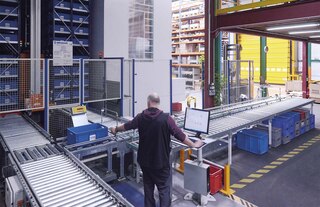
Wie lässt sich der PDCA-Zyklus (Demingkreis) in der Logistik anwenden?
Der Demingkreis oder PDCA-Zyklus (Plan, Do, Check and Act) ist eine Methode zur Optimierung des Qualitätsmanagements durch die kontinuierliche Verbesserung von Prozessen im Unternehmen. Dadurch wird die Lösung von Problemen auf strukturierte und systematische Weise erleichtert.
In Deutschland wird manchmal auch vom PTCA-Zyklus gesprochen, wobei die Anfangsbuchstaben dabei für Planen, Tun, Checken und Agieren stehen.
Der Name des Zyklus stammt von dem amerikanischen Berater William Edwards Deming, der ihn populär gemacht hat, obwohl die Schöpfung seinem Mentor Walter Shewhart zugeschrieben wird. Deming, ein Experte für Qualitätsmanagementsysteme und Statistik, arbeitete in den 1950er Jahren mit Ingenieuren und Wissenschaftlern zusammen, um den PDCA-Zyklus in japanischen Unternehmen anzuwenden. Erst drei Jahrzehnte später hatte seine Methode der optimalen Qualität in der amerikanischen Industrie Fuß gefasst.
Was ist der PDCA-Zyklus?
Der PDCA-Zyklus ist ein kontinuierlicher Verbesserungsprozess, der darauf abzielt, ein Verfahren zu optimieren, indem die Ursache eines Problems lokalisiert und korrigiert wird. Der Demingkreis wird als Rad (sog. Deming-Rad) dargestellt, da er als zyklischer Prozess konzipiert ist, wie die nachfolgende Abbildung zeigt:
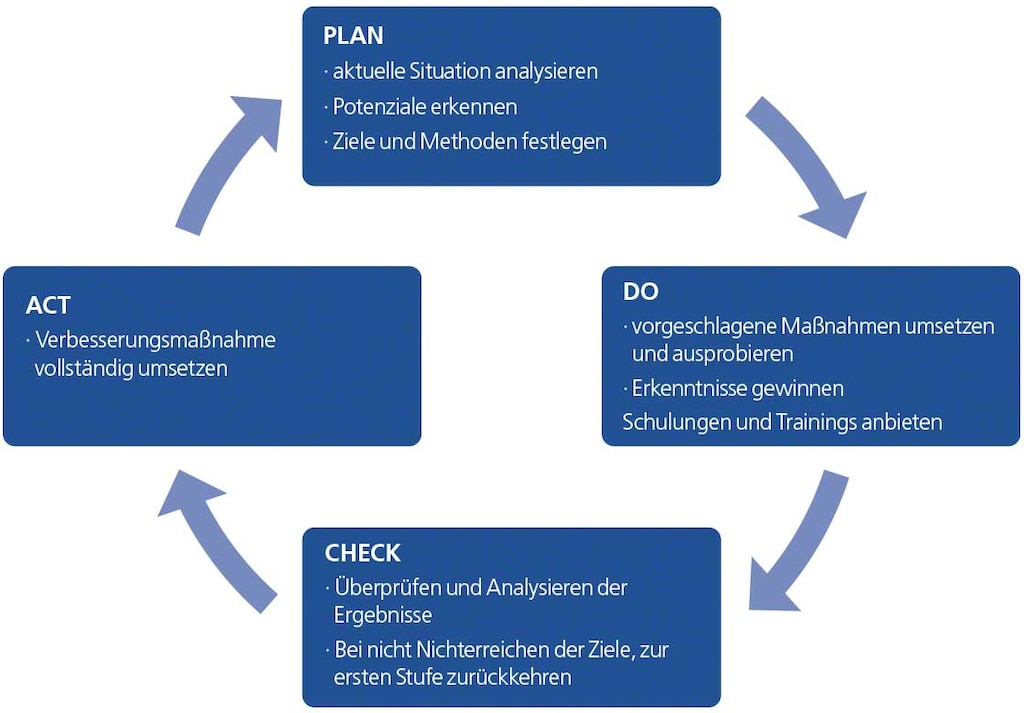
Der PDCA-Zyklus umfasst die Planung einer Verbesserungsmaßnahme eines wiederkehrenden Problems, die kontrollierte Ausführung der vorgeschlagenen Lösung, die anschließende Analyse des Vorgangs - um Unterschiede zwischen dem geplanten und dem ausgeführten Vorgang festzustellen - und schließlich die Standardisierung der entsprechenden Anpassung, um den neuen optimierten Prozess im Unternehmen zu verankern.
Die 4 Stufen des Deming-Rads auf die Logistik angewandt
Lassen Sie uns die einzelnen Phasen des PDCA-Zyklus etwas genauer betrachten:
1. Plan
Das Ziel dieser Phase ist es, das Problem oder den zu verbessernden Prozess zu definieren. In der Logistik gibt es einige Situationen, die eine Anwendung des Demingkreislaufes erforderlich machen können, wie beispielsweise Fehler im Bereich des Picking und Packing, Verzögerungen bei der Auftragsvorbereitung, eine hohe Retourenquote oder die Lieferung beschädigter Pakete. Eine umfassende Kontrolle des Lagers anhand einiger definierter Parameter ist demnach notwendig, um mangelhafte Vorgänge zu identifizieren.
Diese Phase des PDCA-Zyklus lässt sich in drei Teilprozesse gliedern:
1. Aktuelle Situation analysieren und Potenziale erkennen: Hier werden die Ursachen des Problems identifiziert und nach dem Warum gefragt. Die Anwendung des Pareto-Prinzips kann hier von Nutzen sein. Ebenso wie bei der ABC-Analyse des Lagers kann diese Regel auch dazu verwendet werden, Schwerpunkte festzulegen, die sich aus einem logistischen Problem ergeben. In der Regel wird der Großteil der negativen Folgen eines Problems (80%) durch einige wenige Ursachen (20%) erzeugt.
2. Messbare Ziele festlegen: Sie müssen konkret, erreichbar, relevant und ergebnisorientiert sein und es sollte ein Zeitrahmen für ihre Bewertung bestimmt werden. Diese Ziele können auf Erfahrungswerten basieren, die das Unternehmen durch die Festlegung von KPI oder Schlüsselindikatoren erfasst hat, oder auf Branchendaten, die aus Benchmarking-Ergebnissen abgeleitet werden.
3. Maßnahmenplan vorbereiten: Dazu gehört das Prüfen und Auswählen der am besten geeigneten Verbesserungsmöglichkeiten, der Verantwortlichen für die einzelnen Maßnahmen und der Umsetzungsfristen. Man kann es als eine Art Probelauf betrachten, der auf die übrigen Bereiche ausgeweitet wird, wenn die Ergebnisse zufriedenstellend sind.
2. Do
Die zweite Phase des PDCA-Zyklus wird auch als Testphase bezeichnet. Hier werden die identifizierten Strategien umgesetzt und die Ursachen des Problems beseitigt. Um einen reibungslosen Ablauf zu gewährleisten, sollten Anweisungen und Schulungen für die beteiligten Mitarbeiter vorbereitet und Abweichungen vom ursprünglichen Plan erfasst werden.
3. Check
Ziel dieser Phase ist es, die Ergebnisse zu bewerten und die umgesetzte mit der vorgeschlagenen Maßnahme zu vergleichen. Die gesammelten Informationen werden in der Regel mittels Visualisierungstools als Grafiken und Diagramme dargestellt. Ein wichtiger Punkt hierbei ist die Einhaltung der festgelegten Fristen, um keine voreiligen Schlüsse zu ziehen.
Nach dieser Auswertung der Ergebnisse können zwei Situationen eintreten:
- Das Ziel wurde erreicht, so dass der PDCA-Zyklus in die nächste Phase der Anpassung eintritt. Es ist wichtig, auch die anderen Parameter zu überprüfen, damit es keine "Nebenwirkungen" gibt, d. h. keine Probleme in anderen Bereichen entdeckt oder verstärkt wurden.
- Das Ziel wurde nicht erreicht: Wenn der Grund dafür ist, dass der Plan nicht ordnungsgemäß umgesetzt wurde, muss man zur vorherigen Phase zurückgehen und die Erarbeitung des Plans genau überprüfen. Ist dies nicht der Grund, ist es notwendig, bis zum Anfang des Demings-Rads zurückkehren und die Ursachen, die zu dem Problem geführt haben, erneut zu analysieren.
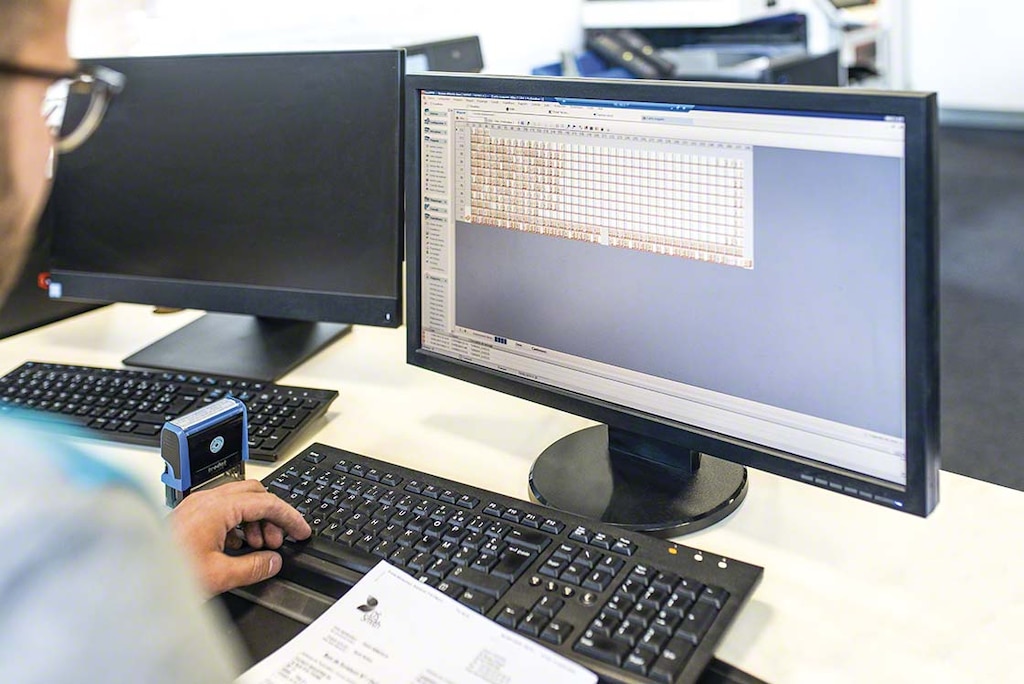
4. Act
Sobald sich der Zyklus als wirksam erwiesen hat, muss die Änderung dokumentier, standardisiert und kontrolliert werden. Diese Informationen sollten dem Personal zur Verfügung gestellt werden, z. B. durch Schulungen. Für eine umfassende Überwachung neuer Prozesse ist es auch erforderlich, die entsprechenden KPI zu bestimmen.
Außerdem sollten neue Geräte nach ihrem Test auf breiter Ebene eingesetzt werden. Wenn sich der Pilotversuch mit sprachgesteuerten Kommissioniergeräten als wirksam hinsichtlich der Reduzierung von Fehlern in der Kommissionierung erwiesen hat, sollte der Logistikleiter deren Einsatz durch alle Bediener in Betracht ziehen.
Vorteile des PDCA-Zyklus
Die zentralen Vorteile der Anwendung des PDCA-Zyklus sind:
- Es handelt sich um eine standardisierte Methode, die in jedem Geschäftsbereich zur Lösung wiederkehrender Probleme eingesetzt werden kann.
- Sie spart Zeit bei der Suche nach der bestmöglichen Lösung.
- Sie dient als Leitfaden, um die vollständige Durchführung eines Projekts sicherzustellen.
- Sie garantiert eine detaillierte Analyse der häufigsten Fehler zu deren Behebung.
- Sie ermöglicht die Kontrolle und Dokumentation der Umsetzung neuer Prozesse.
- Mit dem PDCA-Zyklus werden Maßnahmen zur Beseitigung der Ursachen eines Problems festgelegt, unabhängig von personellen Veränderungen.
- Die Methode fördert die Teamarbeit dank der aktiven Einbeziehung aller Beteiligten.
Wie verbessert der Demingkreis die Qualität der Logistik eines Unternehmens?
In der Logistik bedeutet Qualität, die Kundennachfrage zu den niedrigsten Kosten zu befriedigen, ohne dass das Serviceniveau zu irgendeinem Zeitpunkt beeinträchtigt wird. Entscheidend ist das optimale Verhältnis zwischen Kosten und Servicequalität.
Die Kosten von Qualität und „Nicht-Qualität”
Mit diesem Konzept sind zwei Arten von Kosten verbunden:
- Qualitätskosten: Dies sind die Kosten für die Erzielung der geforderten Qualität. Es handelt sich zum Beispiel im Lager um die Kosten im Zusammenhang mit der Umsetzung eines industriellen, vorbeugenden Wartungsplans für die Instandhaltung der Systeme.
- Fehlerfolgekosten („Nicht-Qualität”): Dies sind die Kosten, die durch die mangelnde Qualität der Prozesse entstehen. Ein Beispiel wären Verluste infolge von Maschinenstörungen oder -ausfällen.
Werkzeuge für eine effiziente Lagerverwaltung
Die Qualitätsverbesserung ist ein stetes Ziel in der Logistik, denn sie ist gleichbedeutend mit Produktivitätssteigerung. Das oberste Ziel ist es, die Dinge gleich beim ersten Mal richtig zu machen. Zu diesem Zweck ist die Anwendung von Methoden wie dem PDCA-Zyklus auf Prozesse im Lager der entscheidende Faktor für die Steigerung der logistischen Effizienz des Unternehmens.
Die Umsetzung des Demingkreises kann durch neue Systeme und Ausrüstungen ergänzt werden, um alle Prozesse der Anlage zu optimieren. Die Installation eines LVS im Lager verbessert die Anwendung dieser Methode, da dieses System automatisch eine große Menge an Informationen sammelt und verarbeitet.
Darüber hinaus erleichtern Tools wie Supply Chain Analytics die Analyse dieser Daten durch benutzerdefinierte Dashboards und Diagramme, was die Effizienz in kritischen Phasen wie z. B. dem Warenein- und ausgang, der Auftragsvorbereitung oder dem Bestandsmanagement etc. erhöht.
Technologische Innovation erhöht die Wirkung des PDCA-Zyklus
Das übergeordnete Ziel hinsichtlich der Logistikqualität besteht darin, eine kontinuierliche Verbesserung der Dienstleistung zu erreichen, indem die Kosten so weit wie möglich angepasst werden. Zwei von zehn Befragten der Deloitte-Umfrage Supply Chain Digital and Analytics Survey betrachten die Senkung der Logistikkosten als vorrangiges Ziel ihres Interesses für Datenanalyse-Tools.
Die Prozessüberwachung stellt sicher, dass der PDCA-Zyklus reibungslos abläuft und durch den Einsatz von IT-Systemen effektiver angewendet werden kann. Wenn Sie die Vorteile eines Lagerverwaltungssystems im Detail sehen wollen, kontaktieren Sie uns und wir zeigen Ihnen eine personalisierte Demo-Version.