die Aufträge in kürzester Zeit und mit maximaler Produktivität abgewickelt werden. Mit Roboterlösungen wie Förderbändern, mobilen Robotern oder automatisierten Handhabungsgeräten wird auch eine übermäßig häufige Handhabung von Waren verhindert, indem unnötige Bewegungen vermieden werden und die volle Leistungsfähigkeit der Anlage gewährleistet wird.
Was ist das „Double Handling“ im Lager?
Der Effekt des Double Handling entsteht, wenn Ineffizienzen bei Vorgängen wie dem Nachschub von Produkten oder der Auftragszusammenstellung auftreten. Infolgedessen müssen die Lagermitarbeiter bei der internen Beförderung von Waren mehr Zeit oder mehr Bewegungen einplanen. Einer der Gründe für dieses ineffiziente Vorgehen ist die fehlende Optimierung der Routen in einer Logistikanlage. Dadurch wird Zeit verschwendet und das Risiko erhöht, dass Waren oder Lagersysteme während des Transports beschädigt werden.
Überflüssige Prozesse und Bewegungen in einem Lager erhöhen die Dauer der Auftragsabwicklung, was sich auf den Service für den Endkunden auswirkt. Der wissenschaftliche Artikel An efficient approach to investigate the tradeoff between double handling and needed capacity in automated distribution centers beschreibt ein Beispiel für das „Double Handling“ in einem Palettenlager: „Das Double Handling liegt vor, wenn der tägliche Bedarf geringer ist als die Größe der Palette, so dass nur einige Behälter mithilfe von Depalettierern von der Palette genommen werden und der Rest der Behälter gelagert wird, bis er benötigt wird.“ Durch die Minimierung des „Double Handling“ können Unternehmen ihren Logistikservice verbessern, die mit den Kunden vereinbarten Aufträge pünktlich ausliefern und folglich Marktanteile hinzugewinnen.
„Double Handling“, „Muda“ und „Lean“-Methode
Das doppelte Handling von Produkten oder unnötige Bewegungen der Lagermitarbeiter sind Beispiele für Lean Waste. Bei der Lean Logistics werden Aktivitäten und Prozesse, die keinen Mehrwert schaffen und die Effizienz der Abläufe verringern können, identifiziert und beseitigt. Eine schlechte Routenplanung im Lager kann z. B. zu unnötigen Transportwegen und damit zu Ineffizienzen bei der Auftragszusammenstellung führen.
In der Lean-Logistik wird der aus dem Japanischen stammende Begriff Muda verwendet, um alle Prozesse zu beschreiben, die eine Art von Verschwendung erzeugen oder dem Endprodukt oder der Dienstleistung keinen wirklichen Mehrwert verleihen. Durch das „Double Handling“ von Waren steigen die Kosten und die Effizienz der Unternehmenslogistik wird beeinträchtigt. Zu viele Bewegungen sind nicht die einzigen Muda, die in einem Lager auftreten können. Eine sinnlose Anhäufung von Beständen und ganz allgemein eine schlechte Bestandsverwaltung können auch zu Platzverschwendung oder Veralterung der gelagerten Produkte führen.
Was sind die Ursachen für ein „Double Handling“?
Gehen Materialien in einem Lager ein, müssen die Produkte einer vorher festgelegten Route folgen, um eine überflüssige Bewegung oder Handhabung von Waren zu vermeiden. Dies sind oft die Hauptursachen für ein Double Handling:
- Fehlen eines Plans für die Platzierung und den Nachschub von Produkten. Eine unzureichende Bestandsplanung führt häufig dazu, dass die Bestände an den falschen Stellen gelagert werden. Dies hat zur Folge, dass Artikel in einen anderen Lagerbereich befördert werden müssen und Platz beanspruchen, der eigentlich für andere Produkte genutzt werden sollte.
- Kommunikationsfehler zwischen dem Lager und anderen Abteilungen des Unternehmens, z. B. der Produktion. Ein Mangel an reibungsloser Kommunikation kann zu Engpässen oder einem Mangel an Beständen in den Produktionslinien führen.
- Ein Mangel an Lagerraum oder andernfalls schlechte Verteilung der Produkte. Fehler in der Logistikplanung oder im Lagerlayout können zu unnötigen Bewegungen von Mitarbeitern und Waren führen.
- Falsche Verwendung von Ausrüstung, Hilfsmitteln oder Handhabungsgeräten. In einem manuellen Lager kann z. B. der Einsatz von ungeeigneten Flurfördermitteln den Betrieb verlangsamen.
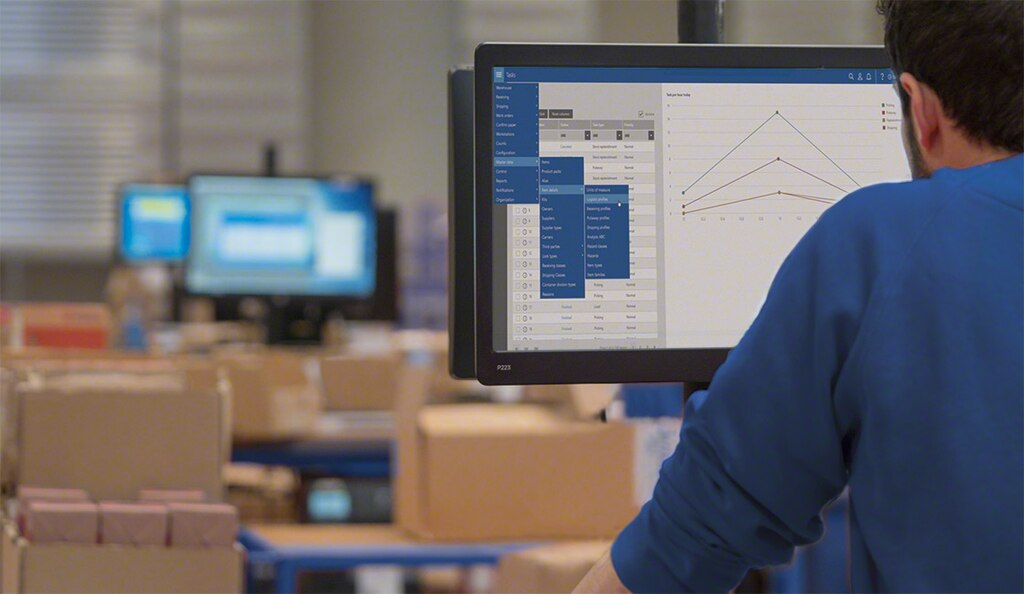
Wie kann man den Effekt des „Double Handling“ verringern?
Zur Vermeidung des „Double Handling“ und überflüssigen Bewegungen empfiehlt es sich, die manuelle Warenverwaltung durch eine digitale Lösung wie eine Lagerverwaltungssoftware zu ersetzen. Dieses Logistikprogramm koordiniert alle Vorgänge innerhalb der Anlage, wie z. B. die Zuweisung von Stellplätzen im Lager. Die Software bestimmt anhand einer Reihe von Regeln und Kriterien, die vom Logistikverantwortlichen im Voraus festgelegt wurden, den idealen Stellplatz, wodurch das Risiko von Ineffizienzen – Fehlern oder „Double Handling“ – beim Nachschub begrenzt wird.
Eine erweiterte Verwaltungssoftware ist auch für die Planung der Kommissionierrouten und der Routen der Handhabungsgeräte zuständig, um zwei Ziele zu gewährleisten: Effiziente und sichere Bewegungen von Lagermitarbeitern und Waren. Das Programm berücksichtigt die Anzahl der vorzubereitenden Aufträge und die Verteilung der Produkte, um die Route für jeden Mitarbeiter zur Maximierung seiner Leistung zu bestimmen.
Mit automatisierten Lösungen – wie z. B. Förderanlagen, Regalbediengeräten oder mobilen Robotern – lassen sich die Risiken des „Double Handling“ vermeiden und die Waren optimal bewegen. Die Verwaltungssoftware ist bei diesen Lösungen das Gehirn der Anlage, das die Bewegung der Roboter und der Waren koordiniert. Mithilfe von Roboterlösungen wird die Strategie Goods-to-Person unterstützt, bei der sich die Produkte selbstständig zu den Lagermitarbeitern bewegen. Durch die Automatisierung wird die Anzahl der Bewegungen und Handhabungsvorgänge reduziert, um eine maximale Rentabilität des Lagerbetriebs zu gewährleisten.
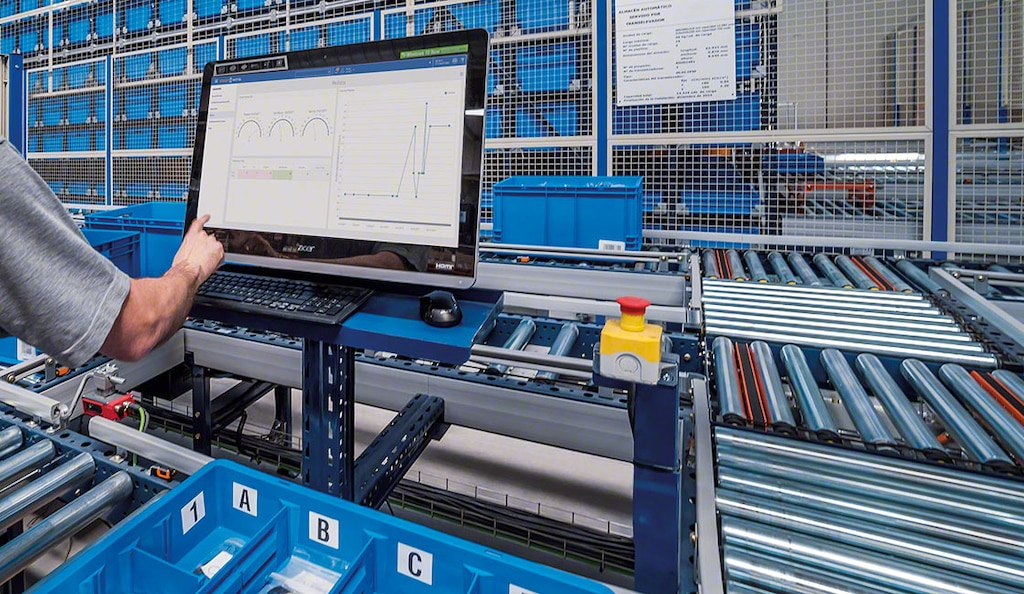
Fortschrittliche Lösungen zur Vermeidung von Ineffizienzen im Lager
Die fehlende Optimierung der Bewegungen im Lager ist ein klares Symptom für Lean Waste und damit für logistische Ineffizienz. Mit neuen Technologien wird das Risiko von Fehlern, die durch das Double Handling entstehen, begrenzt. In manuellen Lagern koordiniert eine Verwaltungssoftware wie Easy WMS die Bewegungen der Waren und der Lagermitarbeiter, um unproduktive Abläufe zu vermeiden.
Der Einsatz von Roboterlösungen wie Regalbediengeräten, Förderanlagen oder mobilen Robotern automatisiert zudem den Warentransport und steigert die Leistung der Anlage. Mecalux verfügt über umfangreiche Erfahrung bei der Entwicklung von Lager- und Softwarelösungen für alle Arten von Unternehmen. Wenden Sie sich an uns, und ein fachkundiger Berater wird Sie hinsichtlich der besten Lösung für Ihre Anlage beraten.