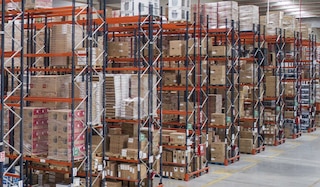
Die 10 häufigsten Logistikprobleme im Lager
Aufgrund der kontinuierlichen Entwicklung in Richtung digitaler Märkte und der neuen Kundenanforderungen haben die Logistikprobleme, insbesondere im Zusammenhang mit der Lagerverwaltung, erheblich zugenommen.
Was sind aber die häufigsten Logistikprobleme? In diesem Beitrag werden die zehn häufigsten Probleme, die in einem Lager auftreten können, vorgestellt und einige Lösungen zur Minimierung ihrer Folgen vorgeschlagen.
1. Ungenutzter Raum
Zu wenig Lagerfläche ist eines der Hauptprobleme, das die meisten Unternehmen betrifft. Diese Situation wird vor allem durch die Ausweitung der Unternehmensaktivität hervorgerufen. Unternehmen müssen daher ihre Lagerflächen optimieren, wenn sie nicht erhebliche Investitionen für neue Logistikflächen tätigen wollen.
Eine der häufigsten Lösungen zur Optimierung der Lagerkapazität, ohne die Lagerfläche zu erweitern, ist die Ausnutzung der Höhe des Lagers durch höhere Regale oder Bühnen und Laufgänge. Darüber hinaus kann die Lagerfläche durch die Montage von Kompaktlagersystemen wie dem Pallet-Shuttle-System, Movirack-Verschieberegalen oder Einfahr- bzw. Durchfahrregalen optimiert werden.
2. Mangelhafte Organisation der Waren
Aufgrund einer schlechten Organisation der Ware kommt es zu Fehlern und Verzögerungen bei der Suche nach einem bestimmten Produkt, wodurch es schwierig wird, Lieferzeiten einzuhalten. Ein geordnetes Lager ist der erste Schritt zu logistischer Effizienz.
Um Fehler durch mangelhafte Organisation zu vermeiden, ist es erforderlich, eine effiziente Strategie für die Einlagerung der Waren zu entwickeln, die die Eigenschaften der Artikelarten, die verfügbaren Lagersysteme, den Umschlag der Waren und die Bewegungen der Bediener berücksichtigt.
Die Verwendung eines Lagerverwaltungssystems gewährleistet die volle Kontrolle über den Bestand im Lager durch die Synchronisierung der Eingangs- und Ausgangsaufträge. So automatisiert ein LVS beispielsweise den Einlagerungsprozess von Artikelarten im Lager (Slotting) anhand vorkonfigurierter Kriterien und Regeln.
3. Fehler bei der Kommissionierung
Von der Kommissionierung des falschen Artikels bis hin zum Vermischen mehrerer Aufträge haben die Kosten der reversen Logistik, also der Rücksendung von Artikeln aufgrund von Kommissionierungsfehlern, schwerwiegende Folgen für die Logistik eines Unternehmens.
Fehler bei der Kommissionierung sind für das Unternehmen kostspielig. Einigen Studien zufolge wird ihr durchschnittlicher Anteil auf etwa 17 Euro pro Auftrag geschätzt.
Bei einem so komplexen Vorgang wie der Auftragszusammenstellung, bei der die Bediener in der Regel mehrere Aufträge mit verschiedenen Artikelarten gleichzeitig zusammenstellen, ist die Automatisierung die beste Lösung, um die Fehlerquote zu senken und die Anzahl der im Lager durchgeführten Picks pro Stunde zu erhöhen.
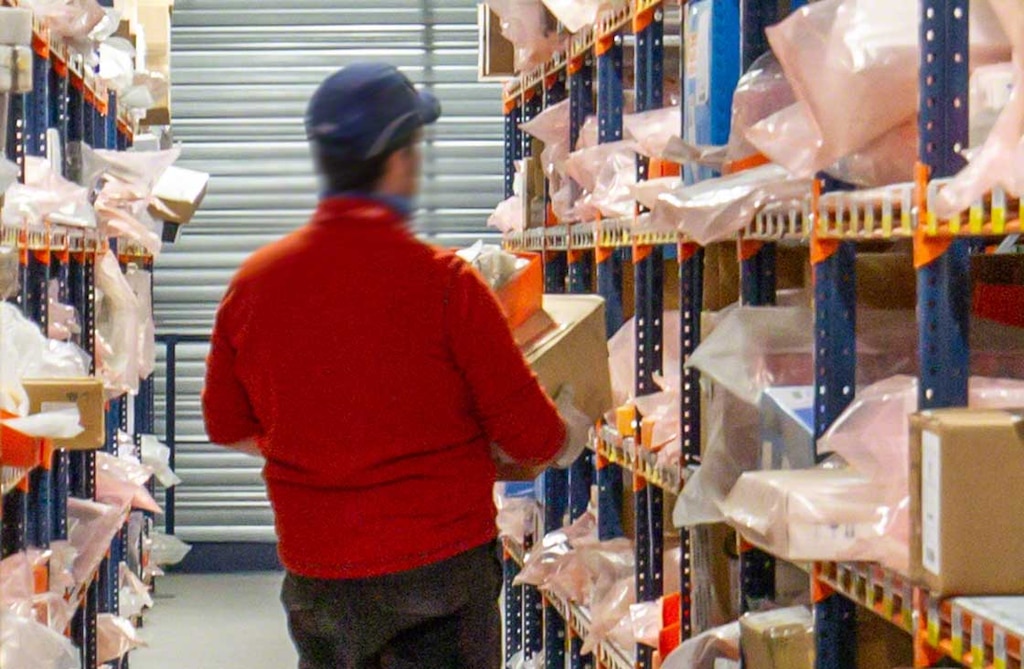
4. Fehlende Rückverfolgbarkeit
Im Rahmen einer integrierten Lieferkette fordern Kunden und Lieferanten, genau zu wissen, aus welchen Rohstoffen ein Artikel hergestellt wird und welche Produktions- und logistischen Abläufe er durchlaufen hat, bis sie ihn in den Händen halten.
Die Rückverfolgbarkeit von Produkten ermöglicht es, jedes Produkt von seinem Ursprung bis zum endgültigen Bestimmungsort zu erfassen und zu identifizieren, und ist besonders in Sektoren wie der Pharma- oder der Lebensmittelindustrie erforderlich. Ein Fehler bei der Rückverfolgbarkeit kann sowohl für Kunden, die das Produkt kaufen, als auch für den Hersteller ernsthafte Probleme mit sich bringen.
Die Implementierung einer Logistiksoftware wie einem LVS garantiert die Rückverfolgbarkeit des Produkts von seinem Eingang im Lager bis zum Versand. Neben dieser Anwendung gibt es auch andere Softwareprodukte auf dem Markt, die die Rückverfolgbarkeit optimieren, z. B. die erweiterte Funktionalität von Easy WMS, das LVS für die Produktion. Dieses Modul synchronisiert den Versorgungspuffer mit dem Produktionspuffer, um den Produktionsprozess im Lager zu überwachen.
5. Veralteter Bestand
Um die Produktivität aller logistischen Vorgängen aufrecht zu erhalten, ist es unerlässlich den Bestand eines Lagers zu kennen und zu planen. Ein Lager mit einem veralteten Bestand kann für ein Unternehmen schwerwiegende Folgen haben, von Fehlern bei der Einlagerung von Produkten bis hin zu möglichen Out-of-Stock-Situationen.
Mit zunehmendem Wachstum eines Unternehmens und der Aufnahme weiterer Artikelarten in das Lager ist die Implementierung eines Lagerverwaltungssystems ein notwendiger Schritt, um jederzeit den verfügbaren Bestand des Lagers abzufragen.
6. Fehler bei der Warenhandhabung
Ein Schlüssel zur Fehlerreduzierung und Produktivitätssteigerung ist die korrekte Handhabung von Ladeeinheiten bei der Auftragsabwicklung. Es muss sichergestellt werden, dass die Bediener entsprechend geschult sind, dass das Lager über angemessene Handhabungsgeräte verfügt und dass diese ordnungsgemäß gewartet werden.
Am besten lässt sich die optimale Handhabung der Waren jedoch durch die Automatisierung der Lagersysteme gewährleisten. Immer häufiger entscheiden sich Logistikleiter für den Ersatz konventioneller Handhabungsgeräte wie Palettenhubwagen und Gegengewichtsstapler durch Fördervorrichtungen und Regalbediengeräte, um den Warentransport zwischen den verschiedenen Logistikprozessen zu beschleunigen.
Darüber hinaus ist es bei der Handhabung der Waren wichtig, die Stabilität der Ladeeinheiten, in der Regel Paletten oder Behälter, sicherzustellen, um gleichzeitig die Stabilität des gesamten Packstücks während aller im Lager durchgeführten Vorgänge zu gewährleisten.
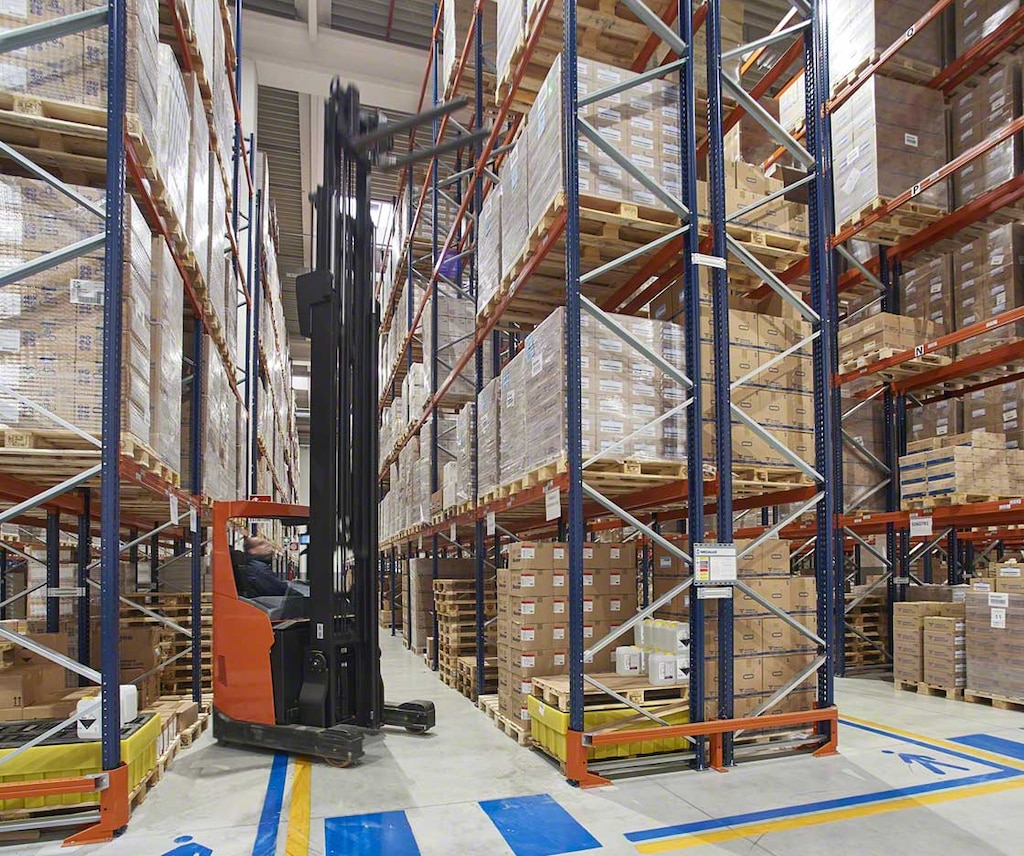
7. Verzögerungen beim Versand
Der Versand ist der letzte Prozess, den ein Produkt durchläuft, bevor es entweder an den Endkunden oder an ein anderes Vertriebs- oder Produktionszentrum ausgeliefert wird.
Damit dieser Prozess erfolgreich durchgeführt werden kann, ist es ratsam, die Planung der abzuwickelnden Lieferungen, die effiziente Konsolidierung der Waren, die korrekte Prüfung aller für den Transport erforderlichen Dokumente sowie eine schnelle und sichere Verladung der Waren in den LKW sicherzustellen.
Ein Lagerverwaltungssystem ermöglicht die Gruppierung von Aufträgen u. a. nach Versandroute, Fahrzeugtyp, Kunde oder Transportpriorität.
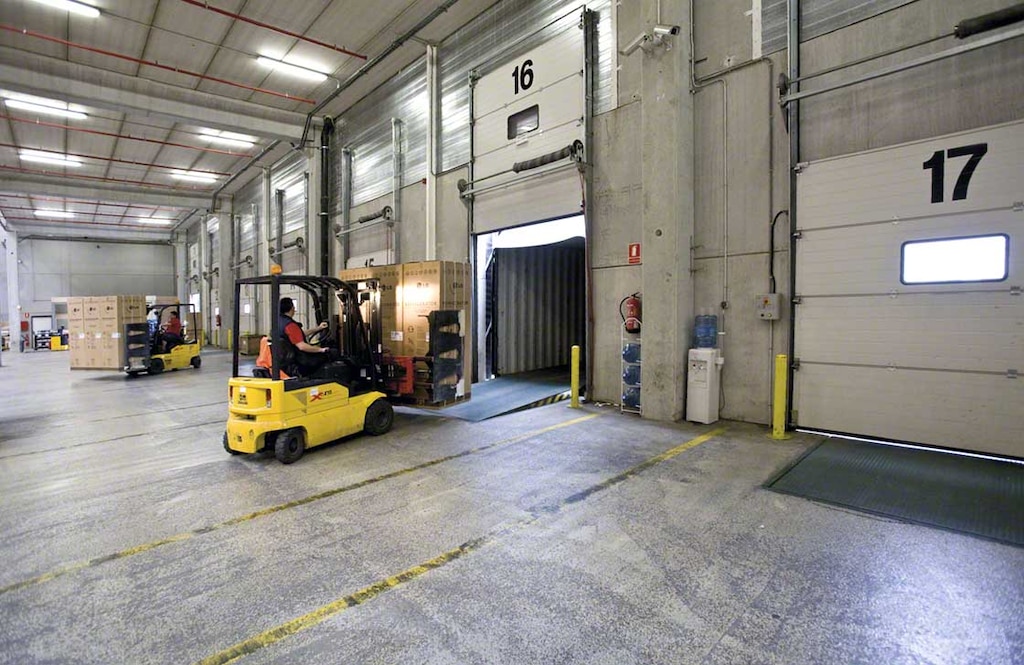
8. Fehlerhafte Kennzeichnung des Lagers
In einem Raum, in dem Arbeiter, Waren und Umschlaggeräte gleichzeitig vorhanden sind, ist es unerlässlich, die Kennzeichnung des Lagers so zu gestalten, dass das Unfallrisiko möglichst gering ist. Die Kennzeichnungen müssen auf dem Boden und in den Regalen perfekt positioniert und optisch voneinander zu unterscheiden sein, damit sie den Sicherheitsmaßnahmen entsprechen.
Die Richtlinie 92/58/EWG des Europäischen Rates, die die Kennzeichnung des Lagers vorschreibt und regelt, legt fest, wie die Beschilderung in einem Lager auszusehen hat. Die Schilder können je nach ihren Merkmalen und der Botschaft, die sie vermitteln sollen, unterschiedliche Farben, Symbole und Formen aufweisen.
9. Fehlerhafte logistische KPIs
Das beste Hilfsmittel zur Durchführung kontinuierlicher Verbesserungsmaßnahmen in einem Lager sind Leistungsindikatoren, Logistikkennzahlen oder logistische KPIs (Key Performance Indicators) genannt. Durch die Erfassung von Daten und den Vergleich mit dem bisherigen Verlauf kann die Leistung eines Vorgangs überwacht werden und es können Verbesserungsmöglichkeiten ermittelt werden.
Anhand von logistischen KPIs lassen sich alle in einem Lager durchgeführten Vorgänge messen: u. a. Wareneingang, Lagerung, Auftragszusammenstellung, Bestandsverwaltung, Versand, Lieferung, Transport und Retourenmanagement. Werden diese Indikatoren jedoch nicht korrekt verwendet oder falsche KPIs analysiert, ist es äußerst schwierig, positive oder negative Entwicklungen zu erkennen und entsprechend zu handeln, um die Logistik zu optimieren.
Ein Modul wie die Software Supply Chain Analytics überwacht alle Vorgänge, die im Lager stattfinden, und berechnet die wichtigsten KPIs für die anschließende Analyse.
10. Integration mit anderen Abteilungen (ERP)
Der Lagerleiter muss sich mit anderen Abteilungen des Unternehmens abstimmen, um das Ziel der gesamten Logistik zu erreichen: dass die Bestellung in der mit dem Kunden vereinbarten Zeit und auf die vereinbarte Art und Weise eintrifft.
Zu diesem Zweck werden die verschiedenen Logistik-Softwareprogramme in das ERP-System (Enterprise Resourcing Planning System) integriert, ein Computerprogramm, das alle bzw. fast alle Abteilungen eines Unternehmens, wie Buchhaltung, Marketing, Verkaufsabteilung usw., zusammenfasst.
Eine schlechte Koordination zwischen dem Lager und der Verkaufsabteilung kann zu Fehlern bei Bestellungen oder unvollständigen Bestellungen führen, was schwerwiegende wirtschaftliche Folgen für das Unternehmen haben kann.
Profitieren Sie von einem effizienteren Lager
Grundsätzlich ist die Automatisierung, sowohl der Vorgänge als auch der Verwaltung eines Lagers, mithilfe eines LVS die beste Strategie für ein fehlerfreies und wesentlich effizienteres Lager.
Ist Ihnen in Ihrem Lager eines der oben genannten Probleme aufgefallen oder möchten Sie sowohl die Lagerung als auch die Verwaltung Ihres Distributionszentrums automatisieren, dann kontaktieren Sie Mecalux. Einer unserer Experten wird Sie dabei unterstützen, Lösungen für mögliche Probleme zu erarbeiten, um das Beste aus Ihren Logistikprozessen herauszuholen.