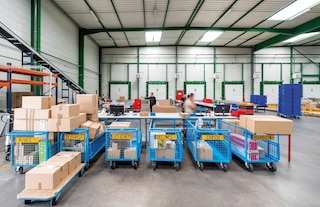
Maßnahmen zur Lageroptimierung - ein Leitfaden
Eine Maxime in der Logistik lautet: "Der beste Weg, um Zeit zu sparen, ist, sie nicht zu verschwenden". Denn Zeit ist Geld - das gilt heutzutage mehr denn je. Damit wird deutlich, wie wichtig eine Lageroptimierung ist. In unserem Artikel werden wir Schritt für Schritt zeigen, mit welchen Maßnahmen Ihr Lager effizienter wird.
1. Detaillierte Analyse der Aufgaben
Ausgangspunkt für eine Lageroptimierung ist die Analyse des Ist-Zustandes: Welche Art von Aufgaben werden ausgeführt? Wie viel Zeit wird für jede Aufgabe aufgewendet? Diese Phase umfasst die folgenden Schritte:
- Identifizieren der Aufgaben
- Administrative Aufgaben: Erstellung von Berichten, Organisation von Lieferscheinen, Arbeitsauftrag (falls nicht automatisch), Qualitätskontrolle, interne Meetings etc.,
- Warentransport: zwischen den verschiedenen Zonen des Lagers (horizontale und vertikale Wege - bei Arbeiten mit Lasten in der Höhe),
- Leerfahrten ohne Ladung,
- Be- und Entladen von Frachtwagen.
Die Vorbereitung von Aufträgen ist besonders hervorzuheben, da sie eine der kostenintensivsten Aktivitäten auf operativer Ebene ist. Daher müssen die mit jeder Kommissionierphase verbundenen Aufgaben im Detail analysiert werden.
- Berechnung der aufgewendeten Zeit pro Aufgabe
Die Aufgaben werden nun in einem zweiten Schritt klassifiziert und quantifiziert, indem die Häufigkeit der Durchführungen pro Aufgabe und die Zeit pro Durchführung sowie die Gesamtzeit notiert werden. So entsteht eine Übersicht sämtlicher Prozesse, die Teil einer Aufgabe sein können. Die Beladung eines LKW beispielsweise umfasst fünf verschiedene Abläufe: Verwaltungsaufgaben, Bewegen der Handhabungsgeräte ohne Last, Aufnehmen der Palette, Bewegen mit der Last und Positionieren der Last auf dem LKW.
- Analyse der Ergebnisse, um Maßnahmen festzulegen
Mit den gewonnenen Informationen ist es anschließend möglich:
- unnötige oder doppelte Aufgaben zu lokalisieren und zu eliminieren.
- Routen besser zu planen und zu optimieren. Eine entscheidende Rolle spielt dabei ein LVS wie Easy WMS.
- das Layout des Lagers auf Schwachstellen zu prüfen und gegebenenfalls eine Umgestaltung vorzunehmen.
2. Analyse der Produktivität der Handhabungsgeräte
Handhabungsgeräte haben einen direkten Einfluss auf die Organisation der Logistikprozesse im Lager. Sie sollten daher gesondert analysiert werden:
- Protokollieren Sie die aktuelle Leistung aller verwendeten Geräte: welche Geschwindigkeit und Höhe sie erreichen, die Reichweite der Batterien, die Häufigkeit der Ladungen, welche Gangbreite sie benötigen usw.
- Messen Sie deren Auswirkungen auf den Materialfluss: Wenn die Aktivitäten im Lager zunehmen, wird schnell ein Punkt erreicht, bei dem sich der Transport von Lasten nicht mehr vervielfachen lässt, ohne Ineffizienzen zu erzeugen.
Anhand dieser Informationen lässt sich abschätzen, welche Prozesse im Lager mit welchen Systemen automatisiert werden können. So kann beispielsweise der Effizienzverlust durch einen voll ausgelasteten Verkehr einer der Gründe für ein Automatisierungsprojekt sein, wie es beim spanischen Logistikdienstleister Disalfarm der Fall war.
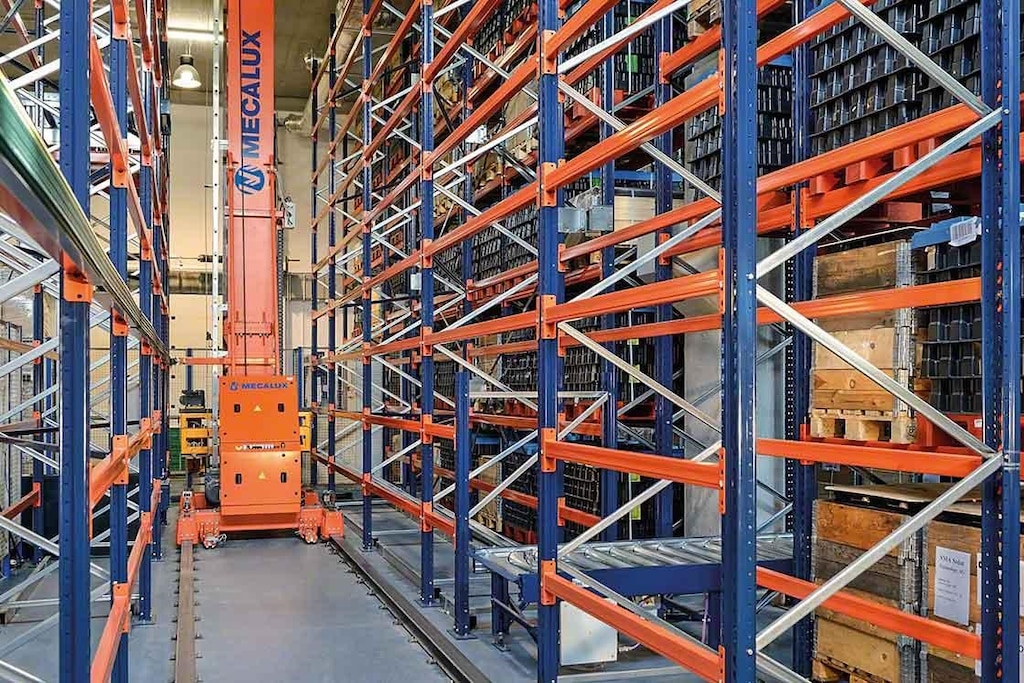
3. Bewertung des Lagerbestands
Einer der Bereiche der Lagerlogistik mit dem größten Verbesserungspotenzial ist die Bestandsverwaltung. Folgende Maßnahmen können Sie durchführen:
- Identifizieren Sie durch Lagerbewegungen aufgezeichnete Trends, um Saisonalität zu erkennen und zu überprüfen, ob die Verteilung nach dem ABC-Prinzip korrekt im Lager implementiert ist und ob die Lagersysteme ausreichend sind.
- Überprüfen Sie die logistischen Parameter, die bei der Zuordnung von Lagerplätzen berücksichtigt werden, insbesondere wenn diese variabel sind, wie im Falle der chaotischen (oder dynamischen) Lagerhaltung.
- Untersuchen Sie sorgfältig Prozesse, die zu Fehlern bei der Rückverfolgbarkeit führen können. Zum Beispiel: Wie werden Waren, die einer Qualitätskontrolle unterzogen werden, klassifiziert? Bereinigen und optimieren Sie auch Ihren Lagerbestand durch das Entfernen von Ladenhütern.
4. Einbeziehung der Mitarbeiter
Ein weiterer Schwerpunkt im Rahmen der Lageroptimierung liegt bei den Mitarbeitern. Es ist wichtig, sie in den Prozess einzubeziehen, beispielsweise durch folgende Maßnahmen:
- Ermittlung des Schulungsbedarfs: Neue Fähigkeiten können zu einer Verbesserung der Teamproduktivität führen.
- Analyse der Arbeitsplätze unter dem Gesichtspunkt der Ergonomie und des Arbeitsschutzes.
- Gemeinsame Gespräche, um Probleme zu erkennen, mit denen die Mitarbeiter täglich konfrontiert sind und um zu erfahren, wie ihre Arbeit dadurch beeinträchtigt wird.
Kurz gesagt, Lageroptimierung bedeutet Kosteneinsparung und Verbesserung der Servicequalität. Nach einer eingehenden Prüfung des Ist-Zustandes des Lagers können entsprechende Maßnahmen zur Verbesserung der Gesamtleistung ergriffen werden. Kontaktieren Sie uns und einer unserer erfahrenen Experten wird Sie dabei begleiten!