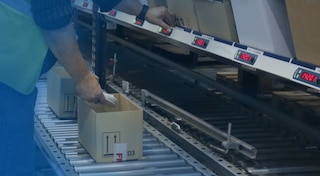
5 Beispiele für die Poka-Yoke-Methode
Bei Poka-Yoke handelt es sich um eine Technik des Continuous Improvement, die zwei grundlegende Ziele verfolgt: zum einen die Vermeidung unbeabsichtigter Fehler in Produktions- und Logistikprozessen und zum anderen die Korrektur von Ineffizienzen, falls diese auftreten.
Aufgrund des Omnichannel-Modells müssen Unternehmen heute eine sehr hohe Anzahl von Aufträgen pro Tag in kürzester Zeit zusammenstellen und ausliefern. Aus diesem Grund versuchen Lagerleiter stets, potenzielle Störungen zu vermeiden, die zu Verzögerungen und zum Verlust des Kundenvertrauens führen.
Doch wie trägt Poka-Yoke dazu bei, Kommissionierfehler zu vermeiden? In diesem Artikel wird erläutert, worum genau es sich bei dieser Methode handelt, und es wird anhand von fünf Beispielen veranschaulicht, wie sie angewendet werden kann.
Was bedeutet Poka-Yoke?
Die Poka-Yoke-Methode wurde 1960 in einer Fabrik von Toyota in Japan entwickelt und heißt wörtlich übersetzt „unglückliche Fehler vermeiden”. Es handelt sich um eine Technik des Continuous Improvement, die der Vermeidung von Fehlern in sämtlichen Produktions- und Logistikprozessen dient.
Poka-Yoke umfasst Strategien zur Verfeinerung und Optimierung von Verfahren in einem Lager oder einer Produktionsstätte, wie z. B. die 5S der Kaizen-Methode.
Sie kann auch auf Objekte angewandt werden, die speziell entwickelt wurden, um menschliches Versagen einzudämmen, wie z. B. USB-Kabel, die zur Übertragung von Daten und zum Aufladen von Geräten verwendet werden. Diese können nur mit der richtigen Seite nach oben in den Port eingesetzt werden, sonst können sie nicht verwendet werden
Der Ingenieur Shigeo Shingo entwickelte diese erfolgreiche Arbeitsphilosophie mit dem Ziel, Ineffizienzen in den Produktionsprozessen zu vermeiden. Durch die Anwendung von Praktiken, die die Arbeit der Bediener vereinfachen und Ablenkungen minimieren, können sie sich voll und ganz auf ihre Aufgaben konzentrieren.
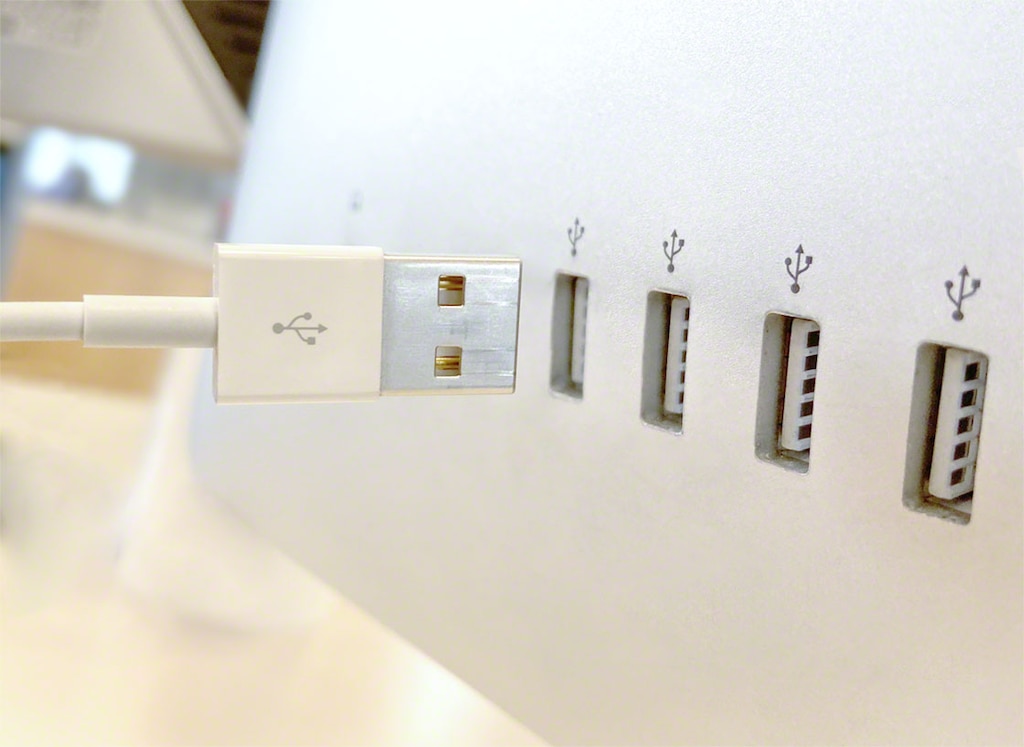
Umsetzung von Poka-Yoke
Die Schlüsselfrage lautet also: Wie setzt man Poka-Yoke ein, zum Beispiel in einer Produktionsstätte oder einem Lager? Zunächst gilt es, die einzelnen Prozesse zu ermitteln und zu untersuchen. In dieser Analyse wird die Art und Weise betrachtet, in der die einzelnen Vorgänge durchgeführt werden, mit besonderem Schwerpunkt auf mögliche Störungen.
Dann wird der richtige Poka-Yoke-Ansatz gewählt, d. h. eine Lösung, die mögliche Störungen minimiert oder verhindert. Es wird auch davon ausgegangen, dass es unvermeidliche Fehler gibt. Für diese Fälle wird ein Erkennungs- und Reaktionssystem entworfen, um ihre Auswirkungen zu verringern.
Schließlich wird der Vorgang verfolgt, um zu überprüfen, ob die Poka-Yoke-Methode und ihre Umsetzung funktioniert haben.
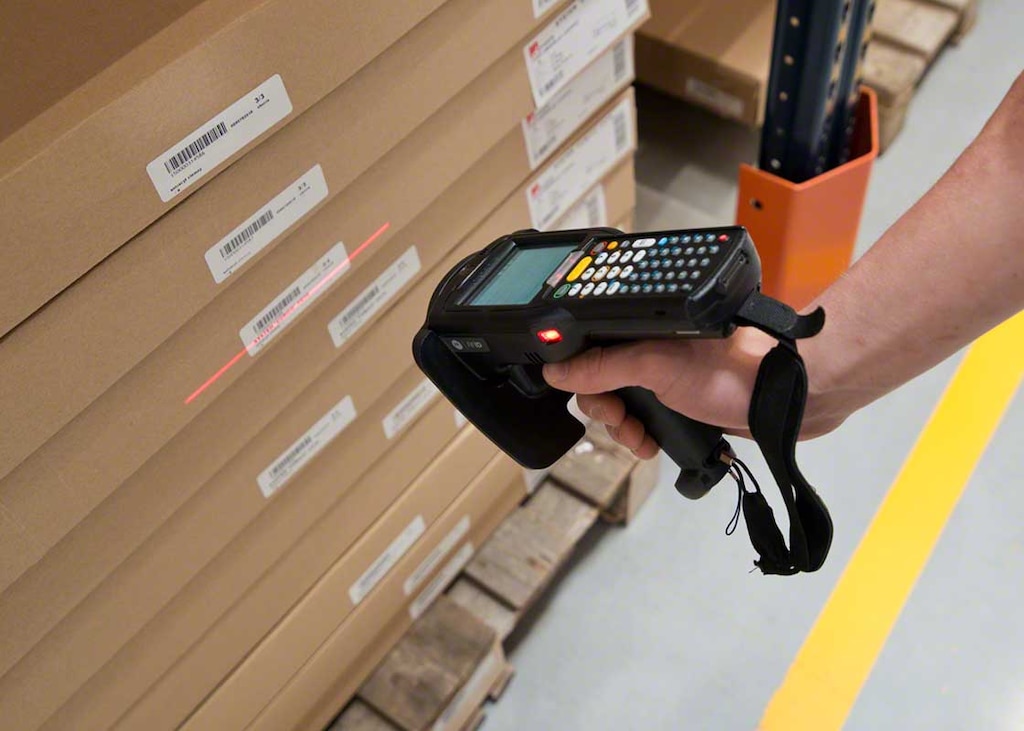
Arten von Poka-Yoke
Poka-Yoke lässt sich in vier Arten einteilen:
- Sequenziell. Diese Art basiert auf der Bewahrung einer Ordnung bzw. einer Sequenz bei einem Prozess. Wird diese nicht erfüllt, kann die Aufgabe nicht abgeschlossen werden und es ist daher unmöglich, zum nächsten Prozess überzugehen.
- Informativ. Die klare, einfache und direkte Information hilft den Bedienern, die verschiedenen Vorgänge fehlerfrei auszuführen.
- Gruppiert. Diese Art der Methode besteht in der Vorbereitung von Sets mit allen Materialien und Teilen, die für die Durchführung eines Vorgangs erforderlich sind. Auf diese Weise verlieren die Bediener keine Zeit mit der Suche nach den zu verwendenden Materialien, da sie diese bereits alle zur Hand haben.
- Physisch. Hierbei handelt es sich um Änderungen in der Nutzbarkeit bestimmter Geräte mit der Absicht, Fehler zu vermeiden. Zum Beispiel können Waschmaschinen oder Mikrowellen erst dann in Betrieb genommen werden, wenn die Türen richtig geschlossen sind oder eine bestimmte Reihenfolge eingehalten wurde (Auswahl von Temperatur, Minuten, Programm usw.).
Bei all diesen Maßnahmen besteht das eigentliche Ziel darin, Fehler bei sich wiederholenden Tätigkeiten oder bei Prozessen zu vermeiden, bei denen die Bediener aufgrund von Unwissenheit oder mangelnder Kenntnis Fehler machen können. Auf diese Weise können sich die Bediener auf ihre Arbeit konzentrieren, anstatt Zeit mit der Überprüfung oder Korrektur von Ineffizienzen zu verschwenden.
Fünf Beispiele für Poka-Yoke mit dem Schwerpunkt Logistik
Eigentlich gibt es keine festen Regeln, wenn es um die Gestaltung von Poka-Yoke geht. Die angewandten Praktiken oder die zur Fehlerbeseitigung verwendeten Gegenstände hängen vom Einfallsreichtum der an jedem Prozess beteiligten Personen ab.
Nachstehend wird anhand einiger Beispiele aufgezeigt, welche Methoden des Poka-Yoke am häufigsten in einem Lager angewendet werden. Im Logistiksektor ist Poka-Yoke Teil der so genannten Lean Logistik, d. h. einer Arbeitsweise, die darauf abzielt, die wertschöpfenden Logistikprozesse zu stärken, um Kosten zu senken.
Beispiel 1: Sequenzielles Poka-Yoke mit einer Lagerverwaltungssoftware
Eine Lagerverwaltungssystem (LVS), wie Easy WMS von Mecalux ermöglicht es, die Abläufe zu optimieren und die Bediener so anzuleiten, dass sie ihre Aufgaben so schnell und effizient wie möglich ausführen können.
Das LVS kann als sequenzielles Poka-Yoke fungieren, da die Bediener mithilfe der Handscanner nacheinander den Anweisungen des LVS folgen. Dieses System zeigt ihnen Schritt für Schritt an, was zu tun ist, und die Bediener müssen wiederum bestätigen, dass sie jeden Vorgang ausgeführt haben, um weitere Aufträge zu erhalten.
Beispiel 2: Informatives Poka-Yoke mit Pick-to-Light-Geräten
Die Auftragszusammenstellung ist einer der Vorgänge im Lager mit dem größten Fehlerrisiko. Aufgrund der körperlichen Ermüdung der Bediener, der Ähnlichkeit der Produkte oder der Regale können Fehler auftreten (Aufträge mit fehlenden oder falschen Artikeln oder mit der falschen Menge usw.).
Eine Lösung zur Vermeidung von Kommissionierfehlern ist der Einsatz von Pick-to-Light-Geräten. Diese Technologie, die Teil des informativen Poka-Yoke ist, zeigt klar und deutlich an, welche Produkte in welcher Menge zu kommissionieren sind. So soll die Arbeit der Bediener fehlerfrei gestaltet werden.
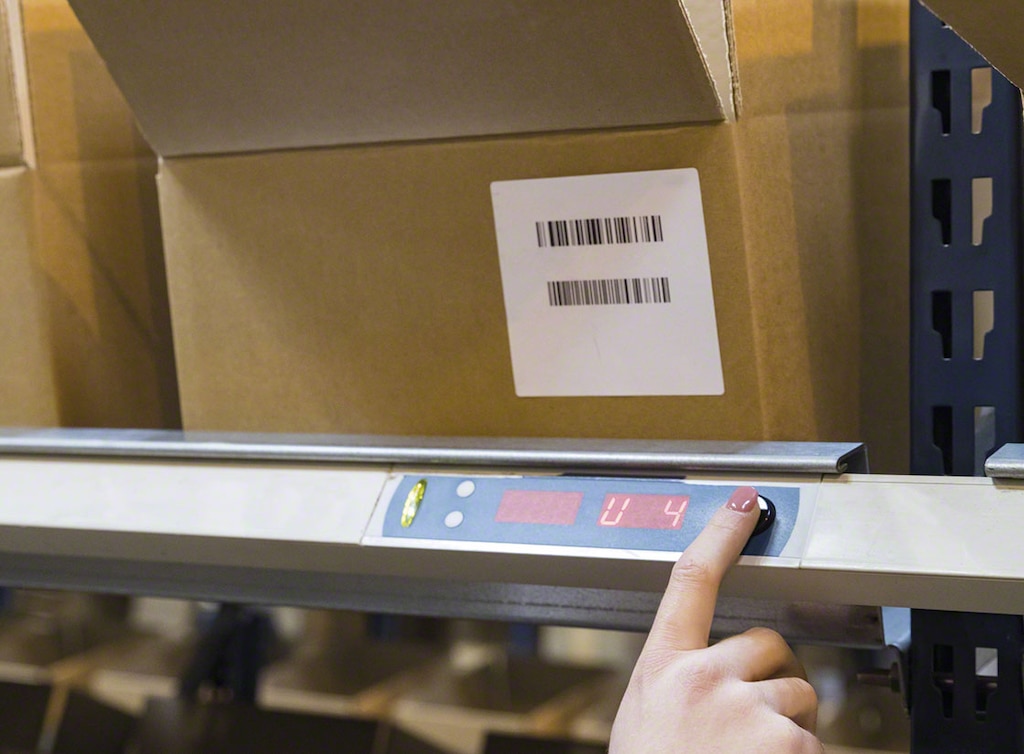
Beispiel 3: Gruppiertes Poka-Yoke beim Kitting
In vielen Lagern wird Kitting durchgeführt. Bei diesem Prozess, werden zunächst die einzelnen Teile, aus denen ein Produkt besteht, zusammengetragen und dann wird aus der Gesamtheit der Teile ein Packstück erstellt. Auf diese Weise können andere Bediener den endgültigen Artikel zusammensetzen, ohne erst nach Einzelteilen suchen zu müssen.
Hierbei handelt es sich um ein gruppiertes Poka-Yoke, da an den Montagestationen die Bediener über alle Materialien verfügen, die für die Herstellung des Produkts erforderlich sind, und sich nicht durch das Lager bewegen müssen, um die verschiedenen Komponenten ausfindig zu machen.
Die Zusammenstellung der Sets im Voraus sorgt für Schnelligkeit und Präzision. Die Zusammenstellung eines Artikels wird fortgeführt, bis alle Komponenten zusammengebaut sind.

Beispiel 4: Physisches Poka-Yoke dank Schutzzäunen
Das häufigste physische Poka-Yoke in einem Lager sind Schutzzäune. Ihre Hauptfunktion besteht eher darin, Unfällen vorzubeugen als Fehler zu vermeiden.
Die Bereiche, in denen automatische Handhabungsgeräte, wie z. B. Regalbediengeräte, betrieben werden, sind geschützt, um den Zugang von nicht autorisiertem Personal zu verhindern. In dem Moment, in dem eine Person diese Bereiche durchquert und den Arbeitsbereich eines Regalbediengeräts betritt, sei es zu Wartungszwecken oder aus Versehen, hält das Gerät an.
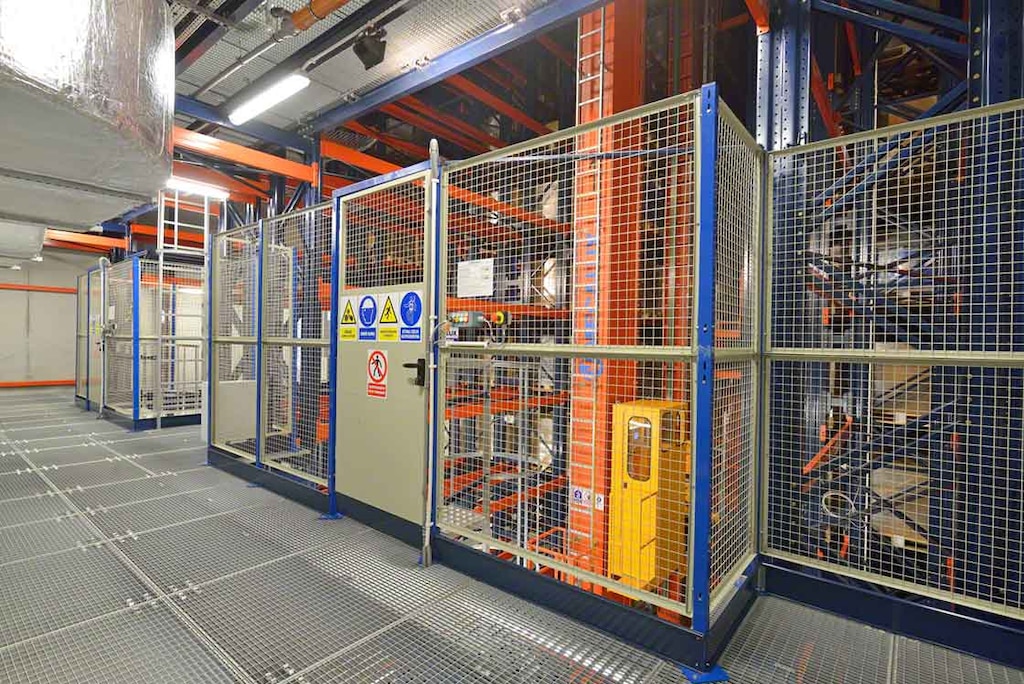
Beispiel 5: Physisches Poka-Yoke mit Kommissionierwagen
Ein weiteres häufiges physisches Poka-Yoke in Lagern sind Kommissionierwagen. Diese weisen in der Regel spezifische Abmessungen auf, die von der Größe der Produkte und Aufträge abhängen.
Wird in einem Lager eine Kommissionierung in Wellen durchgeführt, werden diese Wagen zusätzlich in so viele Stellplätze aufgeteilt, wie die Welle Aufträge hat. Auf diese Weise entspricht jeder Stellplatz einem Auftrag, wodurch Fehler vermieden werden.
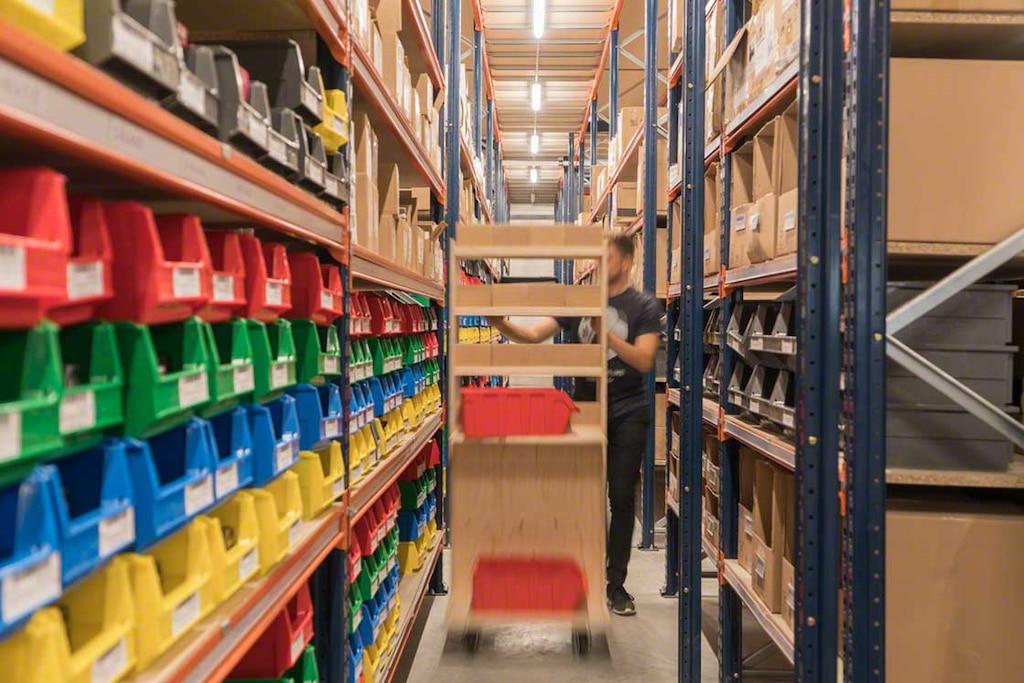
Vermeidung von Fehlern und Verbesserung der Qualität
Poka-Yoke umfasst die Anwendung von Techniken zur Vermeidung von Fehlern, insbesondere bei Vorgängen, die sich wiederholen. Sie sind durch Gegenstände und Geräte nicht nur Teil unseres täglichen Lebens, sondern auch in Lagern und Produktionsstätten zu finden.
Ziel von Poka-Yoke ist es, die Qualität der Prozesse und damit die Qualität des Services sowie des Endprodukts zu erhöhen. Dies führt zu einer höheren Kundenzufriedenheit.
Wir bei Mecalux verfügen über eine langjährige Erfahrung in der Entwicklung von Lagersystemen, die den Betrieb Ihres Lagers vereinfachen und ihm mehr Leistung verleihen können. Kontaktieren Sie uns, damit wir gemeinsam mit Ihnen ein effizientes Lager entwerfen, in dem kaum Fehler auftreten können.