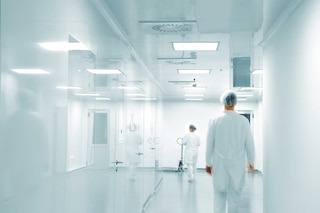
Reinräume bzw. Reinsträume: Wie können Kontaminationen vermieden werden?
Reinräume bzw. Reinsträume entstanden aus der Notwendigkeit von Industriezweigen wie der Pharma-, Lebensmittel- oder der Chemieindustrie heraus, luftgetragene Partikel zu vermeiden, damit Produkte nicht kontaminiert werden. Eine derartige Kontamination könnte die Qualität der Produkte beeinträchtigen oder sogar Infektionen verursachen, was ernsthafte gesundheitliche Risiken für den Menschen sowie wirtschaftliche Risiken für das Unternehmen und für dessen Ruf bedeuten würde.
Aus diesem Grund müssen Unternehmen in bestimmten Branchen über Reinräume verfügen, die auch als cleanrooms bezeichnet werden. Hierbei handelt es sich um Räume, die speziell dafür entwickelt wurden, bestimmte Umgebungsbedingungen aufrecht zu halten und einen Verunreinigungsgrad von Null zu erreichen. Zu diesem Zweck ist es zwingend erforderlich, dass der Aufbau und die Gestaltung dieser Räume den Vorschriften hinsichtlich ihrer Nutzung entsprechen. Gleichzeitig ist es unerlässlich, sie regelmäßig und gründlichst zu reinigen und zu desinfizieren.
In diesem Artikel wird erläutert, was Reinräume sind, wie sie aufgebaut sind, was ihre Anwendungsbereiche sind und wie man sie in ein Lager integriert.
Was ist ein Reinraum?
Bei einem Reinraum handelt es sich um einen sauberen und sterilen Arbeitsbereich, in dem die Lufthygiene, der Druck, die Temperatur, die Luftfeuchtigkeit und die Beleuchtung innerhalb der durch die geltenden Vorschriften festgelegten Grenzwerte streng kontrolliert werden. Dort können verschiedene Prozesse und Vorgänge sicher durchgeführt werden, wobei jegliche Form von Kontamination ausgeschlossen ist.
Diese Anlagen müssen speziell konstruiert und gestaltet werden und über eine geeignete Ausstattung verfügen (Lüftungssysteme mit HEPA-Filtern, Luftduschen, Reinraumtüren, ...). Ausschließlich autorisiertes Personal darf den Reinraum betreten, um die entsprechenden Arbeiten auszuführen, ohne die Produkte Krankheitserregern auszusetzen, die sie kontaminieren könnten.
Anwendungsbereiche von Reinräumen
Das Konzept der Reinräume stammt ursprünglich aus Operationssälen in Krankenhäusern. Um chirurgische Eingriffe vorzunehmen, ist es unerlässlich, diese Räume korrekt zu belüften, die verwendeten Geräte zu sterilisieren und strenge Hygienevorschriften einzuhalten.
Anschließend fanden Reinräume nach und nach in der Industrie Anwendung, um in der Produktion den Kontaminationsgrad kontrollieren zu können, was zur Gewährleistung der Sicherheit der hergestellten Produkte unerlässlich ist. Folglich werden sie heutzutage in vielen Bereichen eingesetzt: im Lebensmittel- und Gesundheitssektor, in der Technologie usw.
Mikroorganismen in der Umgebungsluft können die Eigenschaften bestimmter Produkte verändern. Im Falle von Lebensmitteln (Fleisch-, Fisch-, und Milchprodukte, Gemüse oder vorgekochte Lebensmittel) können sie beispielsweise ein Gesundheitsrisiko darstellen und zu Vergiftungen und Infektionen führen.
Vorschriften für Reinräume
Die Kontrolle und Verringerung des Kontaminationsgrades in einem Reinraum ist keine leichte Aufgabe und erfordert eine sehr präzise Gestaltung des Reinraums. Dabei müssen zahlreiche Aspekte beachtet werden: von den technischen Spezifikationen für den korrekten Betrieb, wobei die Verwendung von HEPA-Filtern besonders wichtig ist, über die Bauvorschriften oder die erforderlichen Geräte bis hin zum Personal- und Warenfluss.
Beim Planungs- und Konstruktionsprozess finden zwei Normen Anwendung, die festlegen, wie ein Reinraum auszusehen hat:
- Gute Herstellungspraktiken (Good Manufacturing Practice, GMP). Hierbei handelt es sich um einen internationalen Standard für die Herstellung von Medikamenten, Kosmetika oder Lebensmitteln unter optimalen Bedingungen. In Europa wird er durch die Verordnung 1223/2009 des Europäischen Parlaments und des Rates geregelt. Um diese einzuhalten, ist es nicht nur erforderlich, dass die Reinheit der Luft gewährleistet ist, sondern auch, dass der Reinraum eine gute Temperaturverteilung, eine geeignete Beleuchtung und entsprechende Brandschutzeinrichtungen aufweist. Darüber hinaus müssen sterile Materialien verwendet werden und die Oberflächen, auf denen die Vorgänge durchgeführt werden, müssen keimfrei gehalten werden.
- DIN EN ISO 14644. Dies ist eine von der Internationalen Organisation für Normung (ISO) erarbeitete internationale Norm, die die Hygiene der Luft in Reinräumen regelt. Diese Norm teilt Reinräume in neun Klassen ein und legt Höchstgrenzen für die Partikelmenge in den Räumen fest. Je nach Branche kann die Klassifizierung mehr oder weniger streng sein. Sie reichen von nur 0,2 Mikrometern Partikel pro Kubikmeter Luft (in Luft- und Raumfahrt, im pharmazeutischen Bereich oder im Krankenhaus) bis hin zu 293.000 Mikrometern. Das Hauptziel des Baus eines Reinraums besteht darin, die Entstehung, das Zurückbleiben und das Eindringen von kontaminierenden Partikeln in diesen Raum zu minimieren.
Gestaltung und Aufbau eines Reinraums
Bei der Planung eines Reinraums muss entschieden werden, wie der Raum aufgeteilt wird, wie die Wandverkleidungen, Türen, Fenster oder der Boden beschaffen sein sollen, sowie wie die Filterung und der Zugang erfolgen. Dabei müssen die jeweilige vorgesehene Nutzung des Reinraums und die äußeren Bedingungen berücksichtigt werden.
Die für den Bau der Reinräume verwendeten Materialien müssen einem hochwertigeren Qualitätsstandard entsprechen als die Materialien, die beim Bau anderer Gebäudearten eingesetzt werden. Der Grund dafür ist, dass sie verschiedene Bedingungen erfüllen müssen: Langlebigkeit, physische und chemische Widerstandsfähigkeit, leichte Reinigung und gutes Brandverhalten.
Die Norm DIN EN ISO 14644 beinhaltet einige Aspekte hinsichtlich des Aufbaus eines Reinraums:
- Wandverkleidungen und Dächer. Reinräume müssen aus Verbundplatten gebaut werden, die über zwei Außenflächen in der Regel aus verzinktem Stahlblech sowie über einen inneren Kern verfügen, der für Steifigkeit sorgt und dem Paneel zusätzliche Eigenschaften wie ein optimales Brandverhalten und eine gute Wärmedämmung verleiht. Die Verbindung der verschiedenen Platten muss äußerst präzise erfolgen, um das Eindringen von Mikroorganismen und die Ansammlung von Staub zu vermeiden und die Reinigung zu erleichtern.
- Türen und Fenster. Die Türen müssen ebenfalls aus isolierenden Verbundplatten bestehen und die Fenster müssen eine Doppelverglasung aufweisen.
- Böden. Je nach Bewegungsfluss im Raum kann ihre Oberfläche unterschiedlich beschichtet sein. Idealerweise sollten sie glatt sein, um die Ansammlung von Schmutz zu verhindern, sowie leicht zu reinigen und widerstandsfähig gegen Mikroorganismen.
- Beleuchtung. Es müssen neutralweiße Leuchtstoffröhren verwendet werden.
Als nächstes wird bei der Gestaltung von Räumen die Filterung, eines der wesentlichen Kriterien für Reinräume, festgelegt. Die Luft, die in diesen abgedichteten Raum eintritt, wird gefiltert, um Schwebeteilchen zu entfernen, und mehrmals täglich erneuert, um zu verhindern, dass Staub entsteht. Daher werden HEPA-Filter verwendet, die aus Glasfasern bestehen, die Mikroorganismen auffangen.
Reinräume müssen darüber hinaus klimatisiert werden, wodurch gute Arbeitsbedingungen für das Personal geschaffen werden und das Risiko einer Kreuzkontamination minimiert wird. So wird gewährleistet, dass der Fertigungsprozess einwandfrei abläuft.
Außerdem wird die Installation eines Schleusensystems (Security Airlock System, SAS) nachdrücklich empfohlen, das aus einer Schleusenkammer besteht, die über zwei Schnelllauftüren verfügt. Eine der Türen führt in den Reinraum hinein und die andere aus der Kammer hinaus, wobei beide Türen niemals gleichzeitig geöffnet sind. Durch dieses System werden plötzliche Temperatur- und Druckänderungen beim Zutritt zum Reinraum vermieden.
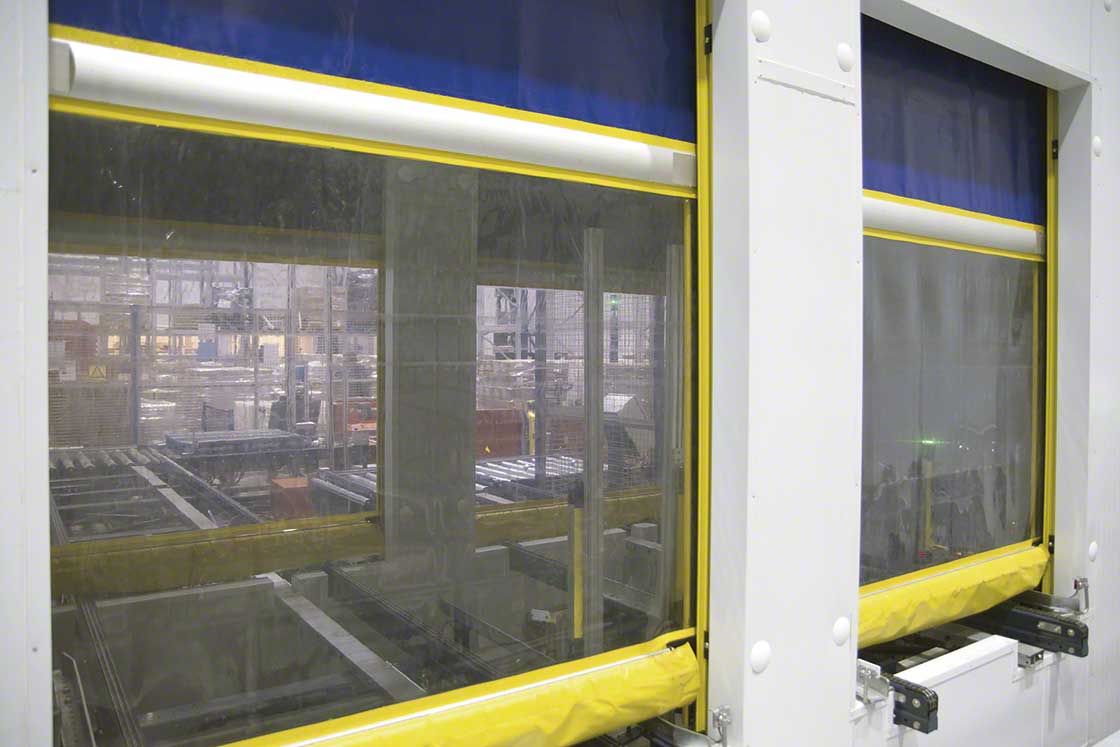
Die Bedeutung von Sauberkeit in Reinräumen
Nach der Planung und dem Bau des Reinraums ist es ebenso wichtig, diesen instand zu halten. Die Grundvoraussetzung in Reinräumen ist die Reinheit. Es ist daher unerlässlich, die Sauberkeit von Personal und Material zu kontrollieren. Zu diesem Zweck müssen die Bediener entsprechend geschult werden und sich der Bedeutung dieses Aspekts bewusst sein. Im Inneren des Reinraums muss Kleidung getragen werden, die speziell dafür ausgelegt ist, Verunreinigungen aufzufangen, die Haut und Körper auf natürliche Weise produzieren. In einigen Fällen ist zusätzlich das Tragen von Haarnetzen, Handschuhen und Masken verpflichtend.
Ein weiterer wichtiger Punkt bei Reinräumen sind die Zugänge, da hier die Gefahr des Eindringens von Partikeln am größten ist. Um dieses Risiko zu minimieren, werden für die Mitarbeiter Luftduschen installiert. Dabei handelt es sich um Kabinen, die dazu dienen, Keime, die Menschen mit in die Reinräume tragen könnten, abzutöten, bevor sie diese betreten.
Reinräume in Lagern
Im Bereich der Logistik findet das Konzept des Reinraums eine klare Anwendung: in Gefrier- und Kühlräumen. Hierbei handelt es sich um isolierte Kammern, die die Übertragung von Wärmeenergie verhindern. Kälte ist eine der gebräuchlichsten Methoden, um Produkte, hauptsächlich Lebensmittel oder Medikamente, für eine bestimmte Zeit zu konservieren.
Um die thermische Isolierung einer Kammer zu gewährleisten, müssen die Wände, Decken, Böden und Türen aus energiebeständigen Materialien bestehen. Außerdem müssen Kompressoren und Verdampfer im oberen Bereich des Gebäudes angebracht werden. Vorrangiges Ziel ist die Aufrechterhaltung einer stabilen Temperatur während des gesamten Logistikprozesses sowie die Vermeidung kritischer Momente, die die Kühlkette der Produkte unterbrechen könnten.
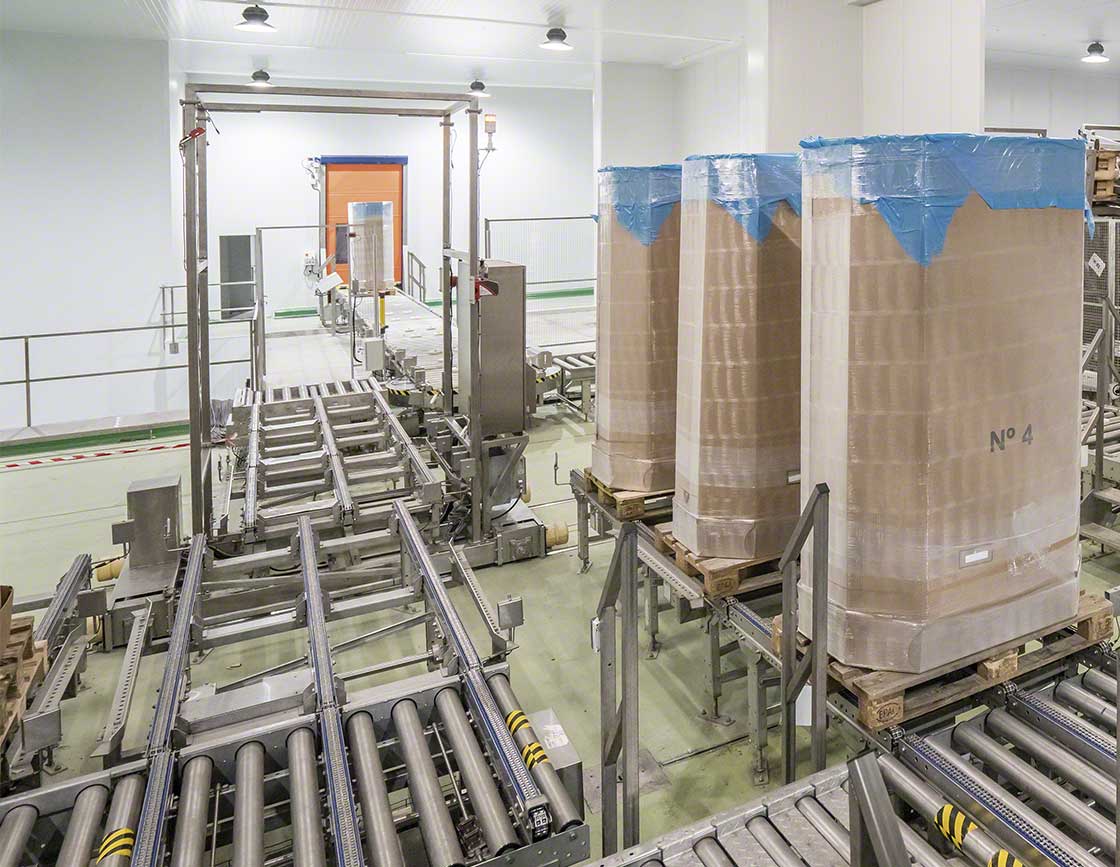
Es ist gängige Praxis, Kammern in Silobauweise zu errichten, die bei kontrollierter Temperatur betrieben werden. Bei diesem System besteht die Struktur des Gebäudes aus den Metallregalen selbst, an denen die Fachböden sowie die Wandverkleidungen und das Dach befestigt sind. Diese Art der Konstruktion nimmt also nur den geringst nötigen Platz ein, sodass die Lagerkapazität maximiert wird. Einer der Hauptvorteile ist die Reduzierung der Energiekosten, indem die Anlage auf einer konstant niedrigen Temperatur gehalten wird.
Reinräume und automatisierte Lager
Im Bereich der temperaturgeführten Logistik gewinnt die Automatisierung zunehmend an Bedeutung. Diese Lösung ermöglicht die maximale Nutzung der Lagerkapazität bei gleichzeitiger vollständiger Kontrolle über die Handhabungsbedingungen der Produkte. Förderer und Regalbediengeräte sorgen für eine fortlaufende und sichere Bewegung der Waren. All dies spart Zeit und minimiert die manuelle Handhabung der Produkte und die damit verbundenen Risiken.
Die gängigsten automatischen Lager- und Transportsysteme in Gefrier- oder Kühlkammern sind:
- Industrieförderer. Sie ersetzen herkömmliche Handhabungsgeräte und transportieren die Produkte automatisch. Förderer aus rostfreiem Stahl sind für diese Art von Kammern aufgrund ihrer hohen Korrosionsbeständigkeit besonders geeignet.
- Regalbediengeräte. In jedem Gang übernimmt ein Regalbediengerät den Transport der Waren von den Eingangspositionen im Lager bis zum entsprechenden Stellplatz. Die Regale können über eine einfache oder doppelte Tiefe verfügen.
- Pallet-Shuttle-System. Der Arbeitsablauf erfolgt vollkommen automatisch, da das System über ein motorisiertes Shuttle verfügt, das die Warenbewegungen ausführt. Es zählt zu den effizientesten Kompaktlagersystemen, da durch die Verwendung dieses Systems die Produktivität durch eine größere Anzahl von Zyklen erhöht wird.
- Hinsichtlich der Software trägt die Implementierung eines Lagerverwaltungssystems (LVS), beispielsweise Easy WMS von Mecalux, zur Steigerung der Produktivität eines automatischen Lagers bei. Die Software stellt das Gehirn der Anlage dar und steuert alle in einer Logistikanlage miteinander interagierenden Elemente, von den Handhabungsgeräten bis hin zu den Vorgängen zur effizienten Warenverwaltung.
Kontrolle, Reinheit und Sicherheit
Unternehmen beispielsweise in der Lebensmittel-, Pharma- oder Chemieindustrie sind verpflichtet, Reinräume zu nutzen, um ihre Produkte sicher zu verarbeiten oder zu handhaben. Diese Anlagen sind isoliert, um die Reinheit der Luft zu gewährleisten und das Eindringen von kontaminierenden Partikeln in diese Räume zu vermeiden, die die Qualität der Güter beeinträchtigen oder verschlechtern könnten.
Im Logistiksektor handelt es sich bei einer vollisolierten Anlage meistens um eine Kühl- oder Gefrierkammer. Hier werden Produkte gelagert, deren Temperatur kontrolliert werden muss, sodass eine Wärmeisolierung unerlässlich ist, um die Kälte im Inneren der Kammer zu halten.
Mecalux blickt auf eine langjährige Erfahrung in der Entwicklung dieser Art von Lagern für Unternehmen aus der Lebensmittel-, Chemie- oder Pharmaindustrie zurück, zum Beispiel:
- Bem Brasil. Dieser Hersteller von vorfrittierten Tiefkühl-Pommes-Frites hat seine Tiefkühlkammer (bei -30º C) mit dem automatischen Pallet-Shuttle-System ausgestattet, das eine Lagerkapazität von mehr als 33.000 Paletten bietet. Das Unternehmen entschied sich für dieses Kompaktlagersystem, da es sich hervorragend für Massenverbrauchsgüter mit einem großen Volumen an Paletten pro Artikelart eignet.
- Schaal Chocolatier. Dieses in Frankreichttps://www.mecalux.de/fallbeispiele/praxisbeispiel-intelligentes-lager-bem-brasilh führende Unternehmen in der Herstellung von Schokoladenpralinen verfügt über ein automatisches Lager, das aus fünf Gängen mit Regalen einfacher Tiefe besteht und eine Kapazität für 6.200 Paletten bietet. Von den fünf Gängen werden vier bei 14º C und der fünfte bei 5º C betrieben. Die Regale dienen zur Aufbewahrung von Fertigprodukten, Halbfertigprodukten, Rohstoffen, Verpackungen und den täglich benötigten Gebrauchsgegenständen.
- Takeda. Das Pharmaunternehmen Takeda hat ein automatisches Lager in Silobauweise mit einer Kapazität von 6.584 Paletten gebaut. Das Lager ist mit einem System zur Kontrolle von Lufttemperatur und Luftfeuchtigkeit ausgestattet, das die Temperatur zwischen 16° und 24º C hält und verhindert, dass die Luftfeuchtigkeit 70 % übersteigt.
Falls Sie überlegen, in Ihrem Lager einen Reinraum oder eine Lösung für die Automatisierung bei Kühltemperaturen zu bauen, nehmen Sie gerne Kontakt mit uns auf. Einer unserer Spezialisten wird Ihren Fall auf technischer Ebene analysieren und Ihnen helfen, die beste Lösung für Ihr Lager zu finden.