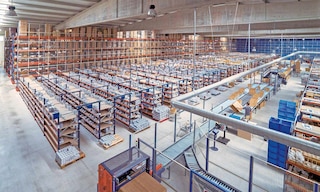
Wie man ein Lager organisiert und die Ressourcen optimiert
Die Organisation von Lagern ist entscheidend für eine gute Leistung der darin durchzuführenden Arbeiten.
Wie organisiert man ein Lager?
Das Wissen um die Organisation eines Lagers ist eine entscheidende Voraussetzung für den Erfolg von Unternehmen, die im Bereich der Logistik tätig sind. In einem geordneten Lager lassen sich die Unternehmensziele leichter erreichen, und es bringt Vorteile wie mehr Sicherheit und Flexibilität bei der Arbeit sowie eine Verringerung der Fehlerquote.
Der erste Schritt bei der Organisation einer zweckmäßigen Logistikanlage ist ihre Planung. Dieser Teil des Prozesses ist von entscheidender Bedeutung, denn eine schlechte Verteilung der Elemente kann einen effizienten Betrieb verhindern. Deshalb ist es sinnvoll, sich vor der Renovierung eines Lagers oder einer Neueinrichtung von Experten beraten zu lassen. Genauso wenig kann ein gutes Layout funktionieren, wenn das Personal nicht angemessen vorbereitet ist.
Zu Beginn der Lagerorganisation müssen Faktoren wie das Marktverhalten, die Geschäftsstrategie und das Vertriebsmodell des Unternehmens, die Lieferkette, die Produktion und Faktoren wie der verfügbare Platz und die finanziellen Mittel berücksichtigt werden.
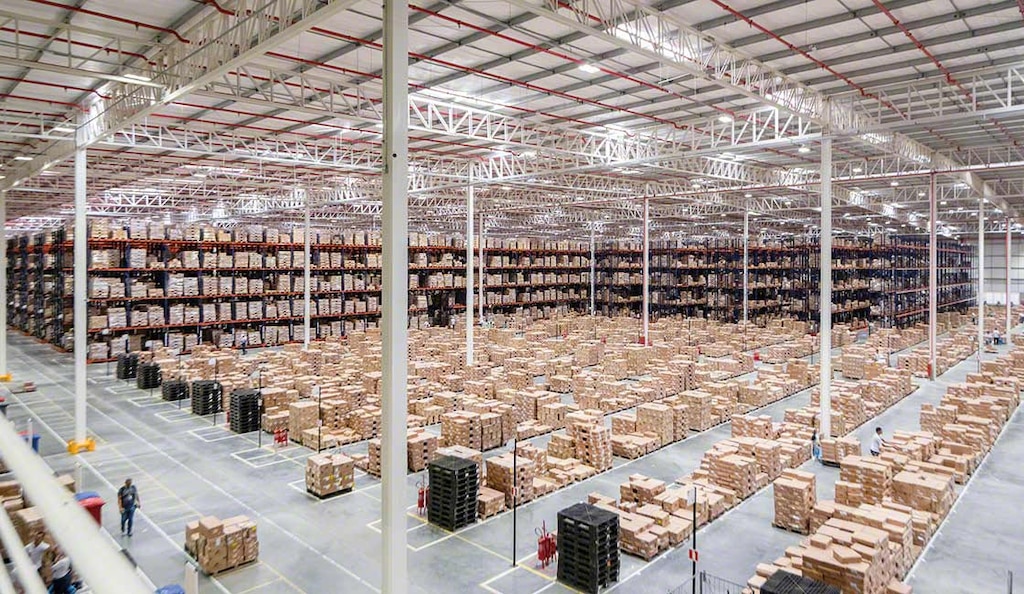
Wie lässt sich ein Lager besser organisieren?
Durch die Berücksichtigung des Layouts von Logistikanlagen und die Untersuchung der Organisation eines Logistiklagers wird der verfügbare Raum maximiert, bei allen Prozessen Zeit gespart und die Kosten gesenkt und optimiert, was den Unternehmen einen größeren Nutzen bringt.
- Die Wahl des richtigen Systems Es gibt drei Möglichkeiten, die Position der Ladeeinheiten nach einer zuvor erstellten Funktionsanalyse zu bestimmen. Bei einem festen oder statischen Stellplatz wird jedem Artikel im Voraus eine Position zugewiesen. Bei der zufälligen oder dynamischen Lagerung, auch chaotische Lagerung genannt, werden die Waren auf jeden verfügbaren freien Platz abgelegt. Beim gemischten oder halb zufälligen Stellplatz schließlich werden beide Systeme kombiniert.
- Optimale Nutzung des vertikalen Raums Da Lager nur begrenzten Raum bieten, ist die Ausnutzung der Höhe dieser Gebäude von entscheidender Bedeutung, damit sie optimal genutzt werden können. Daher empfiehlt es sich, manuelle Hochregale oder, wenn möglich, effizientere automatische Lagersysteme zu wählen.
- Anforderungen vorhersehen Abgesehen von der kurzfristigen Ausrichtung sollten Logistikverantwortliche versuchen, die Aktivitäten der Einrichtungen vorherzusehen, um den Ereignissen einen Schritt voraus zu sein.
- Berücksichtigung des Umschlags Wenn man weiß, welche Bestände zu einem bestimmten Zeitpunkt am meisten nachgefragt werden, kann man das Lager nach dem Produktumschlag organisieren. So kann man eine große Anzahl von Sendungen abwickeln, indem man die am meisten nachgefragten Produkte in eine bevorzugte Position bringt.
- Verwendung des Cross-Docking Wenn die eingehenden Waren ohne Umweg über die Regale direkt in den Kommissionierbereich gelangen, werden Zeit und Lagerarbeit eingespart, die Lieferzeiten verkürzt und die Kosten gesenkt.
Was geschieht, wenn ein Lager ungeordnet ist?
Wenn man nicht auf die Verwaltung eines Lagers achtet, erschwert das den täglichen Betrieb und kann sich negativ auf die Leistung und den Ruf eines Unternehmens auswirken. Dies sind einige der häufigsten Folgen:
- Die Produkte werden nicht gefunden. Wenn das Personal die Stellplätze nicht genau kennt und die Anlagen nicht aufgeräumt sind, wird das Auffinden von Referenzen schwierig, was alle Prozesse verlangsamt und sogar zu einem Bestandsschwund führen kann.
- Überschuss oder Mangel an Bestand. Ohne eine geordnete Lagerung können sich zusätzliche Artikel ansammeln, ohne dass man es merkt, was zu einem Überbestand führt. Es kann aber auch der Eindruck entstehen, dass man einige Artikel auf Lager hat, die in Wirklichkeit nicht vorrätig sind, d. h. es kommt zu Fehlbeständen.
- Es wird mehr Platz benötigt. Wenn die Produkte ungeordnet platziert und die Gänge nicht beachtet werden, kann man leicht den Eindruck gewinnen, dass es an Platz mangelt. Eine gute Flächennutzung steigert jedoch die Effizienz von Unternehmen erheblich. Die Berücksichtigung dieser bewährten Verfahren ist besonders wichtig, wenn die Organisation eines kleinen Lagers geplant ist.
Wie hält man ein Lager sauber und aufgeräumt?
Lager mit sauberen und geordneten Arbeitsbereichen sparen Zeit und Mühe, was die Produktivität und Sicherheit erhöht. Eines der Systeme japanischen Ursprungs, das häufig zur Gewährleistung der Sauberkeit eingesetzt wird, ist die 5er-Methode. Dies sind ihre Schritte:
- Klassifizierung (Seiri): Dabei wird alles Unnötige entfernt, um so Lagerplatz freizugeben.
- Ordnung (Seiton): Es geht darum, das Lager mit den notwendigen Mitteln auszustatten, um Produkte strategisch zu orten und sie schnell zu finden.
- Reinigung (Seiso): Damit soll ermittelt werden, wie oft verschiedene Wartungs- und Hygienemaßnahmen im Arbeitsbereich durchgeführt werden.
- Visuelle Kontrolle (Seiketsu): Die ordnungsgemäße Kennzeichnung begrenzt Sortierfehler und erleichtert die Aufrechterhaltung der Ordnung.
- Selbstdisziplin (Shitsuke): Reinigungsroutinen sollten zur Gewohnheit werden und eine übermäßige Ansammlung von Schmutz vermeiden.
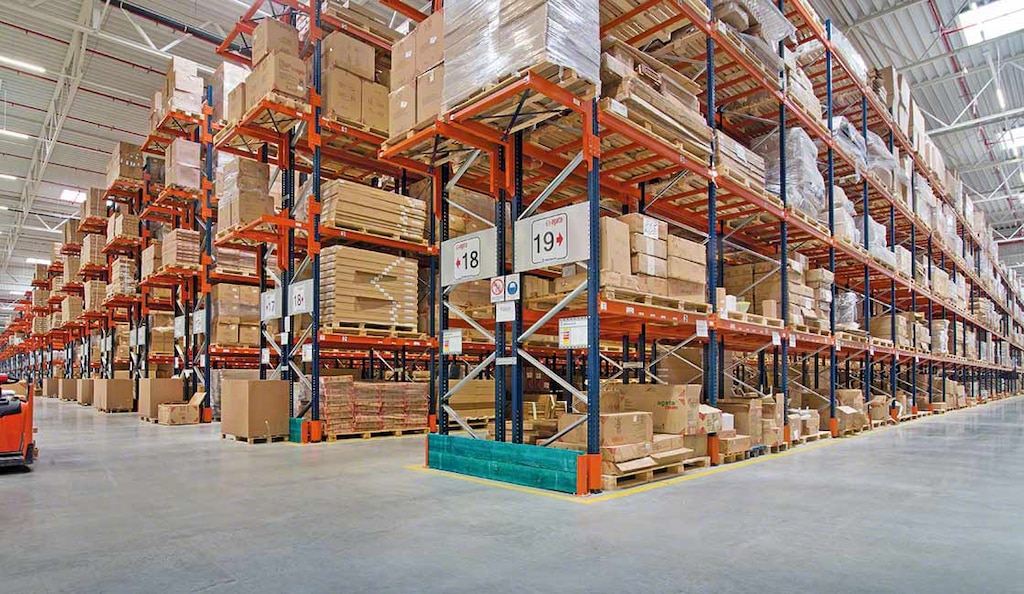
Was sind die Schritte, um ein Lager richtig zu organisieren?
Dies sind einige der häufigsten Probleme in Logistikanlagen und die Lösungen, die zu ihrer Überwindung eingesetzt werden können:
Problem | Lösung |
---|---|
Lange Strecken | Durch die Anwendung der ABC-Methode für die Organisation des Lagerbestands können die sich besonders schnell bewegenden Waren näher an den Versandbereichen platziert werden. |
Unterbrechungen | Durch die ordnungsgemäße Kennzeichnung der Durchgangsstellen und der Fahrtrichtung von Personen oder Maschinen wird sichergestellt, dass die Arbeit bestimmter Kollegen nicht die anderer Kollegen beeinträchtigt. |
Manuelles Zählen | Wenn man einen genauen Überblick über die Waren in seinem Lager behalten und Zeit sparen möchte, ist die Einrichtung eines RFID-Etikettierungssystems äußerst sinnvoll. |
Kumulierte Retouren | Die Bereitstellung von Lagerflächen für die reverse Logistik wird oft vernachlässigt, so dass sich die Retouren stapeln und das Lager überfüllen. Durch die Planung von Anlagen von Anfang an oder durch Nachrüstung kann dieses Problem gelöst werden. |
Schmutz | Wenn man sich im Alltag Zeit nimmt, um das Lager in gutem Zustand zu halten, werden Risiken vermieden, die Sicherheit erhöht und die Arbeitsumgebung angenehmer gestaltet. |
Beispiele für die Organisation von Lagerregalen
Zwar können Unternehmen durch Automatisierung einen Schritt weiter gehen, aber folgende Unternehmen haben mit manuellen Regalanlagen hocheffiziente Lager erreicht:
- Leroy Merlin Das französische Unternehmen für Heimwerkerbedarf, Heimdekoration und Gartengestaltung hat seine Geschäftsstrategie mit der Eröffnung neuer städtischer Geschäfte in spanischen Städten wie Madrid und Barcelona neu ausgerichtet und gleichzeitig den Online-Vertrieb gestärkt. Um diese Projekte in Angriff zu nehmen, hat das Unternehmen seine beiden Lager in Torija (Spanien) mit herkömmlichen Palettenregalen ausgestattet. Sie haben eine Höhe von 10,5 Metern und bieten eine Lagerkapazität von mehr als 21.600 Paletten und passen sich jeder Artikelart an – unabhängig von deren Gewicht und Volumen.
- SMU Das Logistikzentrum der chilenischen Supermarktkette in Pudahuel, in der Nähe von Santiago, ist 70.000 m² groß und kann rund 47.000 Paletten aufnehmen. Dieses wichtige Einzelhandelsunternehmen in Chile verfügt über einen langen Kreislauf von Fördersystemen und Regalen mit einem unteren Teil für die Kommissionierung. Bei diesen kamen verstärkte Ständer zum Einsatz, die für mehr Sicherheit sorgen. Sie minimieren die Folgen eines möglichen Erdbebens so weit wie möglich, da sich das Lager in einem Gebiet mit hoher seismischer Aktivität befindet.
- Radec Der mexikanische Importeur und Händler für Kfz-Ersatzteile Radec ist in den letzten Jahren stark gewachsen und verfügt über Standorte in Villahermosa, Tijuana, Monterrey und Guadalajara. Diese Expansion führte jedoch zu einem Platzmangel in ihren Anlagen. Nach einer Beratung durch Mecalux setzt das Unternehmen an seinem Hauptsitz in Guadalajara Paletten- und Regale mit Pick-Tower ein, um bis zu 1.800 Aufträge pro Tag zusammenzustellen.
Organisieren Sie Ihr Lager mit Mecalux
Wir bei Mecalux fördern den Betrieb aller Arten von Lagern mit Lagersystemen oder mit automatisierten Anlagen und Verwaltungsprogrammen. Wir arbeiten zudem Hand in Hand mit unseren Kunden, um das Lagerverwaltungssystem auf ihre spezifischen Geschäftsanforderungen abzustimmen. Wenn Sie Ihre Lieferkette stärken wollen, wenden Sie sich an uns, damit wir Ihnen bei der Optimierung Ihrer Logistik helfen können.