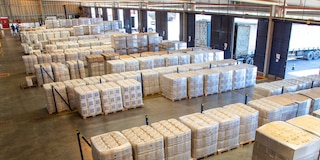
Wie wird der optimale Bestand für ein Lager berechnet?
Der Schlüssel zu einer effizienten Logistik und zur Vermeidung von Mehrkosten bei der Einlagerung liegt in einem optimalen Lagerbestand. Wie hoch ist jedoch die erforderliche Anzahl an Beständen, um die Nachfrage nach einem Produkt angemessen decken zu können, ohne dass es zu Out-of-Stock-Situationen kommt?
In diesem Artikel wird erläutert, was der optimale Lagerbestand ist und welche Unterschiede es zwischen diesem Konzept und dem Mindest- und Sicherheitsbestand gibt. Dabei wird näher auf die Formel eingegangen, um den Lagerbestand entsprechend der Nachfrage, der jeweiligen Anlage und dem progressiven Wachstum des Unternehmens zu bestimmen.
Was ist der optimale Lagerbestand und wie wird er angewandt?
Das logistische Konzept des optimalen Lagerbestands definiert die genaue Bestandsmenge, die ein Unternehmen benötigt, um einer regelmäßigen Nachfrage ohne Out-of-Stock-Situationen nachzukommen. Es geht also darum, die maximale Rentabilität zu erzielen und gleichzeitig die Lagerhaltungskosten zu senken.
Dieses Konzept darf nicht mit dem des Durchschnittsbestands verwechselt werden, der, wie der Name bereits sagt, den durchschnittlichen Bestand im Lager darstellt. Der optimale Lagerbestand liegt zwischen dem Maximalbestand, d. h. der Gesamtzahl der Artikel, die in der Anlage unter Berücksichtigung der Fläche und der Lagersysteme gelagert werden können, und dem Meldebestand oder dem Mindestbestand, d. h. der Mindestgrenze, ab der ein Unternehmen ein Produkt nachbestellen muss.
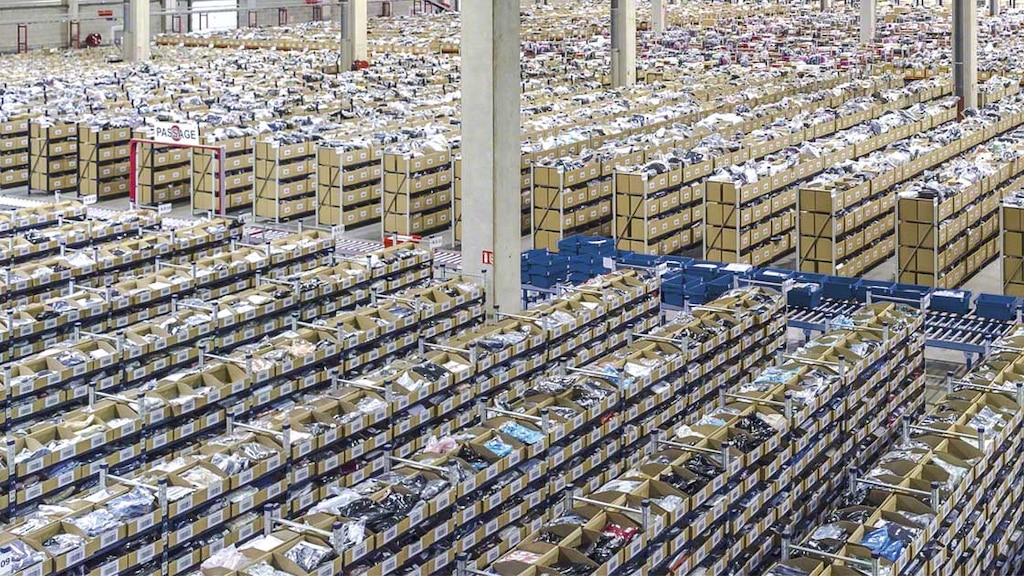
Wie wird der optimale Lagerbestand ermittelt?
Auf welche Faktoren muss der Logistikleiter achten, um den optimalen Lagerbestand zu bestimmen? Diese Faktoren sind zwar von der Strategie des jeweiligen Unternehmens abhängig, jedoch sind dies die vier wichtigsten Aspekte, die zu berücksichtigen sind:
- Nachfrage der Kunden: Der Logistikleiter muss zusammen mit der Buchhaltungs- und Verwaltungsabteilung die Entwicklung der Nachfrage während der letzten Jahre, die Prognose dieser Nachfrage für jede Artikelart, ihre Saisonabhängigkeit für jedes Produkt usw. auswerten.
- Lagerumschlag: Der Logistikleiter muss darüber hinaus den Umschlag der einzelnen Artikelarten kennen, damit er die Stellplätze der Waren korrekt verwalten kann. Die ABC-Klassifizierung ist eine gängige Methode, um Bestände entsprechend der Nachfrage zu organisieren.
- Art des Produkts. Die Merkmale der einzelnen Produkte und der Branche, in der das Unternehmen tätig ist, sind von grundlegender Bedeutung für die Bestimmung des optimalen Lagerbestands entsprechend den vorhandenen Lagersystemen. Zum Beispiel kann die Logistik in der Lebensmittelindustrie, in der bei der Lagerung Kälte benötigt wird, um die Qualität der Waren zu gewährleisten, nicht mit der Lagerung von Kabeln oder Rohren verglichen werden, bei der spezifische Lagersysteme erforderlich sind, die an die Besonderheiten der Produkte angepasst sind.
- Maximalbestand, Mindestbestand und Sicherheitsbestand. Aus diesen drei Werten kann der optimale Bestand für jede SKU berechnet werden. Der maximale Bestand wird anhand der Fläche, der Lagersysteme und der Handhabungsgeräte bestimmt, während der Mindestbestand durch die Nachfrage und die Kapazität zur Verwaltung der einzelnen Aufträge festgelegt wird. Die Eigenschaften des Unternehmens definieren andererseits den Sicherheitsbestand, der in jeder Anlage erforderlich ist.
- Lead time. Der Lagerleiter muss darüber hinaus die Lead Time der einzelnen Lieferanten kennen. Diese umfasst die Wartezeit zwischen der Generierung eines Eingangsauftrags für das Lager und der Auslieferung des Produkts durch den Lieferanten.
Da in der Logistik Effizienz und die Senkung der Lagerhaltungskosten immer wichtiger werden, kann ein fehlender optimaler Lagerbestand ernsthafte Folgen für das Unternehmen haben, wie ineffiziente Abläufe bei der Einlagerung, kostspieliger Überbestand oder die Beeinträchtigung der Qualität des Bestands, insbesondere, wenn dieser verderblich ist.
Optimaler Bestand, Mindest- und Sicherheitsbestand: Welche Bestandsarten gibt es?
Um das Konzept des optimalen Lagerbestands zu verstehen, müssen zunächst andere Konzepte wie operativer Bestand, Sicherheitsbestand oder Meldebestand bekannt sein. Dann betrachten wir die verschiedenen Bestandsarten entsprechend der Logistikstrategie:
- Verfügbarer Bestand: Hierbei handelt es sich um die Bestandsmenge im Lager, die für einen Auftrag zur Verfügung steht. Mit dem verfügbaren Bestand, der auch als operativer Bestand bezeichnet wird, werden alle logistischen Prozesse ausgeführt.
- Mindestbestand: Der Mindestbestand ist die Mindestmenge eines jeden Produkts, über die das Lager verfügen muss, um die Nachfrage nach einem Produkt zu decken.
- Sicherheitsbestand: Jede Anlage muss über einen Sicherheitsbestand verfügen, damit es bei einem unerwarteten Anstieg der Nachfrage nicht zu einer Out-of-Stock-Situation kommt.
- Meldebestand: Der Meldebestand ist ein in der Logistikstrategie festgelegter Wert, der angibt, wann ein Produkt beim Lieferant bestellt werden soll. Er liegt zwischen dem Mindestbestand und dem optimalen Bestand.
- Maximalbestand: Hierbei handelt es sich um die Anzahl der Bestände, die nie überschritten werden darf, um den Betrieb der Anlage zu gewährleisten. Er hängt mit der Lagerkapazität der Anlage und den im Unternehmen verfügbaren Arbeitskräften zusammen.
Sobald diese Konzepte klar sind, kann der optimale Lagerbestand berechnet werden, d. h. die Anzahl der Bestände, die vorhanden sein muss, damit das Unternehmen eine maximale Rentabilität erzielen und gleichzeitig auf die bestehende Nachfrage und eventuelle Schwankungen reagieren kann.
Die Formel für einen optimalen Bestand
Wenn der Logistikleiter die zuvor genannten Aspekte berücksichtigt hat, muss er anhand der Formel zur Berechnung des optimalen Bestands die Menge jedes Artikels ermitteln, die sich im Lager befinden sollte. Dies geschieht ausgehend von der optimalen Bestellmenge, zu der der Mindestbestand und der Sicherheitsbestand, der sich im Lager befinden sollte, hinzugerechnet werden müssen. Nachstehend wird erläutert, wie diese Variablen ermittelt werden.
Die optimale Bestellmenge wird mit dem Wilson-Modell bestimmt, bei dem auf Grundlage der Menge und Häufigkeit, mit der Bestellungen bei Lieferanten aufgegeben werden, eine optimale Bestandsverwaltung und Rohstoffbeschaffung erreicht werden soll. Um diesen Wert zu berechnen, wird folgende Formel verwendet:

Q ist dabei die optimale Bestellmenge, D ist der jährliche Bedarf an dem entsprechenden Rohstoff, K sind die Kosten für jede Bestellung und G sind die Kosten für die Lagerung eines Produkts für eine bestimmte Zeit. Dank des Wilson-Modells kann der Lagerleiter also ableiten, wann er eine neue Bestellung aufgeben muss.
Neben der optimalen Bestellmenge ist es auch erforderlich, den Mindestbestand eines Lagers und den Sicherheitsbestand zu bestimmen. Um den Mindestbestand eines Lagers zu ermitteln, lautet die Formel wie folgt:

Zu dieser Formel muss der Sicherheitsbestand hinzugefügt werden, der anhand der folgenden Variablen berechnet wird:
- Lead time der Lieferanten unter normalen Umständen (LTL).
- Maximale Lieferzeit im Falle von Schwierigkeiten (MLS)
- Durchschnittliche Produktnachfrage (DPN).

Die Formel für den optimalen Bestand lautet schließlich wie folgt:
Optimaler Bestand = optimale Bestellmenge + Mindestbestand + Sicherheitsbestand
Beispiel für die Berechnung des optimalen Lagerbestands
Die oben genannten Formeln können leicht anhand eines konkreten Beispiels verdeutlicht werden. Ein Unternehmen benötigt 80.000 Schrauben pro Jahr zur Herstellung von Metallblechen, die es anschließend vertreibt.
Jede Bestellung, die das Unternehmen bei seinem Schraubenlieferanten aufgibt, kostet 100 Euro, während die Kosten für die Lagerung einer Schraube mit 5 Cent pro Jahr veranschlagt werden. Welches ist also der optimale Lagerbestand an Schrauben, der in den Anlagen vorhanden sein sollte?
Wie bereits erläutert, besteht der erste Schritt zur Berechnung des optimalen Bestands darin, die optimale Bestellmenge zu ermitteln. Unter Verwendung der Formel, in der K (Kosten für jede Bestellung) 100 €, D (die jährliche Nachfrage) 80.000 Schrauben und G (die Kosten pro Einheit für die Lagerung einer Schraube) 0,05 € entspricht, ergibt Q einen Wert von 17.888 Schrauben. Das bedeutet, die optimale Bestellmenge für das Unternehmen sind 17.888 Schrauben pro Bestellung.
Q (optimale Bestellmenge) = √((2 x 100 x 80.000) / 0,05) = 17.888 Schrauben
Zur Berechnung des optimalen Lagerbestands muss anschließend der im Lager vorhandene Mindestbestand bestimmt werden. Dazu muss ermittelt werden, wie viele Schrauben das Unternehmen pro Zeiteinheit (pro Tag) benötigt. Angenommen, dass Unternehmen arbeitet an 250 Tagen im Jahr, ergibt sich, dass es 320 Einheiten pro Tag benötigt. Wenn die Lead Time des Lieferanten nur eine Woche beträgt, beträgt der erforderliche Mindestbestand folglich 2240 Stück.
Mindestbestand = (80.000/250) x 7 = 320 x 7 = 2.240 Schrauben
Abschließend wird der Sicherheitsbestand des Lagers berechnet. Wenn die maximale Lieferzeit von einem Lieferanten unter anormalen Bedingungen 21 Tage beträgt, sollte der Sicherheitsbestand 4480 Schrauben betragen.
Sicherheitsbestand = (21-7) x 320 = 4.480 Schrauben
Demzufolge beträgt der optimale Lagerbestand 24.608 Schrauben und ergibt sich aus der Addition der optimalen Bestellmenge (17.888), des Mindestbestands (2240) und des Sicherheitsbestands (4480).
Optimaler Lagerbestand = 17.888 + 2.240 + 4.480 = 24.608 Schrauben
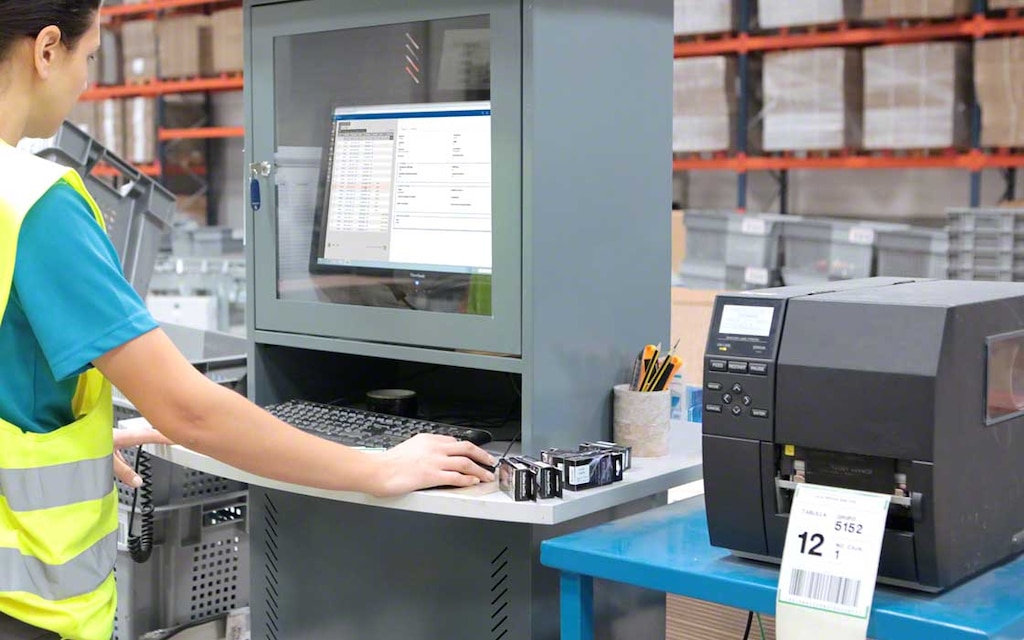
Digitalisierung des optimalen Lagerbestands
Durch die Digitalisierung von Logistikprozessen konnten zahlreiche Aufgaben automatisiert werden, die vor einigen Jahren noch Fehler und Zeitverluste für die Bediener bedeuteten. Die Implementierung eines ERP-Systems (Enterprise Resource Planning System) ist der Schlüssel für die integrierte Verwaltung von Aufträgen im Lager. Mit ihm kann u. a. der Bedarf jedes Produkts und die Lead Time der einzelnen Lieferanten ermittelt werden. Das ERP-System unterstützt also den Logistikleiter bei der Berechnung des optimalen Lagerbestands und des optimalen Bestellvolumens für jeden Lieferanten.
Sobald der optimale Lagerbestand für jede der Artikelarten berechnet wurde, kann ein Lagerverwaltungssystem (LVS) automatisch Prioritäten setzen, für Prozesse wie die Wiederauffüllung an Kommissionierstationen, die Annahme von Eingangsaufträgen im Lager und sogar für die Verwaltung der Produktionslinie in der Anlage.
Darüber hinaus legen diese Anwendungen den optimalen Bestand für jede Artikelart fest, wodurch automatisch Wiederauffüllungsaufgaben für die Artikelarten erstellt werden, die unter dem voreingestellten Grenzwert liegen. Ein LVS lagert ebenfalls automatisch die Produkte im Lager anhand deren Merkmalen (Produktumschlag, Charge oder Verfallsdatum) ein, wodurch Fehler reduziert und die Produktivität der Anlage erhöht werden.
Präzision und Flexibilität: der Knackpunkt der Logistik 4.0
Vor dem Hintergrund eines immer anspruchsvolleren logistischen und industriellen Umfelds müssen Logistikleiter die Kosten für Einlagerung und Auftragszusammenstellung senken, um wettbewerbsfähig zu bleiben. Aus diesem Grund werden durch die Verwendung von Hilfsmitteln wie dem optimalen Lagerbestand Fehler und Mehrkosten vermieden, sodass sichergestellt ist, dass genügend Lagerbestand vorhanden ist, um die Nachfrage für jede Artikelart zu decken, ohne dass unnötige Kosten entstehen.
Darüber hinaus werden in immer mehr Lagern Lösungen zur Automatisierung der Abläufe eingesetzt. Sobald der optimale Lagerbestand berechnet worden ist, ermöglicht ein LVS zusammen mit einem ERP die Planung von Aufträgen an Lieferanten, die zeitliche Einteilung von Wiederauffüllungsaufgaben an den Stellplätzen und zahlreiche weitere fortschrittliche Funktionalitäten.
Wir bei Mecalux haben Easy WMS entwickelt, ein LVS mit zahlreichen Anwendungen für den Logistiksektor. Möchten auch Sie die Prozesse in Ihrem Unternehmen effizienter gestalten und eine optimale Kontrolle über Ihr Lager erhalten, dann kontaktieren Sie uns. Einer unserer Experten wird Sie über die beste digitale Lösung für Ihr Unternehmen beraten.